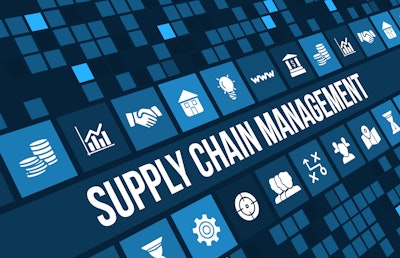
Making informed, real-time decisions is crucial for companies in the supply chain, especially those that deal with perishable goods. It can make a significant difference in optimizing routes, reducing delays, improving inventory management and, ultimately, ensuring products on the shelf are fresh and will last. Improvements in operational efficiency and resilience would constitute a genuine competitive advantage.
But that kind of decision-making depends on making real-time use of data, which leaves many companies in a bind. They have the means to generate that data, including critical parameters ranging from traceability to location to temperature and shock impact. But distilling the raw data into actionable insights in real time is, for many companies, beyond their grasp.
Companies need the digital equivalent of that trusted veteran dock worker who’s seen it all and has deep, nuanced institutional knowledge based on experience. There’s one on every dock. How do you bring that level of ingrained knowledge to every aspect of your operation?
Cold chain environments are drowning in data
Supply chain companies don’t have a data generation problem; they have a data visibility problem.
They have transportation management systems (TMS), warehouse management systems (WMS) and other enterprise applications for monitoring supply chain activity as well as sensors, data loggers and other tools that collect cold chain data on perishable goods and other temperature-sensitive products such as pharmaceuticals.
Despite being data-rich environments, however, many companies are unable to draw actionable insights from their data, falling short of operationalizing the investments they’ve made in supply chain/cold chain visibility. and not improving on the 15-20% product loss rates that are standard in the food and beverage industry.
An organization, for example, may have an array of active data loggers using GPS or cellular signals to monitor goods in transit, identifying their location at any point in time. They can monitor temperature fluctuations affecting perishable and temperature-sensitive products, as well as humidity levels for products sensitive to moisture. They can track other factors—such as light exposure, shock and vibration—that affect certain products.
Companies also can use sensor data from devices that don’t transmit in real time but meticulously record data on temperature, humidity, shock and other environmental factors. That data can be later analyzed and used to create baselines for proper shipping conditions and in identifying the areas in need of improvement. It can, for instance, identify areas where temperature fluctuations, shipping delays or product damage most often occur, allowing companies to optimize shipping routes.
Many organizations run into a wall, however, when it comes to using all that cold chain data, plus data from enterprise supply chain systems to divine actionable insights. Dots on a map and streaming temperature data are nice, but they don’t tell you what action needs to be taken. And the inability to act on that data puts products at risk, reduces operational efficiencies and strains customer relationships.
Without an effective means of efficiently combining and analyzing supply chain and cold chain data, organizations restrict visibility and complicate ROI. Rather than putting their data to use, they simply suffer from information overload.
Meeting the challenges of operationalizing cold chain data
Organizations looking to make use of their data can follow one of two basic paths: build their own visibility system or adopt a solution specifically designed to provide supply chain insights.
Building a system in-house can seem like an attractive option, since an organization could conceivably tailor it to its own needs and maintain control over the system. But it also involves lengthy development cycles while carrying hidden costs and maintenance obligations. The challenges of forging your own path to operationalizing supply chain visibility include:
· Significant costs. A company must invest a substantial amount of capital to build a complex data analytics solution. And it will need specialized resources—in the form of people with the right skills—to implement the system.
· Steep technical debt. Devoting money and resources to building a solution diverts the organization’s focus away from other core functions and can delay the time to value (TTV) for receiving actionable insights.
· Maintenance woes. When you own the system, you have to keep it updated and stay abreast of new developments in technology, data streams and business requirements. This can overburden in-house teams.
The other option is to acquire a purpose-built solution, which offers several advantages. For one thing, you can implement a purchased solution a lot more quickly than you can build one, increasing TTV and ROI. For another, third-party providers already specialize in supply chain analytics, bringing with them years of deep domain knowledge, best practices and advanced analytics.
They are built to scale easily to meet an organization’s needs and adapt to changes as they come. Providers also are responsible for keeping their systems updated. And although organizations may pay licensing costs up front, purchased systems cost less that building and maintaining a system in-house, avoiding expenses like hardware, developer salaries, ongoing updates and the overhead of managing a complex analytics environment.
Making your cold chain data work for you
In choosing a solution for operationalizing your real-time and sensor data, consider several critical features.
Automation is essential. Trying to manually extract patterns, trends and insights from the vast amount of data in your organization is too arduous and time-consuming to support optimization, and it’s also not a scalable practice. Automating the extraction of logger data, for instance, allows you to create a standardized method of collecting temperature records in a central location, providing a consistent data set for analysis. Standardized documents also make it easier to meet compliance requirements.
It’s also helpful to understand the applicable uses for real-time data and sensor data. Real-time monitoring of shipments and factors such as temperature and impact is extremely valuable, but budget considerations can make enterprise-wide real-time tracking impractical for all situations.
Sensor data collected for later analysis, however, can be a very useful, cost-effective way of gaining supply chain and cold chain insights. Sensor data, for example, can affordably track temperature, humidity, shock and other environmental factors throughout a shipment to pinpoint areas in need of improvement and establish baselines for performance. They’re also useful for short-term trials or investigations involving specific shipping routes or products.
Identifying effective uses for both real-time and sensor data can hold down the costs of monitoring while still helping to streamline supply chain operations.
Conclusion
Improving supply chain performance involves getting full control over your supply chain and cold chain data with a solution that enables both real-time and forward-looking data analysis. Companies need a system that, like that one wizened worker on the loading dock, just knows everything.
Companies need to bring that level of institutional and operational knowledge into a centralized, automated system capable of putting vast amounts of data to effective use. When data-driven insights fuel decision making, it reduces supply chain risk, increases efficiency and creates happier customers.