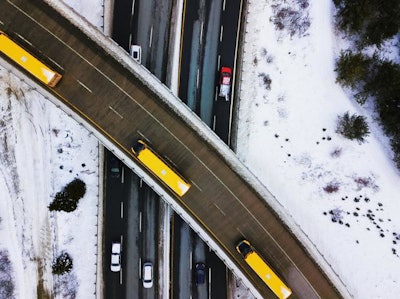
There is no doubting that extreme weather is here to stay. In Q1 of 2024, the United States experienced record low and high temperatures with six major winter storms, periods of heavy rainfall, and warmer-than-expected temperatures as far north as Canada and Alaska. The frequency and intensity of extreme weather events is on the rise and the risks and impacts to cold chain fleet operations are particularly high when delays and extreme temperatures combine to threaten safe handling of temperature-sensitive goods such as produce, meat, dairy, pharmaceuticals, and frozen goods. When severe weather strikes, ensuring cold chain fleets are well-equipped with the right tools, processes, and preparation will ensure critical load handling and safe delivery.
Prepare your fleet
The key to maintaining proper cold chain product handling during severe weather is fleet preparation. Routine coordination and processes like route planning and digital vehicle inspection reports (DVIR) become critical when severe weather strikes. Identifying and avoiding routes and regions known to become particularly dangerous during extreme weather reduces the risk of accidents and delays while considering known but not deadline maintenance issues when selecting tractors and trailers stacks the odds in drivers and fleets favor. Turn-by-turn route planning and driver navigation applications combined with integrated DVIR and maintenance management systems give dispatchers and fleet managers the insights needed to make critical decisions before severe weather has an impact.
Independent temperature sensing and logging is another example of cold chain fleet preparation where a relatively small upfront investment pays big dividends during severe weather conditions. Adding 2-3 independent temperature sensors configured to sample every 5 minutes and store 3,000 readings provides 10 days of uninterrupted backup temperature history data when refrigeration unit maintenance or refuel interrupts primary data collection.
Training is critical
Driver and cold chain fleet team training is critical to ensuring compliance and minimizing delivery delays when severe weather impacts normal operations. Severe weather commodity handling practices and standard operating procedures provide the insights, backup data, and contact details needed to make time-sensitive decisions to reroute shipments to other distribution centers or stores, coordinating repairs with refrigeration unit and trailer repair shops, and understand the warming and cooling effects extreme high and low ambient temperatures have on frozen and fresh produce and other temperature and humidity sensitive products and medications.
Driver training prior to severe weather is critical to both driver and motorist safety and cold chain delivery compliance. Simulator, online, and remote training sessions are proven to be incredibly helpful for drivers to get accustomed to emergency protocols and extreme weather road conditions. Training drivers to take a defensive driving approach and operate at safe speeds and distances in severe weather conditions significantly reduces accident risk and damage to vehicles and cargo.
Communication is key
Timely, clear, and coordinated communication is the key to ensuring compliant and safe product delivery and preservation during normal and severe weather conditions.
Cellular data network coverage and in-cab data terminals and mobile applications combine to provide extremely good real-time fleet manager and driver communication. Automated tractor and trailer fleet tracking and monitoring allow drivers to focus on safe driving while automated service and compliance mobile applications like scale bypass, parking reservation, roadside assistance, and fuel pricing tools simplify support operations.
Cold chain fleet management systems leverage remote communication to monitor product temperatures and trigger alerts when temperatures or systems are out of control limits and need attention to avoid compliance issues. One example is automated alarm email escalation and issue management reporting where dispatchers and fleet managers are progressively alerted to persistent alarms that have not been acknowledged or resolved.
Typical cold chain shipments can maintain compliance for four hours before high or low temperatures start to impact safe handling and commodity preservation. Drivers receive local and remote alarm notifications in the form of refrigeration unit displays on the trailer, in-cab terminal notifications, mobile application notifications, and telephone calls and texts. Dispatchers and drivers work together to implement remediation plans ranging from correcting refrigeration unit settings to alternate site delivery, all designed to ensure compliant commodity handling to ensure safety and avoid costly commodity loss.
Leverage the power of data and technology
When managing the special challenges and complexities of cold chain logistics combined with severe weather, the power lies in leveraging data and technology solutions. When severe weather threatens, artificial Intelligence of Things (AIoT) solutions can streamline refrigeration unit monitoring/control, vehicle tracking, and effective communication, all critical for successfully managing cold chain logistics. But simply having access to the information is not enough; drivers and fleet managers must identify risks and vulnerabilities in advance and make plans to improve real-time visibility, decision making, and issue tracking to resolution.
From origin to destination, AIoT solutions monitor sensitive cargo, provide precise and continuous remote temperature and humidity monitoring, and provide real-time data and alarm visibility needed to quickly identify and resolve potential threats before they impact compliance, safety, and profitability.