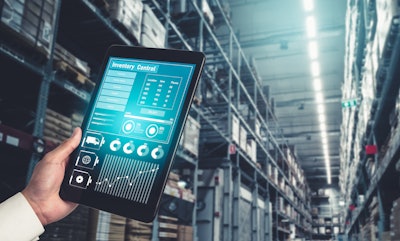
Cold chain warehouse audits have two important purposes. First, they find vulnerabilities and ways your operation could run better. Second, they demonstrate due diligence, which protects you from legal and reputational risks.
But audits have a habit of turning into routine exercises in compliance. Opportunities to drive business value get missed. Or, they focus too narrowly on surface-level problems and overlook the kind of systemic issues that might lead to worse disruptions in the future.
This matters more than ever as consumer expectations keep shifting. Yesterday's cold chain requirements look nothing like tomorrow's - just ask anyone who's had to adapt their operation for direct-to-consumer fresh meal delivery or premium flash-frozen produce.
Here are some key areas for conducting a thorough warehouse audit, whether looking at a single facility or standardizing cold chain procedures across your network.
Facility assessment
Geography brings specific operational constraints - how far you are from transport routes, whether fuel deliveries can reach you in severe weather, or if flood risks or heat waves could disrupt operations. Every facility faces distinct risks that generic audits often miss.
The building envelope develops microclimate patterns over time. Hot spots and cold spots form as airflow dynamics interact with door placement and storage layouts. Utility penetrations and expansion joints can undermine insulation integrity. If you walk the facility with a portable temperature logger, you'll find patterns the fixed sensors never see.
Loading zones deserve special attention. Dock seals fail gradually, drainage problems creep in, and water ingress has a way of appearing in unexpected places. Minor failures have a habit of eventually turning into serious temperature control issues.
Document everything, even when you can't do much about it. Sometimes understanding your facility's constraints is as valuable as addressing them.
Equipment evaluation
Every cold warehouse relies on four critical equipment systems: refrigeration, monitoring, power backup, and material handling. Each needs evaluation not just for current performance, but for signs of developing issues.
Most systems have inherent limitations. Sensors can miss brief temperature spikes, and their placement doesn't always capture the conditions the products actually experience. Regular cross-checking with mobile sensors helps validate the fixed monitoring system and identify blind spots.
Next, backup systems need real-world validation. Emergency power must demonstrate it can handle actual loads, not just spin up in monthly tests. Review maintenance records with an eye for patterns, recurring small issues often signal larger problems developing.
Finally, material handling equipment deserves equal scrutiny - slow handling speeds and equipment downtime often create temperature-control bottlenecks that compromise cold chain integrity.
Operational assessment
Peak periods reveal what an operation really looks like under stress. Watch how product staging and loading procedures hold up when everyone's rushing. The relationship between scheduling efficiency and product quality becomes painfully clear during these moments - delayed staging means longer temperature exposure, while hurried handling risks both product and worker safety.
Standard processes might look good on paper, but reality has a way of evolving. Observe actual practices during shift changes and busy periods. Pay attention to how teams handle the handoff between automated and manual processes - this interface is where most disruptions start. Even the best-planned pick paths might not match current needs, creating unnecessary product movement or ergonomic challenges.
Track cycle times across an operation, particularly around staging areas and dock doors. Waiting time isn't just an efficiency issue - it's a direct threat to product integrity. When you spot bottlenecks, look deeper. Sometimes what appears to be a process problem actually stems from layout constraints or equipment limitations.
Risk assessment and continuity planning
Each of your critical systems need realistic backup procedures. Consider the practical constraints - like whether the facility's emergency generator can actually maintain temperature control long enough to protect inventory.
Pay attention to how problems spread. A temperature-control issue at one point in the cold chain often creates pressure elsewhere in the system. Your team's ability to recognize and respond to these situations matters more than elaborate written procedures.
The most valuable insights often come from examining patterns across the network. When similar incidents occur at multiple facilities, they typically reveal system-wide vulnerabilities that need addressing. These patterns should guide the continuity planning, focusing efforts on scenarios your resources can actually handle.
Data analysis and continuous improvement
During an audit, look beyond standard data checks to find critical gaps in monitoring systems. Temperature logs might show acceptable averages while missing brief but damaging temperature spikes during loading. Inventory reports could mask picking inefficiencies that expose products to temperature abuse.
Start with the basics - verify the fundamentals, like sensor calibration and placement.
Then dig deeper and consider unexpected connections. Sometimes maintenance logs reveal more about temperature control challenges than sensors do. Your best insights often come from unexpected correlations, like why temperature stability varies between shifts or dock doors.
Robust data collection doesn't guarantee effective analysis. So focus the audit on how information transforms into action.
Taking action on audit findings
Audit findings need ruthless prioritization. High-risk issues can't wait, but don't ignore those efficiency gaps that slowly bleed an operation.
Focus on real impacts you can measure: spoiled products, wasted energy, double-handling, customer rejections. Test solutions in one area before rolling them out. And get contractor agreements in writing - every responsibility, every handoff point, every response time.
Break big problems into bite-sized pieces. Product stability testing and temperature validation take time - you can't rush physics.
Document temperature tolerances for every product type - they're as much a physical constraint as your storage capacity. Track everything against your baseline, but be ready to pivot when the data points somewhere unexpected.
Moving forward
You won't fix everything you find. That's fine. Thorough documentation of known issues, even ones you can't do anything about, helps leadership target resources where they matter most. Sometimes the best outcome is simply a better understanding of where the cold chain needs investment.
The best cold chains run on trust and clarity. When crews understand why temperature limits matter, when contractors know their exact responsibilities, when leadership sees the real operational picture, that's when lasting improvements take hold. Your audit findings build this understanding, step by step.