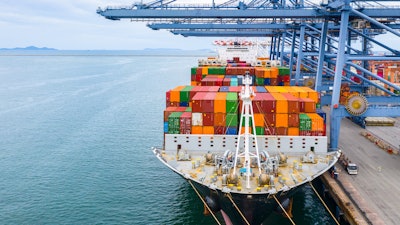
In the last two years, ports across the nation have faced significant backlogs and congestion stemming from labor shortages and rapid increases in import goods, leading to carriers and shippers being unable to get the influx of containers moved in and out of port yards on time. Technological inadequacy, lack of proper infrastructure and labor shortages have severely hampered logistics operations across the board, leading to the long lead times of idle containers, a slowdown in business, lacking inventory in stores and massive late fees, among other things.
In a sudden turn of events, global trade has almost slowed to a halt with inflation on the rise, which enabled the supply chain to catch up on the backlog. Once trade volumes pick up, which they will do since economic downturns don't last forever, logistics leaders must prepare their operations to ensure the supply chain can withstand crisis and uncertainty. With all of the factors that have wreaked havoc on the supply chain in the last couple of years, supply chain managers need to look at what they've learned since then, think about those lessons and make moves to ensure the same thing doesn't happen again.
The root of the problem
Traditionally, one of the most significant issues with cargo terminals is visibility. Ports take in hundreds of thousands of containers a month, and companies working in the supply chain may have little awareness of where their containers are in the port or when they will be unloaded and released. That can impact lead times and make it challenging to schedule onward manufacturing, transportation and distribution. Companies need to take a proactive approach to boost visibility and collaboration across port and container operations among cargo ship carriers, port operators, trucking carriers and shippers.
Of course, it's not just the port and its speed of loading and unloading containers that matters. It's also about the transportation and infrastructure supporting the terminals. Ports, shipping yards and warehouses all need easy access to tie into companies’ overall logistics and distribution network. Congestion and inefficient fleet operations can majorly impact onward shipping needs once volumes pick up again, so the infrastructure must be equipped to handle substantial loads.
The lack of efficient labor during the past two years also made it difficult to manage the massive flood of imports, causing slowed-down processes across the supply chain. The shortage of dock and rail workers made it extremely challenging to unload/load shipments and get them to their next destination.
Another issue with inefficient port operations was the proliferation of demurrage and detention fees. When containers sit idle for too long, the port and rail yard operators can charge companies extensive demurrage fees, which can cost upwards of millions of dollars per week. These fees were passed along to other transportation providers until products reached store shelves and ultimately hurt consumers' pockets. According to Container xChange, many shippers reported that demurrage charges had been levied against them despite cargo being buried under stacks of containers at logjammed ports. As a result, they could not retrieve their containers and were forced to pay huge fees. Demurrage fees can also be challenging to track due to the need for more visibility and collaboration between port managers, shippers and carriers.
Many operations throughout the supply chain are clearly complicated and have led to mismanagement and headaches. Simplifying processes and collaboration is key to ensuring operations run smoothly at ports and can manage high demand when it eventually picks up again.
Creating equilibrium in the supply chain
Over the years, the nature of the workforce has enabled operations to remain stagnant and rely heavily on manual processes, even for simple things like passing paper along from one person to the next for record keeping. These archaic processes have made visibility into operations extremely difficult for carriers and shippers to manage the movement of their containers.
Despite some innovations ports have implemented, many aspects of port ground operations still need to be improved and are still dependent on paper-based systems, causing overall slow productivity and incapacity to take on large cargo volumes. Once volumes increase again, shippers and carriers will have to pay for the ports' inefficient and outdated practices if supply chain leaders can't work together to create collaborative and robust operations. While current U.S. port infrastructure and processes may not be ready to combat another port crisis, there is a way for companies to start future-proofing their supply chains to prepare for any upcoming uncertainty.
A new solution is underway that can help companies restore order to their supply chain operations and combat the massive fees that come with idle containers. Companies are beginning to outsource costs and drayage operations to third-party providers with large amounts of private equipment and container management teams. This new initiative is called Demurrage-as-a-Service (DaaS), and it's an industry-first, full-service solution. The service will help companies pay demurrage fees that have racked up over the last couple of years and help them clear containers out of ports quickly to prevent new fees.
Not only will this service help pay back demurrage fees to the ports, but it also has a digital visibility component that can accurately forecast transportation costs and give logistics managers a clear view of free drivers, chassis and containers. This part of the service will also digitize operations for greater operational efficiencies and tracking ability, helping shippers and carriers find truck drivers to transport containers more quickly. For shippers and carriers, this means they can more accurately forecast and budget their overall transportation costs, allowing them to allocate resources to other parts of the business to maximize efficiency.
The supply chain crisis highlighted the industry's inefficiencies, and now it's up to supply chain leaders to band together to ensure this never happens again. By having increased visibility into available drivers and equipment as well as access to a third-party financial provider to take care of fees, shippers and carriers will be able to thoroughly proof their supply chain and take on uncertainty when it strikes again.