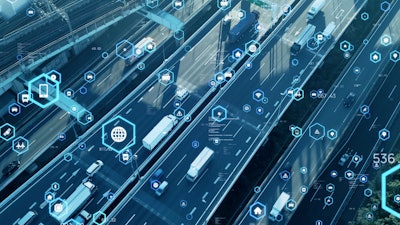
The food industry is under pressure from all sides. The global population is expected to reach 10 billion by 2050, with research from the UN Food and Agriculture Organization (FAO) showing we’ll need 70% more food in 2050 than in 2009. At the same time, raw material, energy, and fuel prices are soaring, water demands are growing, and infrastructure is ageing.
For companies in the food and beverage (F&B) industry, these are daunting challenges. There isn’t a quick fix, but there are ways businesses can drive efficiency to reduce waste and emissions and save on energy and material costs. Specifically, by implementing digital technologies to meticulously track processes in all phases of production.
The destination is indisputable, but the journey is more complex. Manufacturers have used cloud-based data management tools to see quick and substantial returns on its investment.
These connected systems enable employees to understand the profitability and efficiency of assets and are driving long term savings and improved sustainability.
However, addressing plant efficiency alone will not bring about the change necessary. Organizations need to continually drive cost savings across their whole operations. In this piece, we’ll tackle the challenges of implementing an enterprise or even ecosystem wide strategy to drive efficiency, sustainability, and profitability.
Data multiplicity and standardization challenges
Increasing productivity, efficiency and sustainability on a major inter-enterprise scale takes careful coordination. Success depends on stakeholders at all levels of the organization having enterprise-wide visibility and easy access to standardized data for decision-making.
That is not a simple task. Take the challenge of measuring energy and water usage, carbon emissions, and other sustainability metrics. Companies in the F&B sector will need to aggregate and manage extraordinarily high volumes of data from diverse inputs inside and outside the production environment.
At the same time, they must ensure that data collected from a multitude of siloed production areas is consistent, accurate, and of the highest quality. Data must be harmonized to account for differences in reporting standards and variations in data sets. Otherwise, differences can unintentionally muddy the waters when it comes to decision-making.
Managing geographic complexities in global operations
These challenges are compounded when managing facilities globally. Geographical differences make optimizing processes and setting reduction targets for energy, emissions, waste, and other sustainability metrics much harder.
Companies must contend with regional industry standards, energy costs, regulations, compliance requirements, and other factors that make it difficult to benchmark and implement best practices across a global enterprise, much less up and down the value chain.
Intelligent operations centers enhance visibility
There are solutions for these challenges. Companies seeking to improve efficiency and sustainability can achieve real-time visibility into every aspect of their global enterprise through an intelligent operations center.
Data-driven solutions supercharge sustainability
CPG companies need these flexible, scalable solutions customized to specific verticals to meet their sustainability and efficiency goals. Powerful digital tools which allow them to visualize and securely share real-time data within their network are essential to unlock efficiency, reduce waste and drive sustainability.
Data must be at the center of any solution. However, this data must also be as reliable, secure and standardized with historical data from production processes, energy consumption, supply chain operations, environmental factors, and other sources to drive true value.
Armed with this data, combined with artificial intelligence (AI), machine learning and advanced analytics, organizations can more effectively uncover patterns and anomalies. Customizable dashboards can intuitively visualize key performance indicators (KPIs) for data-driven insights into sustainability performance and operational efficiency.
These facilitate decision-making and collaboration between stakeholders in all corners and levels of the organization to drive continuous improvement across the whole enterprise, rather than at single sites.
Meeting the technological challenge
One of the biggest challenges facing F&B is that many of its systems were designed and installed decades ago and based on hardware. This means operators are tied to a single supplier, have very little flexibility, and a lot of complexity, managing hundreds if not thousands of pieces of hardware, all of which needs to work together seamlessly in production.
These hardware-centric systems simply don’t support the automation needs of today’s F&B industry as it strives to improve operational resilience, engineering flexibility, data transparency and agility. Automation sits at the heart of operational technology, optimizing energy, raw material usage and processes, driving competitiveness, productivity and environmental process.
It doesn’t have to be this way. Industry must move to a software-defined automation model, decoupling from hardware to create agile and scalable industrial environment. With an open platform that unifies assets from different brands and systems through a common language, companies can be free from closed, proprietary technology and create an ecosystem of best in-class solutions.
Software-defined solutions seamlessly integrate with other technologies to provide a digital backbone for automation, keeping pace with the demands of today’s agile and digital world, becoming future proof to new innovations.
This software-defined approach to automation optimizes manufacturing processes, fosters predictive maintenance and quality improvement. All while enabling seamless integration of new and existing automation systems and design. However, this model requires expertise to implement and integrate.
Choosing the right partnership for success
Where is a good place to start? Manufacturers in food and beverage should partner with established companies with specific segment experience and a proven track record of delivering success when looking for solutions. A deep understanding of energy management, automation, and digitalization is essential. Expertise in automation, sustainable performance and digital transformation across numerous industries is also beneficial, as a successful facilitator will understand the complex challenges consumer packaged goods manufacturers face.
A collaborative approach enables these companies to leverage cutting-edge technologies, data-driven insights, and best practices. This all helps to achieve sustainability goals, improve operational performance, and stay ahead in today’s competitive and increasingly challenging business landscape.
The road to an efficient and sustainable future has many challenges. With the help of data-driven insights and advanced AI-enabled digital tools, food and beverage producers can reduce time to market, costs and their carbon footprint, while improving flexibility, reliability, and meeting the new scale of global food demand.