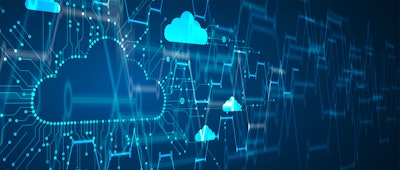
It almost goes without saying -- asset maintenance is essential to any truck fleet operation. Keeping vehicles on the road plays an increasingly critical role in enabling a connected supply chain, and a robust and proactive maintenance program that operates in the cloud ensures that fleets are maximizing resource utilization and improving customer service, while simultaneously reducing costs and keeping drivers and technicians happy.
Today, the concept of a “connected maintenance” program is gaining traction – utilizing cloud connectivity to bring additional visibility into maintenance activities, ultimately resulting in increased uptime and decreased costs.
Maximizing uptime
Maximizing uptime – or, on the other hand, decreasing out-of-service time – continues to be of utmost importance to carriers.
Because there is a repair cost and/or revenue loss associated with having a vehicle out of service, pressure is mounting on carriers to become more proactive when it comes to asset maintenance. Coupled with the ongoing driver and technician shortage, as well as pressures from shippers and receivers to guarantee just-in-time deliveries, the current trucking landscape makes uptime a mission-critical part of a carrier’s operations.
When dispatch assigns a vehicle, there is an expectation that it arrives from Point A to Point B as planned and on schedule, and the maintenance department has a responsibility to ensure that happens.
Historically, technicians have relied on pre-determined information from OEMs to determine when a part is due to be replaced. That is still relevant information to keep an eye on, however, today, solutions exist that can review a specific truck’s repair history and predict, based on how and where that truck was driven, when parts will actually fail and make recommendations on when it should be replaced.
Technologies have progressed significantly in the maintenance space, shifting to an increasingly preventive and predictive approach that helps mitigate concerns about unexpected breakdowns. Machine learning and artificial intelligence algorithms today can evaluate vehicle health and prescribe proactive steps to ensure that the truck can make it from origin to destination without any hiccups.
This is due in large part to the increased number of sensors on trucks, which are gathering huge amounts of data that can be used to create many new efficiencies. Pairing sensor data with an asset’s repair history gives a more comprehensive picture of vehicle health and allows fleets to start exploring more advanced maintenance solutions to help save time and money. Because of this, the understanding of what’s going on with a vehicle is better than it’s ever been and reduces the probability of a part failure taking place on the road. Often, this means fixing something before it breaks – a new shift in mindset for maintenance teams.
For instance, a predictive maintenance application could send a notification about when a part is likely to fail based on certain driving conditions such as climate zones, how fast a driver has been going and how many hard brakes they’ve had, elevation and more – just to name a few.
This customized approach to maintenance allows fleets to make repairs during scheduled preventive maintenance visits, or if a truck is on the road, at a nearby service center, rather than risking a roadside breakdown that will likely be expensive and time-consuming.
The more proactive and predictive a maintenance department can be, using advanced software to help them accomplish that goal, the happier everyone will be, including drivers. No one wants to experience a roadside breakdown.
Connecting the dots
What’s crucial in enabling the use of this data is cloud connectivity -- shops that run on paper are quickly becoming unable to keep up with the pace of digital transformation that the trucking industry is currently experiencing.
Connected maintenance is, of course, all about connection – integrations between disparate solutions and systems, and the exchange of data. The maintenance department needs to be able to connect and communicate with dispatch, operations, telematics data, routing, with drivers, visibility solutions and sometimes, even with shippers directly.
It all begins with exchanging and sharing data. Many technology providers, OEMs, etc., have developed their own portals for the data coming off of trucks and engines. This is great in theory, but in order for the information to be actionable in an efficient way, those sources must come together in one single screen.
In a connected supply chain, fleets need access to a connected system where all data is securely accessible to any stakeholder that needs it.
For example, telematics data from a truck’s engine may be pulled into an OEM’s portal, but if that data is not available in real time to another application like a predictive maintenance platform and then fed to dispatch, it may not actually be providing any real value for maximizing uptime.
In order for these solutions to truly provide the greatest value, integrations between providers must work together seamlessly and securely, in as close to real-time as possible. This is what will enable a truly connected supply chain that runs efficiently and cost-effectively.