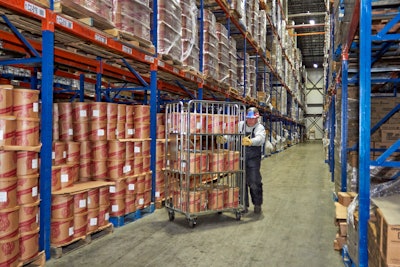
The picking, transporting and delivering challenges of Simco Logistics, Inc. were recently rectified with the smart use of technologies, leading to dramatic results for the direct-store-delivery company.
Simco Logistics is a family-owned distributor of ice cream, frozen foods, beverages and deli products to convenience stores, grocery stores and other food retailers throughout the Middle Atlantic. Founded in 1929 as Jack & Jill Ice Cream, it operates one main distribution center (DC) in Swedesboro, N.J., and ships to 12 cross-dock facilities that support 110-115 direct-store-delivery (DSD) routes per day in the Mid-Atlantic U.S., with routes increasing during peak season.
As a DSD company, delivery accuracy and efficiency are core to Simco’s mission and success. Upgrading warehouse technology and systems to optimize DC operations has downstream benefits for delivery drivers and customers. So, focusing in these areas was a priority.
The challenges
Simco was looking to mitigate its challenges (inefficient manual batching, picking and shipping errors and the reliance on paper-based picking and truck loading) with an upgrade to its warehouse technology. It also wanted to automate its manual processes with an intelligent, voice-directed system suitable for use in a deep-freeze warehouse environment.
At one time, orders from the enterprise resource planning (ERP) system were printed on paper rack sheets. Each sheet was made up of multiple customer orders, which were grouped together using detailed rules based on volume, weight and how racks could be loaded on the truck. Managers would print out rack sheets and hand them to DC workers who used them to guide their picking. Frozen and non-deli refrigerated items weren’t organized by customer order or stop, which created a challenge for delivery drivers.
After picking, completed racks and pallets were staged on a loading dock, and they were then loaded onto trucks or trailers in a paper-based process. The trailers are driven to the satellite cross dock facilities where items were transferred to local delivery. In the paper-based loading process, racks or pallets occasionally would not be loaded on the correct trailer or truck, which would lead to returns and rush delivery of missing items to the cross docks or customers.
The solution: Intelligent picking and loading
Simco made significant changes, guided by Lucas Systems, which gives companies a competitive edge by helping them work smarter with the use of warehouse optimization and adaptive voice-directed workflows and technologies.
Lucas helped Simco to create a paperless voice-directed picking process across the refrigerated and frozen areas of the DC. They also added intelligence to create more efficient groupings of orders on the racks, and to subdivide the racks into locations so that items for a given order could be grouped together. Better grouping of orders on the racks was intended to improve the delivery process.
In the new system, Jennifer – the voice and intelligence of the Lucas software – tells pickers what location to pick from, how many to grab, and in which rack location to place the items. In addition, Lucas creates a rack or pallet license plate that indicates which orders and items are on each rack.
The Lucas solution also includes a voice-directed loading application verifying that the correct racks and pallets are loaded on the appropriate truck or trailer. Workers scan the license plate IDs (LPNs) on pallets or racks to confirm what they are loading, and they verbally enter the truck number and tell Jennifer where they are placing the racks on the truck. Jennifer validates the racks and pallets, and she tracks where items are placed. She warns workers if they attempt to load a rack on the wrong truck and she prevents workers from closing a truck or trailer if there are missing racks, pallets or totes.
Based on information collected during the loading process, Jennifer creates a trailer map showing the location of all racks and pallets on the trucks. The load map aids drivers during delivery or cross-docking from trailers at depots. Drivers also benefit from the Lucas LPNs, which help them identify which racks contain which orders and items so they can off-load items from the trucks faster and more accurately.
In addition to the voice-directed loading and picking applications used by workers, the Lucas solution includes a management console that gives supervisors real-time insight on productivity, workflow, exceptions, and other operational data. Supervisors use the dashboards to manage orders and assign trailers to dock doors, in addition to monitoring performance throughout the shift.
Results: Accuracy and efficiency gains for warehouse workers, supervisors and delivery drivers
Picking
Since implementing the Lucas solution, picking errors have been reduced by more than 60%. Picking productivity at Simco has also improved significantly, although that was not the main objective of the project.
Loading
Loading errors have been nearly eliminated, and this has led to less re-delivery of missing items, fewer returns and less double-work picking items that were not delivered.
Optimizing delivery
The warehouse updates, including the truckload maps and rack/pallet LPNs generated by Lucas, have also had downstream benefits, helping delivery drivers save time at the delivery locations.
Paper-free reporting
The warehouse uses 50% less paper today. With less paper to coordinate, managers are spending more time on the warehouse floor.
“We wanted to increase accuracy, streamline the process and eliminate the paper,” says Ken Schwartz, CEO of Simco Logistics. “And, we are always looking for better ways to make it easier for drivers to make their deliveries.”