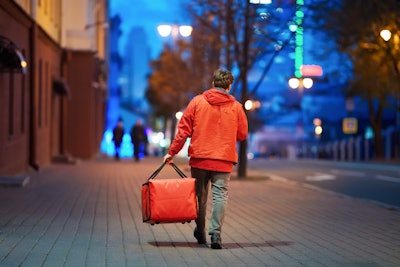
The gig worker economy was projected to reach $455.2 billion dollars last year. However, as profitable as gig worker-specific apps have become, their success is not so easily replicated across industries. Warehouses and distribution centers have seen ongoing talent shortages, as with many industries, and while we can point to the gig economy as a short-term solution, logistics service providers (LSPs) should look toward long-term improvements.
Rather than depend solely on a gig workforce to improve numbers during busy times, existing technologies can accommodate shortages by enhancing planning and forecasting staffing needs. Here are three key considerations logistics personnel should keep in mind before introducing gig workers into their organizational staffing strategies.
The challenges of implementing gig work in logistics
While gig work excels in delivery services, this model does not transfer easily into distribution centers, supply chain processes, or warehouse settings. Several safety and training challenges stand in the way of simply hiring gig workers off an app to take on these roles and responsibilities.
Dangerous machinery such as conveyer belts and forklifts are always present within warehouses and can pose serious harm to new employees if used without the proper training and experience. There are certain qualifications that must be met for new workers to operate machinery in a warehouse, including having the correct accreditation, licensing, and background knowledge. Hiring workers without these explicit skillsets and certifications to drive heavy machine equipment with little to no experience threaten their safety, and the safety of others.
Sufficient time for training on the equipment and tasks in warehouses is also an area of concern. New workers cannot just show up and begin working. In some instances, workers require at least a minimum of 24 hours of training before being allowed to go onto the floor as a picker or packer who doesn’t drive specialty equipment. Testing their capacity to work on machines, understanding safety modules, and becoming familiar with the environment are part of the onboarding process and cannot be rushed simply to meet order volume.
Enhancing forecasting and planning allows for better labor strategies
By focusing only on planning for typical peak seasons such as the holidays, Black Friday, and back-to-school shopping, logistics executives can leave warehouses and supply chains woefully unprepared for global disruptions or unexpected trends. As a result, occurrences like geographical events, extreme weather phenomena and patterns, or trade blockages, can result in long-term delays and significant revenue loss.
The current Red Sea crisis, for instance, is already said to potentially damage the global supply chain network more than the COVID-19 pandemic. The impacts of this crisis are already underway as delays and costs mount on products, and companies scramble to identify alternative shipping routes. Additionally, in preparing for expected peaks in Q4, executives neglect to plan for other busy seasons such as Q1, where suppliers and retailers are restocking goods, and clearing off last-minute order clearances from the holidays or conducting annual inventories.
By utilizing artificial intelligence (AI) and machine learning’s predicative analytics to determine customer behaviors, market demands, potential risks, and future scenarios, logistics executives can sharpen their planning strategy against these opportunities. Executives will be able to better assess staffing capacities in advance of potential disruptions and determine how much labor must be added or removed, which area of operations will require the most labor, and when an expanded workforce is needed.
Using the data cloud also eliminates integration complexities between logistics teams and supply chain operators, improving collaboration, planning, and decision-making as all parties utilize a single, common data infrastructure. All parties will be able to access robust, relevant information across silos to better inform their decision-making and strategic planning. For instance, where there are potential disruptions occurring in the supply chain, logistics teams can prepare their teams in advance, including hiring and training additional staff, if necessary, to minimize delays or work stoppages.
Investments in AI to augment staffing needs
More than two-thirds of organizations expect to increase their AI investment over the next three years. Instead of focusing on boosting its workforce with gig workers to meet peak season demands, the logistics sector should instead determine how new technologies can drive flexibility for the existing and incoming workforce, allowing decision makers to gain and retain employees from the right talent pool vs. focusing on temporary fixes across flex labor. This allows a more central focus in the total rewards for each associate and their contribution.
Generative AI can be a powerful tool to augment decision-making, guiding teams through inventory management, data analysis, and order processing, to produce results more quickly, efficiently, and accurately. By implementing generative AI into operations, the logistics sector will be able to focus its current workforce on tasks that require a higher degree of skill.
Emerging technologies in AI, like robotics, provide value by organizing, storing and transporting products and allowing for a more streamlined work production. As organizations adapt robotics into their workflow, logistics executives can prioritize making the workplace more “flexible” and accommodating to their current workforce’s needs. For instance, where there is a higher need for staff to work second shifts due to parenting commitments, robotics can be onboarded to assist with first shifts and deployed as necessary to work around employees scheduling needs. Such flexibility also makes organizations more appealing to prospective employees.
The gig economy may be a tempting solution for warehouses, distribution centers and logistics teams, without first integrating technology to augment workflows and enhance planning, executives are depriving their customers of a more robust, resilient, and sustainable supply chain process. By using AI, the data cloud, and robotics, logistics executives can more strategically plan for demands and disruptions, become a more flexible employer for new and existing employees, and deliver services efficiently.