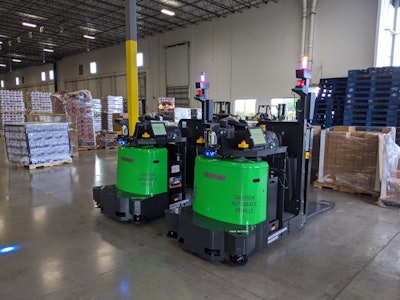
For years, food and beverage warehouse workers have been incentivized to be as productive as possible and were rewarded with engineered rates. Today, however, the food and beverage industry is in the midst of a radical transformation in everything from agriculture to processing facilities, trucking to long-term storage and last-mile delivery. Combine that with proliferating SKUs, changing customer expectations for faster delivery and wider selection, and the impacts of the Coronavirus disease (COVID-19) pandemic, and it's time to rethink this dated incentive strategy.
In an age when shifts can and do happen in the blink of an eye, automation offers the chance to revisit how work is done and how to keep workers safe. It also provides the tools to nimbly adjust operations in response to current events. The most successful organizations will blend human creativity and automation to improve operational efficiencies, increase output and grow revenues.
The difficulty with engineered labor standards
Engineered rates originated from the need to incentivize workers to do dull, dirty and dangerous jobs. For top performers, engineered rates are an excellent way to earn. However, the challenge is that Engineered Labor Standards compel workers to work faster while completing routine tasks on heavy machinery notorious for blind spots. For decades, this mix of high-speed travel and monotonous tasks resulted in injury, inventory damage and even death. In a large food warehouse, it only takes a momentary lack of focus when moving a pallet of food to create a potential safety incident.
By deploying autonomous mobile robots (AMRs), food and beverage warehouses can offset the amount of manual traffic operating in a facility every day, thereby reducing the chance for human error. At a time when brownfield and greenfield development is pushing the size of warehousing and distribution facilities ever larger, AMRs can step in and take on the long-distance hauling.
AMRs also use 360-degree sensors for protection and enhanced obstacle detection and avoidance. If an individual or machine gets too close, an AMR will slow down, find an alternate path to avoid the obstacle, or safely stop to avoid a collision.
While the automation of repetitive tasks is great for increased safety, it's also proven to increase worker satisfaction. With AMRs, workers are no longer moving tons of pallets of products each day, trying to keep up with their engineered rates. Operators can be reassigned to tasks that require more critical thinking, problem-solving, and creativity, like mixed pallet building and exception handling. Robots, in turn, provide reliability and ROI by automating these repetitive tasks with greater efficiency.
More SKUs, pallets and trucks
Another driver of transformation is that food and beverage organizations are experiencing more complex order profiles than ever before. Inbound orders of more SKU's, half pallets, outbound orders of rainbow pallets, perishable items and shorter turnaround times create a dizzying logistics problem. Moreover, this increased level of picking, packing and scheduling can often lead to dock congestion.
AMRs and artificial intelligence (AI) can simplify these logistical hurdles. AMRs automate repetitive tasks at flow-through warehouses by moving goods away from dock doors to areas where inbound pallets can be broken down and outbound pallets can be rapidly built, keeping products moving throughout the warehouse quickly. And, since smaller pallets often require shrink wrapping for safety and transport, AMRs can interface with other industrial equipment like conveyors and wrappers.
Beyond simplifying tasks, AI-powered automation software can integrate into warehouse management systems (WMS) and have the "brains" to orchestrate workloads between robots, human workers and manual equipment based on the most pressing need at the moment.
For example, while humans are great at local optimization and solving edge cases with creativity, such as a product spill or machine error, orchestration software can view the warehouse at a system-wide level. So, if a loading dock is crowded due to an unexpected spike in inbound shipments, this AI-powered engine can assign tasks in real-time to the right resource to ensure workflow at the loading dock flows seamlessly.
Combating COVID-19
Today, worker safety and productivity is about so much more than industrial accidents. Recent news demonstrates that employees across the food supply chain are no exception when it comes to concerns about COVID-19. AI, AMRs and automated guided vehicles (AGVs) can help keep workers safe amid the pandemic.
AI-powered orchestration software can be used to allocate tasks across every resource in a warehouse, including employees, AMRs and other manual equipment. These powerful engines can consider social distancing constraints while automating multiple tasks. Given a parameter for minimum spaces between workers, this software will determine the best approach to task allocation to decrease close human interaction. This allocation supports human workers by enforcing health and safety guidelines throughout the workday. And, since the orchestration software is also capable of issuing assignments in an incredibly efficient way, it helps improve productivity while reducing worker fatigue and eliminating crowded conditions.
Additionally, unlike their human counterparts, robots are impervious to disease and help create a natural buffer between employees. Self-driving industrial vehicles offer the chance to reimagine workflows and find novel ways to automate repetitive and straightforward tasks that would previously create close human contact, such as line side delivery or goods to person.
For example, grocery is almost exclusively a picking and replenishment application – something that is predominately done manually. Greenfield development is a prime area to revisit the traditional approach to building rainbow pallets in order to reduce worker density and proximity. One method is to implement a break pack workflow where pallets are broken down to eaches, put into totes and used to stock a goods-to-person AMR system. AMRs can be put to work, pulling totes from standard racking and delivering goods to person. During peak time, people can also be deployed to aisles to handle the typical 50-75% spike in throughput. Using this system, organizations can largely keep people in their stations while safely improving throughput.
Moving forward, food and beverage warehouses need to realize that automation solutions are not only impervious to diseases and disruption, but they can also help keep workers safe, improve job satisfaction and enable humans to focus on higher-level initiatives, all while improving productivity and efficiency. This is crucial to remain competitive, especially in today’s unprecedented times.