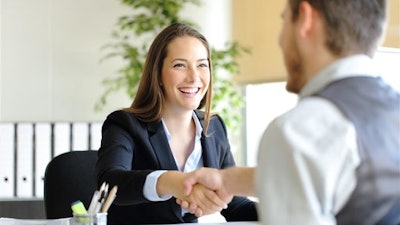
Communication in the workplace has been an evolving concept for the last century. Organizations of all kinds in all eras rely on the transfer of information between team members to be productive and stay competitive. As time goes on, flaws in old processes are identified, advents are made and industry continues with this rinse-and-repeat exercise.
Perhaps no other American industry is more beholden to its communications processes than manufacturing. Technicians, engineers and operators each own tribal knowledge -- information that only people with their core competency know and understand -- critical to the infrastructure of each manufacturing plant. It’s the transfer of that information, not only between those with varying job descriptions but also shift to shift, that is critical to the efficiency of any manufacturing plant.
But, capturing that tribal knowledge must be systemized in order to gain widespread adoption amongst an organization’s workforce, ensure that information isn’t getting lost and optimize the organization of necessary intelligence.
Here of the basic tenets of accomplishing these goals:
Gain buy-in from those who own the knowledge
If your workforce doesn’t believe in the system or technology being used to capture information, it simply won’t work. Think about it, you can throw a bunch of shovels on the ground, but they won’t dig a hole without laborers. Well, a system will only work if operators, technicians and engineers are constantly contributing to the repository of information. Just the same, supervisors need to monitor the usage of these systems or technologies and report up the chain as to the level of adoption they are seeing on the manufacturing floor and what benefits have resulted from it.
It’s important to help workers understand how they will directly benefit through the information-sharing process, whether that’s increased visibility, access to critical knowledge or reduced uncertainty and stress. Tribal knowledge is unwritten information typically held by one person or a small group. The information that an individual gains as a result of reading through a repository of information could help them become a more highly-regarded employee. It’s a givers-get concept where those who share information will get more out of the technology several times over.
Click here to hear more about visibility technology in the supply chain:
Keep things simple
The idea behind any system, process or technology is to make tasks more efficient. If it requires the workforce to undergo an arduous learning process or forces them to maneuver technological glitches, you’re unlikely to earn the aforementioned necessary buy-in. How do you avoid these pitfalls? It’s critical that the systems, tools and processes used to capture tribal knowledge are integrated with the same systems currently in use. Technicians don’t want to adopt entirely different workflows. And, moreover, that’s inefficient.
Additionally, whatever interface is being used must be as intuitive as a Fluke Multimeter. A manufacturer’s proprietary systems should be as easy to adopt as any consumer technology. Technicians aren’t going to adopt a completely separate workflow because they don’t have time to learn how a complicated interface functions. And, the technology must be reliable. Frontline workers span a spectrum of understanding when it comes to technology. Given the high-stress environment of a plant floor, frontline workers won’t have patience for unreliable technologies.
Provide value in return for workers’ efforts
Don’t look down upon workers who question the value they get out of a new process, system or technology. Embrace that sentiment and use that desire to get better to improve the overall efficiency of your manufacturing floor. Workers on the plant floor are proud masters of their respective trade and the specialized knowledge they carry. Value is drawn from career recognition and the esteem that comes with being a critical part of the operation. Demonstrate the value of the technology you’re using to capture tribal knowledge and showcase how it will help each individual more efficiently execute on their responsibilities.
Consider retrospectively showcasing success stories with the technology while addressing your workforce on the manufacturing floor. Call out and reward those who have successfully shared their tribal knowledge so that others at the same level are motivated to do the same. And, of course, explain to the collective workforce how this action ultimately benefits the entire company.
Align capturing of tribal knowledge with company and team priorities
Remember, creating a culture of knowledge-sharing takes time. While it’s important to create systems and technologies that make this more efficient, the actual task still does require all involved to dedicate time to the task. So, it’s important to get top-down buy-in on the initiative. And leadership within the organization needs to articulate the ways in which it will ultimately help a manufacturer achieve its priorities and better the overall health of a company.
And, articulating that value is critical to the introduction of any new process, system or technology on the manufacturing floor. Simply dictating a new process without facilitating an understanding as to why it’s being introduced will stymie engagement with a reporting platform. However, taking the time to explain the reasoning behind such a move, and more importantly, pointing toward the collective goals of the company will generate excitement about the possibilities of any new technology.