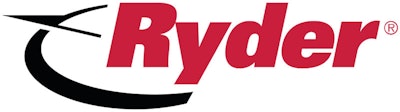
According to the U.S. Energy Information Administration, the national average price of diesel is $2.544 per gallon as of May 15. Given that the average semi has a fuel capacity of 150 to 300 gallons, it would cost $381 to over $762 per fill-up. Clearly fuel is a tremendous expense for the food and beverage logistics operation, and controlling fuel costs is a key component of fleet management as well as fleet sustainability.
The following article lists four ways food and beverage fleets can leverage technology, change processes and train drivers to be more sustainable.
Know Your Fuel
“Fuel costs come as a function of the fuel consumed, the type of fuel and the price point of the fuel. For this reason, it’s relevant to think about the configuration of the vehicle that’s being utilized and what fuel type really makes sense for that duty cycle or application,” says Scott Perry, vice president of supply management and global fuel products for the Fleet Management Solutions business segment of Ryder System Inc.
There is no silver bullet when it comes to fuel, rather Perry says “a series of silver buckshot that have to be evaluated.” For instance, if it’s a long-haul food and beverage fleet and a heavy Class A type configuration, the fuel options will be more limited than if it’s a fleet using straight trucks to make local deliveries.
Fleets today, he says, have two main options when it comes to fuel: Diesel or natural gas. Determining which fuel makes the most sense comes down to the objectives of the organization. “However, natural gas can be a bit more restrictive in how these vehicles are utilized, the range they have and the technology yield,” Perry says.
Schneider, which consumes more than 10 million gallons of blended biodiesel a year to be more environmentally friendly, reported in a publication titled “Going Green Together” that the “overall economics of natural gas operations are not enticing carriers to expand beyond testing” for this fuel. In fact, this provider of transportation and logistics services found that natural gas delivers 15 percent less miles per gallon than diesel. Its use also increases the frequency and the time it takes to fuel the vehicle, and cuts the truck’s engine life in half.
“We see diesel vehicles continuing to become more and more fuel efficient, whereas natural gas vehicles are bumping up against some of the physical constraints of the fuel and fuel combustion cycles. We don’t see much fuel efficiency being obtained [with natural gas,] but we do see results from an emissions standpoint,” Perry adds.
According to Perry, natural gas conversions make sense when operating fixed route structures, where the fleet goes out and makes deliveries and returns to a home base each day. In these cases, the range and infrastructure limitations of natural gas are no longer an issue. Perry explains that “dispatching from the same location and returning to the same location each day makes the use of some of these advanced fuels a little easier to control,” he says. “If the customer base changes and the delivery routes change each week, it makes the range limitations of natural gas more complex and too big of a burden because of the gaps that exist in fueling infrastructure.”
Consider Fleet Design
Wind resistance is one of the top forces working against a truck’s fuel economy. According to Cummins MPG Guide titled “Secrets of Better Fuel Economy,” a 2 percent reduction in aerodynamic drag results in approximately a 1 percent improvement in fuel economy.
Claude Ricciardi, director of purchasing at New York-based Transervice Logistics, states when it comes to fuel economy, a lot of emphasis has been placed on trailer aerodynamics, from trailer skirts to undertrays to spoilers. Low-rolling resistance tires and aero wheel covers as well as smooth-sided trailers are also spec’d to improve aerodynamics.
“Aerodynamics is a really basic building block of fuel economy whenever it applies to both the tractor and the trailer,” adds Perry. “The trailer offers a significant amount of drag whenever you think about a combination vehicle. The use of side skirts and low-rolling resistance tires on trailers are very much key drivers in improving fuel economy. They can bring anywhere from 4 to 8 percent improvements in fuel economy.”
He adds that fuel impacts are also considered when specifying engines and transmissions. “There seems to be a trend toward automated transmissions, which can improve fuel economy,” he says.
Finally, fuel calibrations and settings used to control the speed of trucks as they move down the road offer fleet operators a very simple mechanism to control fuel costs. Consider that every mile per hour above 55 mph results in 1/10th of a mile per gallon degradation in fuel economy. “If you’re operating at 65 mph as opposed to 55 mph, you have already lost 1 mile per gallon of fuel efficiency,” Perry says.
However, Perry reminds that it is key to gear the speed limiting of the vehicle toward the vehicle’s peak operating condition, meaning if the vehicle is set to operate at 65 mph and is geared to operate at that speed, you may actually use more fuel if you limit its operation to 60 mph. “You have to understand the duty cycle of that vehicle and how it has been optimally configured to optimize the vehicle’s fuel economy,” Perry says. “Going outside of that targeted speed and axle ratio can degrade fuel economy very quickly.”
Telematics and Other Technology
Like most food distributors, Ginsberg’s Foods has long used traditional fixed route dispatch and routing practices, delivering loads to the same customers on the same day each week. Complicating the routing process at Ginsberg’s is the fact that customers do not always have standing orders. Many times, customers need additional delivery days. Moreover, many delivery locations require the distributor to adhere to four-hour time windows.
In 2015, the company determined that a dynamic routing system that could account for orders and delivery windows, and was fully integrated with onboard communications technology, was needed to manage and monitor deliveries by account on a real-time basis.
After reviewing the capabilities of the legacy dispatch and onboard communications systems already in, Ginsberg’s determined that TMW Appian Final Mile and PeopleNet solutions would be the best choices moving forward.
Ginsberg’s teamed with TMW to establish a plan to upgrade its technology in three phases. Phase one would see the implementation of TMW Appian Final Mile routing and dispatch software. Phase two would involve upgrading the fleet’s onboard systems with PeopleNet technology. In phase three, the company would integrate handheld computers for point of delivery scanning.
With TMW’s support, all activities were completed, and on March 1, Ginsberg’s was fully operational with both solutions.
Based on immediate results from just the first month of operation with the TMW Appian Final Mile solution, Ginsberg’s Foods is realizing impressive savings, according to Larry Bigando, the company’s transportation manager. In the first month, delivery stops were reduced by 5 percent, stops per route were reduced 6 percent, routes per day were down 4 percent and miles driven went down 6.7 percent.
“We have seen a tremendous savings in fuel,” says Bigando about the change. “We have also seen a savings in driver headcount. We’ve been able to operate with less drivers than we did a year ago.” In fact, Ginsberg’s Foods has already reduced its driver staffing size by two trucks in spite of the fact that it is opening a new satellite location. In addition, the company is on track to save over $571,000 in its first year by reducing its driver staffing and fleet size.
Monitor Driver Behavior
“Telematics is a key tool that will give visibility to performance of the vehicle, fuel economy, driving habits and idle time, which are all key components to understanding the vehicle’s overall fuel efficiency,” says Perry.
With onboard diagnostics and telematics, companies are now able to track road speed, backing applications, etc., which allows them to “determine the good drivers from the not-so-good drivers,” adds Perry.
This information can help drive greater fuel efficiency through targeted driver training, adds Ricciardi.
Schneider uses simulation-based driver training programs that demonstrate to drivers that they are the primary managers of truck energy efficiencies. The company has found these simulations result in an average fuel savings of 335,000 gallons of fuel per year.
In addition, Schneider drivers receive bonuses for energy conservation and safety. In 2015, the company paid $38.2 million in driver incentives for fuel management, safety and other efforts.
“Safety is a key component of sustainability,” adds Perry. “There are many high legal damage awards being granted from lawsuits around improper and unsafe operation of vehicles.”
If safety is also considered part of a company’s sustainability initiative, then fleet operators need to focus on how they can limit unsafe behaviors among drivers to improve the number of safe miles they drive as well as reduce the frequency and severity of collisions should they occur. Forward-looking collision mitigation technologies, autonomous braking systems, forward-looking radar, lane departure control systems, in-cab video monitoring systems and connectivity from a telematics standpoint, can also drive the right driving behavior.
“With these systems in place, Ryder has seen a higher degree of accountability around the drivers operating the vehicles. They make sure they are in tune with their surroundings and operate very safely,” Perry says. “It’s the safety side of the equation. The fuel side of the equation is much the same. The way drivers operate the vehicle in terms of how they do everything from shifting gears to how long they idle, can impact fuel efficiency.”
Companies can use the data they gather from the technology on the truck to help drivers improve their performance. “They can say, ‘Here is how you’re performing individually, here’s how the rest of the fleet is performing overall, and here are how our best operators in the fleet are performing with regard to fuel economy, safety and efficiency. This gives them a benchmark and puts a little peer-to-peer pressure around performance.”