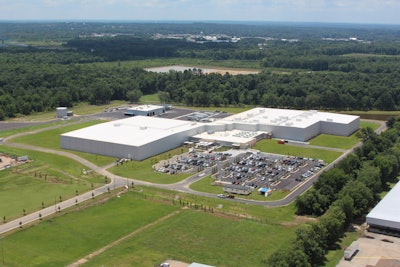
In many ways, cold storage facilities are the antithesis of flexibility with their high-priced construction, operating costs and sheer physical size and space. Yet, the demands of today’s cold chain means facility design, location and even refrigeration systems are under greater pressure to adapt to constant changes in the marketplace while keeping operating costs in check.
Simply put, a cold storage facility essentially is “a giant refrigerator for everybody’s products,” says Tim Nguyen, regional vice president at ESI Group USA. It’s no surprise then that automatic storage and retrieval systems (ASRS) continue to generate buzz in the sector because of their ability to boost storage density and eliminate the need for forklift aisles, not to mention reduce labor and energy costs, he adds.
The downside is the initial cost. ASRS requires a substantial investment. “Secondly, there are costs associated with maintenance,” says Nguyen. “All the robots, gears and hydraulics moving in a very cold environment require a lot of maintenance.” Additionally, these types of facilities are not very versatile, because they typically are designed to accommodate a specific pallet size or carton size in order to achieve uniformity and consistency, which then becomes an issue (if there is a desire to make a change), he says.
“In the cold storage sector, sometimes you’re storing berries, sometimes ice cream or apples, and the configuration changes,” which makes it difficult if you’re locked into a specific system.
Wholesalers who manufacturer their own product(s) tend to make better fits for ASRS. But, operators still can achieve flexibility if they use the ASRS for bulk storage, then use workers to break down pallets into cases or smaller components, which can then be placed in totes or trays and put onto conveyors. This type of operation is becoming more common as online grocery shopping and home delivery continues to grow.
One of the biggest automated cold storage facilities in the United States is under construction in Tacoma, Washington The 25-million-cubic-foot, 130-foot-high Tacoma Automated Coldstore will open by year’s end, with Trident Seafoods as the primary tenant of the multi-customer facility.
Dutch firm NewCold is the owner of the facility, which will rely heavily on automation to control costs related to labor, land and energy, says Jonas Swarttouw, the company’s business development manager for U.S. operations.
Automation also is key to responding to customers’ expectations for faster and more efficient shipping options. It’s difficult to find employees to work at night, not to mention working in a cold storage facility with below freezing temperatures, adds Swarttouw.
The facility will employ some forklift drivers, although robots will primarily be used to move product inside the facility and fulfill orders. Computer tracking of products inside the facility also will provide faster response time in the event of a recall.
According to Swarttouw, “The advantage (of automation) is that you are performing in a very stable and controlled way, and with limited human-product interactions and limited chances the humans will damage the product or pick the wrong pallet.”
The ASRS system will store products on a rack system in low oxygen and complete darkness. Pallets will be transported to the loading area of the facility by a series of conveyors and robots.
As for cold storage trends related to location, the buildup of cold storage facilities around key gateway ports remains strong. “You have to go where your customers are,” acknowledges Nguyen, “but at the same time, you have to be flexible in case your business changes.”
For instance, Nguyen says the industry is trending toward more 80,000- to 100,000-square-foot cold storage warehouses in multiple locations, and fewer “huge, 5- and 600,000-square-foot cold storage warehouses.”
He compares this to the air transport industry’s wide-body passenger jets, which need a lot of people to fill seats and big “hub” airports. Increasingly, people—and products—want to get closer to their end destination, though. A distribution center that is closer to the consumer market is more efficient in terms of logistics and other supply chain considerations.
“The bottom line is you’ve got to react to your customer and you want to be flexible; you want to be fast. That’s the model I see the industry going toward,” says Nguyen.
Evaluating refrigeration systems
The options surrounding which type of refrigeration system to implement comes down to energy efficiency and safety—and operators need both. A cold storage facility’s biggest cost is energy, so energy efficient motors and energy management systems (or anything else that can save a couple kilowatts per hour) add up over time, and therefore make a significant dent.
Overall, the industry is more willing to invest in energy efficient refrigeration systems today, observes Nguyen.
Meanwhile, ammonia remains the cheapest refrigerant (it is up to 10 percent more efficient than other refrigerants) and uses less electricity than other systems. However, “the downside is there are some safety issues with ammonia,” he says.
Another issue is water. Ammonia systems use a lot of water for their evaporative condensers. In states such as California where water prices are at a premium, these types of systems present real problems.
“Certain locales just don’t have enough water” to support these types of systems, says Nguyen.
For these reasons, cascade systems are a good alternative for some facilities. It’s basically comprised of two refrigerants, whereby one refrigerant cools the other refrigerant, which then cools the facility. A cascade system is very energy efficient, and it allows the separation of two refrigerants within the system.
For example, “Now I can put ammonia in one location, which is usually the equipment room, where it refrigerates CO2,” says Nguyen. This type of cascade system is favored for its safety aspect, because ammonia is isolated from workers in the facility. It also reduces the total amount of ammonia charge in the plant, he adds, which helps address certain regulatory issues.
Cascade systems essentially are the standard now on the big distribution facilities that ESI Group is building. Although they are expensive, the ROI manifests in 3-8 years. “Once you get past that, it then becomes a no-brainer,” says Nguyen.
Customers that have large facilities, and those with multiple facilities, make the best fit “because they see the value in energy efficiency over the long term,” he adds.