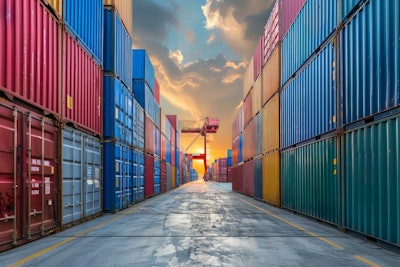
As supply chain disruptions go, the U.S. East Coast and Gulf Coast port strike, which started today, was one of the more predictable. Threats to U.S. port operations seesaw from one side of the country to the other on a six-year cycle as collective labor contracts grind toward expiration dates and efforts to negotiate new ones drag on for months without success.
Two years ago, uncertainty shrouded the West Coast, where the Pacific Maritime Association and the International Longshore and Warehouse Union (ILWU), representing 22,000 dockworkers, took more than a year to hammer out a new deal.
This time around, it’s the turn of the International Longshoremen’s Association (ILA) and 45,000 of its members at ports such as New York-New Jersey, Savannah, and Houston to rock the boat. ILA president Harold Daggett warmed of the prospect of a strike as far back as November 2023 if the United States Maritime Alliance (USMX) failed to meet the union’s demand for a 77% pay rise.
“Known Known” risks can be planned for
In supply chain risk terms, U.S. port strikes have become what the former Secretary of Defense Donald Rumsfeld referred to as a “known known.” Unlike “known unknowns” or “unknown unknowns” (also called “Black Swans”), these are risk events for which the timing and likely consequences are well understood and hence can be planned for. While the exact duration and dollar impact of a port strike can’t be known in advance, previous experience does provide some pointers. The last West Coast strike in 2015 lasted eight days and cost the Southern Californian economy alone an estimated $8 billion. The last East Coast strike in 1977 ran for 60 days with economic costs reckoned to be in excess of $1 billion per week nationwide. Backlogs, in terms of the number of days’ delay in unloading ships per day of strike action, can also be estimated with a reasonable degree of accuracy.
Financial losses will undoubtedly be higher this time around, if only because of inflation during the almost half-century since, however JP Morgan forecasts the loss to be $5 billion per day. As for duration, Lee Klaskow, Bloomberg Intelligence transportation and logistics analyst, anticipates a two-week strike at the 36 ports, with a “drag on economic growth” being the main impact.
One bright spot: container shipping rates, which skyrocketed during the COVID-19 pandemic, are likely to be only “marginally affected” by the strike, according to industry experts.
Switching cargoes from East to West
With the benefit of long lead times, many U.S. retail and manufacturing companies have been readying themselves for port closures, delays, and backlogs on the Eastern seaboard since early 2024. Back in January, more than a dozen logistics leaders were more concerned about the threat of an East Coast port strike than the threat of drone and missile strikes on ships in the Red Sea.
At a follow-up session in March, the senior logistics director at one U.S. apparel and footwear company said that if talks between the ILA and USMX failed to yield progress by the summer, it would begin diverting shipments to the West Coast.
Re-routing ocean-bound goods to ports unaffected by potential strike action – along with building up inventories, importing seasonal items such as holiday gifts early, and shifting premium and perishable products to airfreight – is what any proactive supply chain risk and resilience strategy would dictate.
It’s unsurprising then, that in recent months, the Top 5 West Coast ports have seen their share of container import traffic overtake that of the biggest East Coast and Gulf Coast ports, a reversal of the situation in 2022-23 when industrial unrest loomed over the Western seaboard. Total activity at the Port of Los Angeles, for example, was up 17.4% year on year through August, compared with a 13% decrease in 2023.
Automation? Not if it displaces jobs
However, the West Coast ports’ advantage could be short-lived. One reason for this is that East Coast and Gulf Coast ports are more efficient, according to the latest Container Port Performance Index. This shows that the top quartile of performers includes eight ports on the East and Gulf Coasts (including New York-New Jersey), while seven of the 11 North American ports in the bottom quartile are on the West Coast (including LA/Long Beach).
But East Coast and Gulf Coast ports shouldn’t be too smug. Just as with the ILWU’s stance, the ILA continues to strongly resist the introduction of new technology, such as driverless vehicles, automated cranes, and even semi-automatic gates at terminal entrances. Its just-expired contract stipulated a joint committee with equal employer and union representation to approve any such technology, and the ILA says it walked out of talks in June because it had evidence this was being flouted at some ports.
The lack of investment in productivity-enhancing technology appears to be an industry-wide problem. Zero100 analysis of supply chain job postings by U.S. companies between August 2023 and July 2024 shows that shipping and logistics firms lagged behind their peers in the high-tech, automotive, consumer packaged goods (CPG), and other sectors in looking for workers equipped to handle a range of automated and autonomous systems and self-driving vehicles.
The likelihood of a new long-term agreement between the ILA and the USMX changing this dynamic seems as far away as many of the ports from which U.S.-bound shipments originate. And while the digitization issue remains unresolved, the cycle of predictable disruptions at U.S. ports is set to continue.