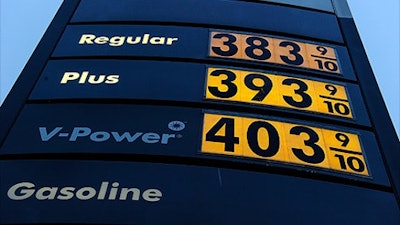
According to the U.S. Energy Information Administration, the United States, Russia and Iran are the world’s largest producers of natural gas. Therefore, as geopolitical conflicts continue to escalate in these EMEA regions, challenges threatening global businesses, including key food industry players, are multiplying rapidly.
In 2021 alone, Europe relied on Russia for 40% of its natural gas, but recent sanctions will demand that European nations seek alternative providers for their natural gas needs. Even countries that do not rely on Russia for natural gas, like the United States and UK, will feel the mounting pressure as global gas prices soar while Russia simultaneously restricts its supplies to mainland Europe.
Across the pond, the United States has experienced a hotter-than-average summer, compounded with a lack of alternative energy sources, leaving its oil inventories below the seasonal average. Less supply and more demand signals higher gas prices to come this winter for both consumers and manufacturers. Consequently, the price of heating homes and producing food for the public will likely increase significantly.
To mitigate the impact of a gas catastrophe, food industry manufacturers should deploy cutting-edge, artificial intelligence (AI)-based, predictive technology solutions that optimize operations and process teams and machine performance.
The dilemma
Limited access to natural gas and oil will impact every industry, the effects of which will show up on our front doorsteps. As experts examine the food industry alone, the alarms begin to sound.
The cost of fertilizer production and natural gas are linked, so as the energy market experiences inflation, the cost of producing and transporting food takes off too. Furthermore, as geopolitical contention in Eastern Europe continues, there’s a strong likelihood that grain export routes will change and aggravate concerns about food insecurity in particular markets.
Now, it is time to consider the manufacturing and supply chain side of the coin. These two sectors rely on energy at every level – from sourcing to production to transportation, etc. To keep the factory lights on, the machines running and the transportation methods moving, both industries have to maximize their available energy resources.
In the face of these economic variables, employing the same 20-year-old processes will only get the industry so far. Disruptive innovation is needed to combat and manage this level of complexity in the food manufacturing space.
Mitigating the impact with AI
The food industry is balancing a host of competing factors: product quality, volume, energy, waste and emissions. Each of these has an independent objective, sometimes conflicting with other factors. After introducing external pressures like changing environmental conditions, the economy, and shifting geopolitical concerns, industry executives now struggle to anticipate the impact on their bottom lines and juggle competing objectives.
Fortunately, to help their teams navigate the complex manufacturing situation, these executives can use AI to parse out intertwined variables with conflicting objectives. Specifically, AI-based solutions can ingest complex data sources and spot patterns and connections no human operator could ever see, empowering decision-makers to use the insights to build new strategies and adapt their operations.
However, before starting an AI implementation process, business leaders need to define clear business objectives, such as how to cut down on energy to maximize existing inventories and identify which solutions are best tailored to industrial use cases. So, what are these AI-based tools that can meet the unique needs of food industry manufacturers? Process health and machine health are two solutions that tackle different but equally important aspects of manufacturing: operations & process teams and machine performance.
Process health
To address these emerging challenges, food manufacturers can lean on process health to solve various production issues they may face on the factory floor. Process health incorporates an element of AI to use algorithms that understand production processes, so skilled workers can glean the ins and outs of production variables and optimize those factors in the face of varied objectives.
In the context of an impending gas catastrophe, process health can show how organizations can be more efficient and maximize objectives with limited resources. Algorithms can be leveraged to show predictive models to help decision-makers plan for different scenarios as the energy crisis plays out.
Additionally, process health pinpoints where losses occur and identifies prevention methods to curtail these inefficiencies in the future. These capabilities empower food industry practitioners to extract more from their processes to have clearer visibility into production and supply chain processes and make quicker decisions that lead to real impact. Finally, factory leaders must look at another essential element when creating efficient manufacturing and production practices, machinery and consider a critical predictive maintenance technology that helps keep machinery in top-notch condition -- machine health.
Machine health
Machine health equips manufacturers with data and insights needed to reduce downtime, increase production capacity and optimize the cost associated with asset care. In other words, it helps organizations use what they have more effectively.
Data can be pulled from sensors that capture vibrations, temperature, and magnetic data from machines, advanced AI diagnostics and human reliability experts. There are four stages to machine health -- monitor, diagnose, guide and act. In essence, Internet of Things (IoT)-enabled sensors capture and transmit the machine data, then AI and predictive models are leveraged to identify issues. Next, AI insights and human experts weigh in to prioritize which issues should be addressed first based on operational needs and business necessities and then users collaborate and act on guidance to make improvements.
Assessing machine health at regular intervals can provide teams with the insight needed for effective planning to mitigate potential complex issues before they arise. In addition, the data is provided in near real-time, allowing analysts to act quickly before additional costs pile up.
Understanding how your machines operate at the factory level significantly benefits the overall supply chain. Furthermore, tightening up machine and process health creates a more holistic understanding of the entire production process.
The end-to-end solution: Production health
As natural gas and oil prices surge, it's time to lean on innovative technologies and tools to continue forging the way toward your business objectives. Supply chain and manufacturing leaders must use disruptive tools to operate in an increasingly complex industry. Therefore, teams should consider leveraging AI-based solutions like process health and machine health to gain a comprehensive understanding of their production processes and reduce the effects of the impending gas catastrophe.
Process health empowers manufacturers’ operations and process teams to navigate the one-of-a-kind challenges that come with each production process, equipping them to understand previously disparate datasets and glean vital insights that were previously undetectable. In parallel, around-the-clock machine health will empower industrial users with real-time prescriptive insights to prevent machine failure and improve machine performance, in turn, reducing energy, improving efficiency and maximizing yield.
Though these cutting-edge solutions tackle different areas of manufacturing, together, process health and machine health create a new approach to production health, a combined solution which improves reliability, quality and sustainability across all production operations and aligns with critical environmental, social, governance (ESG) initiatives. Once food industry experts equip themselves with these reliable insights across their production environments, they can more confidently navigate a possible gas shortage or whatever else may linger around the corner.