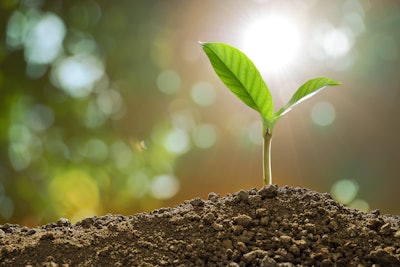
Supply chains are at the cusp of a transformative era in the food manufacturing industry, marked by the emergence of manufacturing energy transformation. Manufacturing energy transformation involves diligently monitoring energy consumption, carbon emissions, and waste throughout the entire value chain to identify areas for enhancing sustainability compliance. The drive behind this initiative is partly due to proposed legislation mandating new standard emissions reporting. Faced with the escalating impact of climate change, food manufacturers across the globe are intensifying their focus on sustainability initiatives.
Increased government pressure
Growing government pressure is evident across every industry as organizations strive for carbon neutrality objectives. The Securities and Exchange Commission (SEC) recently proposed measures requiring companies to disclose their greenhouse gas (GHG) emissions to investors, aiming to augment environmental, social, governance (ESG) transparency and diminish carbon footprints. Further, public companies will be asked to report their Scope 3 emissions to stakeholders. Scope 3 emissions, which are upstream and downstream emissions of a product across the supply chain, are especially difficult for manufacturing leaders to track since this data is not easily accessible.
Pressure on food manufacturers is further amplified by the Paris Agreement’s call for a net-zero economy by 2050. According to the United Nations, the United States is not on track to meet this goal and will need to reduce emissions by 45% in the next seven years. In response, the U.S. Department of Energy released its Industrial Decarbonization Roadmap to outline the route for stakeholders to achieve a net zero economy by 2050. The roadmap calls out four key “pillars” of industrial decarbonization: energy efficiency; industrial electrification; low-carbon fuels, feedstocks, and energy sources; and carbon capture, utilization, and storage.
In the upcoming year, smart manufacturing technologies are poised to play a pivotal role in accelerating sustainability efforts within the food manufacturing sector. Supply chain traceability solutions capable of capturing, contextualizing, and analyzing data across the value chain pertaining to energy consumption, carbon emissions, and waste, will offer manufacturing leaders invaluable insights for identifying opportunities to mitigate their environmental impact.
The solution: Supply chain traceability
The solution lies in the adoption of supply chain traceability technology, allowing business leaders to monitor and enhance their sustainability practices. The collection and contextualization of data are imperative for meeting net-zero emission targets by 2050. As raw materials traverse the manufacturing process through numerous suppliers, employees, and processing stages, tracing each step facilitates a comprehensive understanding of gaps in sustainability goals, thereby improving efficiency, yield, and compliance.
Real-time traceability technology empowers manufacturers with a detailed perspective of materials and goods at every production stage within the supply chain. This enables swift identification of issues, including their exact location and nature, facilitating prompt corrective action. Moreover, proactive identification of potential issues before they escalate helps prevent recalls and other environmental risks.
By embracing Industry 4.0 solutions such as traceability technology, business leaders can streamline processes, reduce carbon emissions, and ultimately realize their sustainability objectives. This not only translates to cost savings but also enhances brand image, attracts new talent, and, most significantly, contributes to a more sustainable and environmentally friendly future.
Real-world examples
Supply chain traceability technology is not new – it is used by some of the world’s largest food and beverage manufacturers. The solution identifies material composition changes along the supply chain path more quickly, thus reducing the number of products that must be recalled or turned into waste in the future. By incorporating this real-time material-centric view, businesses have eliminated countless potential recalls, maximized throughput, enhanced sustainability, and contributed to reducing the approximately 30% of the world’s food that is wasted in the food supply chain.
There are two key areas of waste reduction that supply chain traceability supports: total trucking miles saved (and carbon emissions reduced) as a result of having more efficient operations, and the elimination of physical waste that would have ended up either in a landfill or wastewater treatment facility. Users save hundreds of thousands of miles in rail care miles saved, as well as hundreds of thousands of pounds of reduced physical waste. Specifically, after introducing material traceability into its operations, General Mills doubled its production yield, achieved 99.99% elimination of recalls, saved more than $40 million in costs, enhanced customer engagement and loyalty, and perhaps most critically to the world, it has begun to make good on its role as a U.S. Food Loss and Waste Champion.
A net zero future
Although the goal of achieving a net zero emissions economy is aspirational, it is achievable. Governments and manufacturers alike must work together to ensure federal and state regulations are fair while identifying areas for improvement. Smart manufacturing solutions that automatically capture valuable data across the supply chain will be revolutionary in supporting business leaders with their sustainability initiatives. Failure to adopt these solutions and adapt to the ever-changing manufacturing landscape could result in federal action.