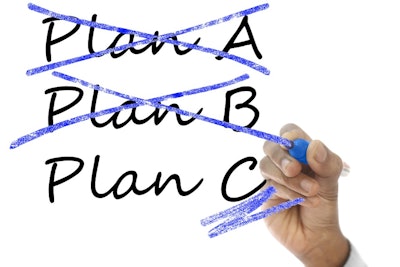
As Glinda the Good Witch says in The Wizard of Oz, “It’s always best to start at the beginning.” In supply chain planning, that equates to developing robust demand planning capabilities.
The accuracy of your forecast has a direct impact on the amount of inventory you carry, the number of unplanned production changeovers, and the amount of expedited material shipments. A highly accurate forecast of demand makes all supply chain planning and execution more efficient and effective. Luckily, today’s advanced demand planning solutions provide the tools needed to improve forecast accuracy automatically without having to have a PhD in statistics.
With new products making up an increasing portion of revenues and profits in the food and beverage industry, the successful introduction of new products is key to survival. Lack of data demand for new products makes it difficult to forecast using time series or qualitative techniques. However, attribute-based modeling techniques that use Chi-squared analysis to develop demand profiles based on attributes, such as package size, flavor or geographic distribution, can significant improve new product forecasting accuracy. As a product’s actual demand starts coming in its demand profile can be automatically adjusted or a new demand profile to maximize forecast accuracy.
Product Demand Profiles
Listed in the balance sheet, inventory tends to attract a high level of attention from senior management. So even though supply chain professionals understand that inventory levels are a byproduct of other business decisions, like level of customer service, supply chain design, product quality, and the ability to predict customer demand, they understand that minimizing total inventory while supporting business objectives is a career sustaining imperative. Advanced inventory planning solutions like multi-echelon inventory optimization (MEIO) provide the power to automatically determine the best inventory positions based on forecasted customer requirements and business objectives. Optimal inventory control parameters can then be used to drive manufacturing, purchasing and distribution to ensure the right products are available at the right place and time through demand-centric and time phased replenishment and manufacturing planning.
The Inventory Efficient Frontier
Replenishment planning allows you to resolve potential availability issues before they happen by projecting detailed demand, supply and inventory levels into the future. Advanced replenishment solutions provide the ability to run “what-if” scenarios to develop optimal strategies to overcome future potential shortages or surpluses.
Product portfolios also continue to grow to meet increasing customer product demands and the channels of distribution in which customers want to buy products. As portfolios increase, so do the number of items with slow and intermittent demand. Statistical methods have a hard time creating accurate forecasts for slow move items and just don’t work when forecast time periods have zero demand. Luckily, stochastic replenishment planning can be used to tackle the long-tail of inventory items. Stochastic replenishment planning anticipates the timing of intermittent demand by determining the lead-time probability distribution of demand and the probability distribution of demand periodicity. Stochastic replenishment planning creates the appropriate replenishment orders based on the probability of demand happening inside the lead-time, and balances the risk of overstock versus the risk of understock. Segmentation can be used with stochastic planning to group items by acceptable out of stock percentage. The result is a series of replenishment orders for items with intermittent demand optimized by product importance.
Slow and Lumpy Demand
Manufacturing planning should use inputs from demand, inventory and replenishment planning to determine how much of what products to produce when to minimize total supply chain costs while meeting customer requirements. Food and beverage manufacturers that have more than one manufacturing facility need two different levels of manufacturing planning.
First, aggregated levels of production quantities need to be assigned to production sites based on expected demand and known capacities. Second, detailed batch processes need to be planned at each plant to meet customer orders. These two planning levels need to be synchronized and aligned. Advanced manufacturing planning solutions will develop optimal aggregate and detailed production plans to minimize total supply chain costs, while considering all supply chain constraints and objectives.
End-to-End Supply Chain Optimization
Sales and operations planning (S&OP) rounds out a robust food and beverage supply chain planning foundation. Helping to align and synchronize expected demand to available capacity, S&OP has been a critical supply chain planning process for close to 30 years. Although the focus of S&OP hasn’t always been clear, it should be squarely focused on identifying misalignments and risks far enough into the future to provide time to make significant changes. Instead of examining detailed manufacturing or distribution schedules, S&OP should be focused on the aggregate to analyze long term staffing, equipment, facility, partnership, product and market scenarios. S&OP provides that longer-term focus to determine optimal tactical and strategic supply chain decisions that is often missing from supply chain planning operations.
Robust demand, inventory, replenishment, manufacturing and S&OP capabilities provide the foundation on which to build more advanced supply chain planning capabilities. If you haven’t built out this foundation, now is a good time to start.
Computing power is less expensive and more powerful than ever, allowing for complete end-to-end supply chain optimization using advanced algorithms. Today’s modern supply chain solutions have been built to take advantage of this increased computing power, while incorporating user-friendly interfaces and powerful data analysis and display capabilities. Big data is here and is providing competitive advantages to those companies that have figured out how to use it. Machine learning and artificial intelligence capabilities that help automate planning tasks and free up planners to tackle more value added activities are available today.
However, without a solid foundation, trying to adopt algorithmic planning, big data, and artificial intelligence can be an exercise in futility. The war for supply chain planning talent is fiercer than ever. The millennial workforce will migrate to those companies that provide advanced tools with powerful user interfaces that help them maximize value-added contributions. Think of an investment in supply chain planning capabilities as a way to attract and retain the best talent.
Are you considering improving your supply chain planning capabilities? If so, what steps are you taking to build a stronger foundation?