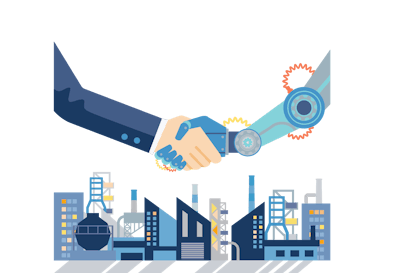
They won’t ask for sick time. They won’t complain about overtime hours. And you’ll never hear about their weekend exploits. But when you really do the analysis, is it worth considering the deployment of robot “workers” as your next labor strategy to improve your warehouse efficiency?
Predictions of long-term labor shortages across the U.S. and Europe as well as continued pressure on supply chains to deliver orders faster and more accurately have caused operations executives to seriously evaluate that question as they look for answers to staffing challenges. The good news is that cost reductions in automated material handling equipment and advances in machine learning and robotics have made such technology tools considerations fair game for warehouses of all sizes.
Supply chain operators are taking full advantage of shifting market forces. Research firm Tractica estimates warehouses will invest a staggering $22.1 billion globally in robots in 2021, up from $1.9 billion in 2016. More organizations now see automation and robotics as a top solution to address a wide range of warehouse challenges, from increasing capacity utilization and picking efficiency to labor reduction and improving order accuracy and cycle time.
New internal and external demands can also drive warehouse operators to investigate new technology. With the rapid growth in the e-commerce sector, many need to fill orders faster to meet customer service expectations. Others want to develop new offerings, such as subscription commerce boxes, that require peak efficiency. Still, others are motivated to keep up with competitors, many of whom have turned to automation to gain the upper hand.
Emerging Technology
Automation and robot technology in the warehouse has come a long way since the first automated guided vehicles (AGVs) began making warehouse rounds in the early 1950s, diligently following their wired pathways through aisles, aiding pick and putaway operations.
The latest generation of warehouse robotics, autonomous mobile robots (AMRs) still perform the same functions as AGVs, moving material from location to location within distribution centers—but do it faster, smarter and more efficiently. Instead of relying on buried wires or magnetic tape for guidance, AMRs can navigate dynamically to complete material handling tasks, using an on-board map that can easily be updated should the warehouse configuration change. These robots are smart enough to find their way around obstacles and can safely navigate around people or other equipment.
In addition to basic stock movement and replenishment tasks, modern robotic automation is also changing the traditional “man to goods” model where employees walk warehouse aisles, following pick lists from shelf to shelf to fill orders. AMRs reverse the process with robotic vehicles bringing items to employees who staff pick locations and fill orders—reducing employee travel time and increasing pick accuracy.
Reports of employees being forced to walk 10 to 15 miles per shift may be exaggerated, but it’s not hard to imagine the efficiency savings in employee travel (as well as the satisfaction improvement) by allowing robots to “do the walking.” And while robots with advanced pick and pack capabilities have yet to produce a foolproof automated picking and packing operation, this technology isn’t far off. Amazon, which pioneered the use of mobile robots in its U.S. facilities after acquiring Kiva, sponsors a global competition every year to identify and promote robotic technology to perform advanced pick processes.
Where Is It All Leading?
So, are we headed towards a complete warehouse labor pool comprised of robots sporting artificial intelligence and machine learning? Probably not—at least in the near term. Even the newest bots require configuration and set up to perform their automated functions. Artificial intelligence and advanced machine learning, where the rules and algorithms controlling the devices can be self-modified based on experience, are still emerging technologies.
Within the next 3-5 years, it’s likely that applications will appear where information is consumed around items, people, processes and order profiles, as well as the physical organization of the warehouse to recommend workflows that best handle the work. These applications are also likely to be costly and be appropriate for only the largest operations when first rolled out.
One thing is clear—embarking on a strategy to enhance or replace portions of your labor pool with automated devices isn’t a quick decision. It requires significant thought and long-term strategic and operational planning. And, before you consider adding a new robotic component to your warehouse operations strategy, it’s best to consider the systems already in place to ensure successful integration. For example, even in the most automated warehouse, a warehouse management system (WMS) is the core to the entire operation. It maintains critical data on inventory, orders, workforce management and the like. Properly configured, it will provide the baseline for managing automated equipment. Without it, attempting to manage a robotic workforce can be as or more difficult as dealing with the human equivalent.
Innovative companies do feel the use of robotic technology has reached the point where it’s accessible to all operations and are working on applications to integrate advanced automation with their WMS offerings.