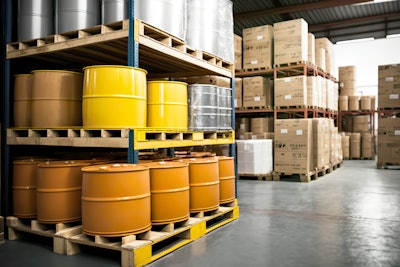
With global supply chains facing ongoing challenges, organizations need to remain competitive and are investing in new solutions and processes to overcome systemic stress factors, optimize performance and reduce operating costs. While most already leverage technology platforms for transportation, warehousing and order management, many overlook one facet of the supply chain that can help or hinder their success: dangerous goods (DG)/hazmat automation.
However, simply implementing an automation solution isn’t enough – many platforms lack the functionality required to specifically address the DG shipping processes. That’s why it’s important to borrow a page from Stephen Covey’s book “The 7 Habits of Highly Effective People” and begin with the end in mind. By envisioning an environment that’s both compliant and automated, businesses can move goods safely and efficiently through the supply chain and realize many operational and financial benefits.
Today’s Dangerous Goods Supply Chain
Before we can address automation, it’s important to understand the current DG supply chain. Shipping and handling DG — from industrial chemicals and pharmaceuticals to power tools and cell phones — can be complicated. The regulations are complex, change frequently and vary depending on how and where the goods are transported.
Those regulations impact nearly every aspect of getting a DG shipment fulfilled, out the door and delivered to a customer. Slow compliance processes mean slower fulfillment, deliveries and overall business. And many operations still rely on manual or rudimentary processes for compliance, since almost all supply chain and logistics automation platforms don’t fully address it.
Shipping hazmat compliantly can be extremely time-consuming for organizations using manual processes. Any given shipment forces teams to answer a number of difficult questions, from classification of the materials to documentation to which labels and marks need to be applied. When manual processes divert hazmat shipments from standard transportation management systems (TMS), warehouse management systems (WMS) or enterprise resource planning (ERP) workflows, it doesn’t just add time for every shipment, it also ties up workers who could otherwise be performing more productive tasks.
For example, take an operation that processes DG shipments manually. If 10% of their shipments contain hazardous materials such as flammable liquids, corrosives or lithium batteries, that means they have to divert one in ten shipments from their standard TMS, ERP or WMS workflow to assure compliance. Even if that only adds ten minutes per shipment, it’s a severe handicap in today’s landscape.
These delays and inefficiencies can add up to significant productivity losses. And when consumers and businesses expect their goods to be delivered the next day — if not sooner — efficiency is paramount.
It’s also easy for people entering information manually to make mistakes — and compliance errors can bring about delays, stopped shipments, carrier penalties, civil penalties and other schedule-wrecking disruptions. That’s why it’s important for organizations to understand the role effective DG management plays within the supply chain and the impact it can have on the overall business.
Establishing an Efficient and Compliant DG Supply Chain
Establishing effective and efficient DG management processes may seem like a daunting task, but it does not have to be difficult, slow, or expensive – even on an enterprise scale. A strategic approach using the right product information, technology, processes and people will put your organization on the path to success. But where do you start?
If we adopt Covey’s second habit of beginning with the end in mind, that means we should “begin each day, task, or project with a clear vision of your desired direction and destination, and then continue by flexing your proactive muscles to make things happen.”
Your organization should begin by defining its overarching goal, whether it’s to streamline operations, enable faster shipping, mitigate risk, increase revenue or something else. No matter the overarching goal, repeatable, reliable, safe and expedient DG shipping is sure to play a critical role.
Once the end vision is defined, companies must then identify the steps a company should take to get there.
A Strategic Approach to Effective DG Management
For organizations that want to become more automated and consistent in their DG processes, it boils down to a few key components:Labelmaster
- Have the right information.
- Ensure the right processes are in place across the supply chain.
- Make your processes as efficient as possible.
- Enable proper deployment and adjust as needed.
Now that you have a roadmap, you need to need a plan for how to put it into place. Your approach should include the following:
- Have the right product information. A product’s components, dimensions and origins impact every process required for safe and compliant shipping. Shippers must first know exactly what they’re shipping, then understand the regulatory requirements or restrictions for those goods.
- Ensure that the right processes are in place. Once an organization knows what it’s shipping and the rules for transporting those goods, it can then define the specific processes that are needed to ship those goods safely, compliantly and efficiently. These processes should be reliable and repeatable, across all locations and supply chain partners.
- Utilize technology to enable efficient shipping processes. Establishing repeatable and reliable processes across the supply chain can be significantly enhanced through automation. DG shipping software can validate orders against the latest regulations and drive efficiencies for repetitive shipments from the same or multiple locations. Dedicated DG shipping software can often integrate directly into other operations and systems, giving organizations the tools to achieve functionality via a single, familiar user interface.
- Enable proper deployment and training. Even with increased automation, training is still required for employees involved in shipping DG. Organizations must ensure they train and re-train employees to use the proper technology, packaging and labeling to affect DG shipments. Adopting a modern, tech-driven approach to hazmat training through eLearning helps businesses quickly and effectively train and recertify employees — and do so remotely.
The Benefits of Fast, Reliable DG Shipping
Repeatable, reliable, and automated DG shipping processes provides operational benefits in several key areas, which will likely align with your organization’s end goal, including:
- Efficient shipping. Automation helps establish repeatable and reliable operations, supports faster shipping processes while also helping ensure regulatory compliance for every shipment, across all locations.
- Reduced operating costs. Faster, more efficient compliance processes simultaneously enable organizations to operate more cost-effectively and reduce the risk of fines.
- Risk mitigation. Ensuring compliance with every shipment reduces the chance of a DG-related shipping incident that could impact employee and public safety, the environment and brand reputation.
- Resource utilization. Automating and streamlining DG shipping processes empowers organizations to better utilize their workers, allowing them to grow and scale when demand increases without having to add additional personnel, which helps offset labor shortages.
- Supply chain resilience. Establishing repeatable, tech-enabled processes lets organizations put in place robust business continuity steps that allow them to ship DG from multiple locations. This not only helps ensure consistent compliance across locations that regularly ship DG but provides flexibility to shift DG processes and shipping to other locations when customer demands change or disruptions arise.
Keeping the DG Supply Chain Moving
Keeping goods moving in the face of ongoing supply chain disruptions, labor and material shortages, and other challenges that will continue to emerge will put compounding stress on businesses shipping DG. Establishing reliable, repeatable and automated compliance processes across the supply chain will become increasingly critical to maintain fast, resilient, efficient and complaint operations. As you move forward in your compliance journey, establish your end goal and then strategic roadmap to get you there.