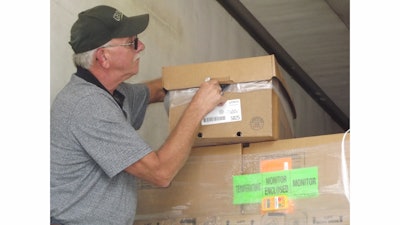
Cold chain transportation managers have more tools to manage temperature and security issues than ever nowadays, thanks to continuously improving technology. It couldn’t be happening a better time, in light of a heightened public concern about food safety and pending food transportation regulations. Transporters of fresh, refrigerated and frozen food have a plethora of hardware, software and services available to manage and monitor shipments across any distance.
As with all types of technology, the challenge facing transportation decision makers is to understand which solution best meets their needs.
While cold transporters await the Food and Drug Administration (FDA) final sanitary transport rules under the Food Safety Modernization Act (FSMA), shippers are already finding it difficult to meet existing requirements at a time when carrier capacity has hit an all-time low. Hence, shippers face growing customer concerns about safety, temperature and quality at a time when carrier demand exceeds supply.
While temperature-controlled warehouse space has increased over the years, it has not kept pace with demand, making it difficult for carriers to meet schedules. As the U.S. economy recovers from the recession, food shippers find themselves competing with other industries for transportation services.
Demand exceeds supply
Sunteck Inc., a full-service, multi-mode transportation solutions provider based in Boca Raton, Fla., manages frozen transport for a sandwich manufacturer with operations in California and Illinois. Shana Monroe, the account representative, says chilled and frozen LTL operations are becoming more difficult due largely to capacity shortages. The problem is especially difficult in California, due in part to the new CARB compliance regulations requiring diesel trucks to meet federally-imposed clean air standards. Diesel truck engines are required to be 2010 model year or newer engines. In addition, the new hours-of-service safety regulations to reduce truck driver fatigue limit the average work week for truck drivers, which has impacted capacity in a big way.
“Consignees no longer recognize LTL versus truckload and make our trucks wait for hours to unload one or two pallets,” Monroe says. “They use to have express doors to accommodate the LTL trucks. Consignees are also charging fees and steep fines that they never used to charge, such as Safeway that will charge $500 for a reschedule fee even though we’ve called ahead and reported we were held up at a previous warehouse, gave notice and needed to re-schedule.”
Moving chilled and frozen LTL can be especially challenging since product has short code dates and customers order “just-in-time” deliveries. “When shipments aren’t delivered on time, the fallout can be, at the very least, difficult for the customer. The customer may get a reduction in freight invoice or the following week's orders cancelled,” Monroe says. “We are also held to a 97 percent on-time delivery ratio from Walmart, and this does include delivering early as well. As you can see, when you pull all this together, it can create an environment that makes it almost impossible to run chilled and frozen LTL, make a profit and stay in business.”
Fewer carriers are staying in the chilled and frozen LTL arena, which is creating capacity issues, Monroe adds. “When you load a trailer out with multiple customer orders, a pallet or two for each customer, it creates multiple picks and stops. Then you have warehouses holding you up and putting you behind schedule. It is challenging to get all the shipments off loaded on time and maintain over a 97 to 98 percent on time delivery ratio, which we do maintain.”
As a result of all the recent changes, Sunteck recently purchased MercuryGate International Inc. TMS software to better manage LTL operations.
George’s, a chicken processor based in Springdale, Ark., has found operating its own reefer fleet to be most economical method of transport, according to Jeff Overstreet, director of transportation. But since the company’s fleet is limited in size, they must outsource fresh and frozen shipments to western states. So far, the company has been satisfied working with 3PLs.
“Our ability to hire the outside guys (drivers) to do the job we need to do gets tougher and tougher,” Overstreet says.
Temperature monitoring improves
George’s reefers are equipped with Sensitech’s TempTale electronic sensors that allow George’s to monitor the temperature in real time and create a temperature log for each shipment, Overstreet says. A monitor light visible to the driver from the side view mirror indicates whether or not the cargo temperature falls within the right range. George’s has the TempTale sensors on its trucks and provides the sensors to its carriers.
George’s has investigated using satellite monitoring to monitor vehicle diagnostics, Overstreet says, but has not considered this necessary.
As customers like George’s find 3PLs helpful in managing reefers, some LTLs providers think food manufacturers and wholesalers need to learn more about the technology they look to the 3PLs to help them with.
Customer education needed
John Gaudet, vice president of business development at Newfield, N.J.-based RLS Logistics, which provides temperature-controlled LTL and TL services, says some customers make the mistake of loading or unloading a reefer from the street where product is exposed to warm air. Other customers require the driver to keep the reefer unit running while the trailer doors are open. In such a case, warm moist air gets into the condenser, causing ice buildup and excessive defrost. This is especially the case in the metro areas of the Northeast where streets and buildings cannot accommodate today’s 53-foot reefers.
In still other cases, shippers place a temperature recorder on top of a pallet in an area where there is ambient air rather than within the cargo or inside the corrugated compartment. “It (the recorder) doesn’t gauge what the temperature of the product is; it’s only giving the air temperature,” Gaudet says. The customer/receiver will then refuse the order, which can result in a substantial financial loss. The cargo insurance only covers loss in the event of a reefer breakdown. “At the end of the delivery cycle, no matter where that error is, it’s always going to fall on our plate,” he says. “The cost implications are great.”
“It’ll drive transportation rates up in the LTL world,” Gaudet says. “Educating our customers about how reefer trailers work and how to properly handle freight claims is a priority right now.” His biggest concern is that these oversights will increase as the FSMA gets closer and customers become more sensitive to temperature issues, resulting in increased costs and ultimately higher freight rates.
How and when to take a shipment’s temperature remains an issue that lacks uniformity, agrees Dan Quinn, vice president of warehousing at Milwaukee, Wis.-based Midwest Refrigerated Services. If a thermometer is placed in an area that does not accurately reflect the cargo’s temperature, it can easily exceed the required temperature, causing the customer to reject the shipment. Quinn thinks that customers should go the extra step of “pulping” the product in cases where temperature on the outside of a package creates a concern.
Temperature concerns apply to rail cars as well, notes Mark Casiano, vice president of sales at Railex. The company’s practice is to “pulp,” take the product temperature, at both the start and end of its journey.
Casiano says rail car temperatures are monitored throughout the entire rail trip and that refrigerated units can be adjusted via satellite while in transit.
Technology continues to evolve
“With the new FSMA requirements, particularly safe transport, record keeping will be more critical. FDA wants to see all your records – not just the data points that got through,” says Elizabeth Darragh, senior director of global marketing communications at Sensitech “A complete breadcrumb trail will be an important tool when an inspector comes knocking.”
Darragh says while the technology for real-time monitoring has been available for years, it has recently become affordable enough to make sense for food shipments. Sensitech’s view is that customers will utilize a variety of data collection devices — including radio frequency and real-time — depending on the detail and timing required for information.
“In the real-time scenario, Sensitech’s TempTale GEO units collect data and transmit in a prescribed interval (e.g., every 10 minutes). If we are in a zone with spotty cell coverage (which we all experience with our own cell phones), the device stores the information and downloads everything when it returns into range,” she notes. Readings are not lost due to the inability to transmit, she adds.
With radio frequency, there are a number of scenarios for downloading data – via infrastructure or handheld devices in either short or longer read ranges, Darragh says. In any case, the receiver still has to find the box with the device in it or on it to read with a handheld.
“Our Sensitech’s TempTale RF products pre-installed infrastructure means no human intervention is required – the infrastructure beacons for signals within its range, which our device responds to and downloads all of the data its collected,” she says.
Witte Bros. Exchange, Inc., an asset-based 3PL based in Troy, Mo., uses a satellite-based, telematics system on its fleets to monitor refrigeration in real time, notes Charla Whalen-Mueller, director of marketing and recruitment. Operated by Rochelle, N.J-based Orbcomm, the web-based system provides visibility, monitoring and two-way control of refrigerated fleets. The service integrates with transportation companies’ dispatch, order generation or planning systems.
This technology will be important to shippers as the FSMA comes into effect, Whalen-Mueller says.
In the meantime, radio frequency identification (RFID) continues to evolve as a tracing tool. While RFID began as an inventory control technology, the electronic tags’ ability to gather more information than other tools has given it a role as way to control foodborne illness. RFID tracking can be managed by existing software systems, according to Chris Schaefer, director of market development for data capture solutions at Motorola, which provides RFID products.
After having to recall all its packaged spinach following an E. coli outbreak in 2006 that sickened 200 people, Dole Foods started RFID-tracking vegetables from harvest, through processing and packaging, and on to stores.
A Canadian meat processor, Levinoff-Colbex SEC in St. Syrille de Wendover, has deployed RFID to provide end-to-end visibility across its logistics chain. An RFID tag is associated with every animal and meat product as it moves through the company’s processing plant. If a veterinarian identifies a problem with any animal part, every other product from that same animal can be immediately located on the production line and traced back to the source animal.
The system has allowed the processor to achieve certification in the international market, according to a case study by Motorola Solutions, which provides the RFID readers, tag antennas and monitoring service.
Logistics industry observers have noted that RFID remains a very costly solution. In addition to the deployment cost, observers say that bar code readers have proven effective monitoring the necessary data for data and temperature monitoring.
Nevertheless, large companies including Walmart and government institutions are issuing RFID compliance mandates to product manufacturers, according to a recent RFID report from the University of Florida.
The July Food Logistics reported Hy-Vee, the West Des Moines, Iowa-based supermarket, now requires suppliers to include RFID tags with orders. Hy-Vee implemented what it characterizes as a complete cold chain management system to monitor temperature of perishable foods from the vendor to a distribution center to the store.
As temperature control, security and inventory management technologies evolve, food companies will be in a better position to meet customer and government concerns about safety.
George’s, the Sprindale, Ark.-based chicken processor, is grateful for the fact that the food transport industry has strong organizations such as the American Trucking Association and National Private Trucks. “The industry is very strong,” George’s Jeff Overstreet says. “We’ll keep getting food to the American consumer.”
For More Information, Contact:
MercuryGate International, 919-469-8057, mercurygate.com
Midwest Refrigerated Services, 414-410-8200, midwestrefrigerated.com
Motorola Solutions, 847-576-5000, motorolasolutions.com
Orbcomm, 703-433-6300, orbcomm.com
Railex, 888-472-4539, railex.com
RLS Logistics, 856-694-2828, rlslogistics.com
Save A Load, 800-728-5623, saveaload.com
Sensitech Inc., 978-720-2648, sensitech.com
Sunteck Transport Group, 561-988-9456, suntecktransportgroup.com
Witte Bros. Exchange, 800-325-8151, wittebros.com