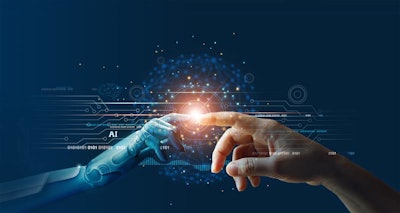
Post-pandemic, the world has become more globalized, complex, fragile and unpredictable than ever. And these developments have significantly impacted the food supply chain worldwide, creating a perfect storm of labor shortages, difficulty accessing raw materials, rising food safety regulations and inflated food prices.
Compounding these issues is the increasing demand for fresh produce. The cold food chain logistics sector responsible for safe and efficient delivery is expected to grow from $233.8 billion in 2020 to $366.8 billion in 2026. Yet, this sector is rife with even more complications than the typical food supply chain. One example of this is the transition to intermodal shipping, which makes maintaining the temperature of products end to end particularly difficult.
So, what is the answer to these complexities? Funnily enough, more complex tech solutions. Let’s break down three of the most sophisticated technologies transforming the future of cold food chain logistics for the better.
Digital twinning
A digital twin is a virtual 3D replica of a particular part of the supply chain. The clone could be of an entire warehouse, inventory, vehicle or product. Previously, logistics teams would test specific scenarios and changes to these elements in real life through trial and error, but now they are opting to carry out virtual simulations. As a result, the digital twin market size was more than $5 billion in 2020 and it is predicted to grow at a CAGR of more than 30% until 2026.
Customers now have considerably greater expectations for the appearance, texture and taste of fresh food, all of which can be impacted by multiple variables throughout the product item’s journey to the customer.
With digital twin technology, companies can simulate potential changes that may occur to the product, let’s say an apple, due to temperature changes, humidity and oxygen and CO2 levels. This was particularly key during the pandemic, where recurring shortages of CO2, required to refrigerate and preserve many cold food items, wrought havoc on the industry.
Today, digital twinning can help businesses gain valuable insights and find smart solutions when faced with unwanted changes that threaten the quality of the products.
This technology is advancing, with companies starting to create digital twins of entire rail and road networks, oceans and end-customers’ domestic and workspaces. For even more optimized results, it’s now being coupled with augmented reality (AR) and virtual reality (VR), creating machine-human interactions known as “collaborative intelligence.”
AR glasses worn by workers can innovatively test the packaging performance, optimize routes, and enhance delivery processes. Instead of doing it manually, AR helps workers to overlay the task requirements digitally and carry them out with artificial intelligence (AI)-powered intelligence in real-time.
VR headsets help geographically dispersed stakeholders immerse themselves in a supply chain environment, such as a warehouse, and work together to find customized solutions tailored to a location. They can then use their learnings to improve the performance of the cold food supply chain in the physical world. This merging of the virtual and real-world—referred to as the Metaverse—is evolving in this sector.
Natural language processing
The interconnectivity of global logistics today means that an event occurring on the other side of the world could likely have a whole host of direct and indirect consequences on a company’s supply chain. Disruption is now the norm, but technology such as natural language processing (NLP) has stepped in to warn against potential problems.
NLP engages in “web scraping” where the technology searches for key terms by scouring through news articles, websites, and videos. Then it finds information and news that may prove critical to the efficient running of logistics processes. Within the supply chain itself, there is an enormous amount of data. Web scraping is instrumental in analyzing multiple sources and applications such as shipping, order and fulfillment documents to gain deep data insights.
NLP also involves “social listening” within social networks, forums, reviews and customer service channels by conducting “sentiment analysis.” The evaluation ascertains whether the public speaks about supply chain themes positively, negatively or neutrally. This feedback is valuable in better understanding customer pain points and what areas of the chain are in need of review.
Due to the globalization of business operations, language barriers are a recurrent obstacle to process efficiency. NLP can translate audio and written content gathered from other languages regarding suppliers, competitors, and regulatory policies. Natural language generation (NLG) is used alongside this technology by using the collected data and translating it into human-sounding language. This is then used to automatically create product descriptions and specifications, instructions, schedules and alerts across borders.
Hyperautomation
Hyperautomation is indispensable in the future-proofing of logistics businesses. Logistics teams are implementing it across the whole chain, from vendor selection and procurement, to supply and demand planning, training, security and fulfillment. As well as digital twinning, AR and NLP, hyperautomation includes other highly sophisticated technologies such as robotic process automation (RPA), advanced analytics, low-code/no-code software, virtual assistants and optical character recognition.
For example, pilotless drones using GPS trackers can be deployed to move their way through warehouse aisles, automate inventory count and detect damages and errors of goods. Driverless vehicles are also set to become an integral part of the industry as the shortages of truck drivers across the world are likely to continue rising.
An area where hyperautomation is increasingly being used is the last mile—a particularly problematic part of the cold food supply chain. Semi-autonomous robotic fleets fitted with cameras, sensors and GPS tracking can successfully and safely deliver food across local communities, college campuses, hospitals, and businesses. This is game-changing as human negligence and error at the point of delivery are one of the biggest issues in the cold food logistics sector.
Finally, hyperautomation will be combined with other tech solutions in the future such as isochoric freezing, smart labeling with time-temperature indicators, zero-emission technologies and the use of phase change materials to store cold thermal energy.
Despite the many complexities and disruptions the global cold food supply chain is experiencing, companies will continue to rise to these challenges by deploying increasingly advanced tech solutions into their operations. These technologies are able to foresee obstacles, overcome inefficiencies and optimize even the most difficult of processes, from the warehouse right up until last-mile delivery. They will completely revolutionize cold food chain logistics in the years to come.