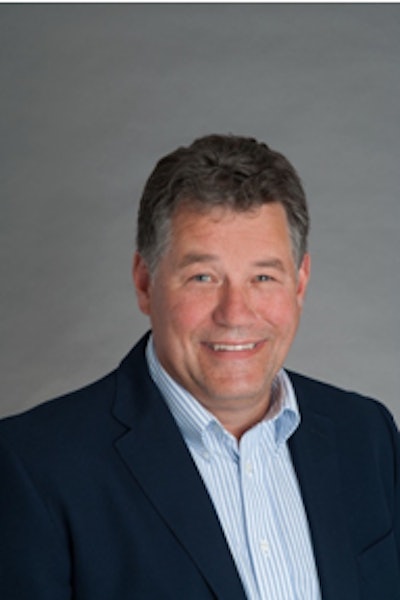
Massive amounts of energy and money go into keeping items cold in a distribution warehouse. The constant flow of air and the movement of workers, machinery, and shipments throughout the space create big challenges in maintaining consistent temperatures and predictable operational costs.
Lighting plays a significant role in every aspect of cold storage: temperature output, energy consumption, and workforce productivity.
The conventional light sources for cold storage and warehouse environments have been high-pressure sodium or metal halide high bay fixtures. The arc-tube of the lamps is designed to operate at temperatures as high as 1000 degrees C. This produces a constant heat source and places an added load on the storage refrigeration system.
In addition, the minimum re-strike time or time to maximum light output when a light is turned on is 10 to 15 minutes. Because these facilities need more responsive lighting to support the constant traffic pattern in the space, the high-pressure sodium or metal halide high bay lights are left on 24 hours a day, seven days a week.
Remember our fathers shouting from the other room, “Please turn off the light – I do not own the electric company.” Enough said.
In recent years, T5HO lamps were introduced with the ability to be turned on and off with fixture-based sensors, improved light output, and a 25 – 30 percent reduction in energy consumption. However, the extreme cold temperature of a freezer compromises the T5HO product effectiveness.
A T5HO lamp provides its most efficient light with an ambient air temperature of 95 degrees F. The low temperature of a refrigerated warehouse thus lengthens the amount of time it takes for a T5HO lamp to reach full brightness.
This significant delay minimizes the value of the fixture-mounted sensor because the T5HO lamps cannot be turned instantly on. Not only does this produce a maintenance nightmare for an already strapped facilities team, the inconsistent and dim light output compromises safety in the space and creates a less than productive work environment for the staff.
Today’s LED technology and wireless controls thrive in cold temperatures and are very directional in their light output - just like having multiple small spotlights to work with.
LED technology is a solid state device enabling instantaneous maximum light output and greatly improved energy efficiency. More importantly, the cold temperature actually lengthens the expected life of the LED light source and can be expected to last well over 100,000 hours. Add in a motion sensor and the lifetime is exponentially extended.
This significantly reduces operating and maintenance costs for a facilities team accustomed to constantly changing light bulbs in the challenging high ceilings of their space.
Many do not realize how much lighting plays a role in our daily work and home environments. From the living room to the driveway, from parking lot to warehouse aisles, a well-lit, modern atmosphere has proven to increase workforce effectiveness and satisfaction.
For today’s businesses, a properly designed and implemented LED lighting system in a cold storage facility can reduce the lighting energy consumption up to 90 percent and significantly decrease operational and maintenance costs for years to come.