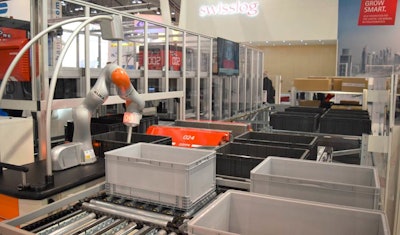
Robotics and automation are not widely used in the food and beverage supply chain compared to some other industries. But adoption is expected to accelerate, given the improved efficiencies they bring and the requirements of the expanding e-commerce sector.
Robotics and automation were cited as the leading source of disruption or competitive advantage by the Material Handling Institute’s 2016 Annual Industry Report; these technologies were cited by 51 percent of respondents, up from 39 percent last year.
In recent years, funding sources have invested significantly in logistics robotics, according to DHL in a recent research report.
In 2012, the U.S. government granted a total of $50 million to universities for robotics research. These grants were the first step in the Obama administration’s National Robotics Initiative (NRI) with the goal of creating the next generation of collaborative robots.
In addition, venture capital invested in robotics for the first five months of 2015 exceeded all robot-related equity funding in 2014 combined. Amazon and Google represent a third source of robotics funding.
Innovation Continues
There have been some fundamental technological breakthroughs that can be used to create the next generation of robots, DHL noted in its report. These enabling technologies include low-cost sensors, faster computers, Big Data analytics, more powerful batteries, cloud computing and mobility.
Robots are increasingly able to demonstrate “human” capabilities and traits such as sensing, dexterity, memory and trainability. They are being integrated into supply chains, taking on more human-oriented tasks, including picking and packaging.
Until recently, robotics technology has not made a big impact in logistics, DHL noted. This is about to change as advanced robots enter warehouses, sorting centers and even help with final-mile delivery.
Robotics represent the next level of technology in distribution warehouses. They mark an upgrade beyond the material handling automation solutions such as conveyors, sorters, goods-to-picker solutions and other mechanized equipment to improve the productivity.
While some of the components of these systems [automated storage and retrieval systems (ASRSs), automated guided vehicles (AGVs) and shuttles] can be considered as a type of robot, they do not provide the same level of robotic functionality that industry observers say will be common place.
At the present time, most distribution warehouses have yet to deploy automated material handling solutions, let alone robots.
Warehousing Trails Production
In the food and beverage space, the production and processing sectors have been the most technologically advanced. Observers believe the warehousing sector will be catching up in the near future.
“Robotics started in palletizing with food, then migrated to secondary packaging and later in primary packaging and processing,” says Raad Asmaro, an account manager at FANUC America Corporation. “We continue to develop robotic solutions to tackle logistic applications like mixed load palletizing, depalletizing, tote picking and handling, ASRS, robotic labeling and truck load and unload. Anytime you have a demand, robotic technology will evolve to make the impossible possible.”
“It will eventually evolve its way downstream more and more into logistics as robotic solutions become more common,” he says.
Asmaro is one of several observers who point to Amazon as a warehouse technology pioneer with its automated good-to-picker system and mobile robot that moves inventory from one area to another. “When Amazon is satisfied with their robotic automation, everybody will follow,” he says.
Good-To-Picker Makes Strides
The goods-to-picker concept can be found in several technologies on the market today such as Swisslog´s CarryPick mobile system. It is possible save 50 percent of warehouse picking labor with these systems through the elimination of walking.
Currently, most of these systems are highly capital intensive, requiring a network of connected shelves, tracks, robotic shuttles, elevators, and conveyors. Even after this investment, they still require people to pick items from an automatically presented plastic tote or mobile shelf.
The manufacturers of goods-to-picker material handling systems have seen this problem as an opportunity to introduce robotic arms into their systems.
SSI Schaefer’s Robot-Pick.65 uses a camera to identify items in a plastic tote which has been delivered to the work cell by one of SSI Schaefer’s large automated tote storage and retrieval systems, the DHL report notes. The stationary robot bolted inside a traditional robot work well uses a camera to identify items in a plastic tote delivered to the work cell by one of SSI Schaefer’s large automated tote storage and retrieval systems.
Once the robot locates an item, it picks it up and places it on a small buffer conveyor that deposits the item in a separate transport tote. The company claims its robot can pick up to 2,400 items per hour depending on product characteristics and order profile.
KNAPP AG and Viastore have developed similar systems. KNAPP’s Pick-It-Easy Robot can automatically change its vacuum cup gripper to better match the product, while Viastore’s viapick system not only picks anitem, but can place it into a shipping carton as well.
The opposite of the goods-to-picker system would be a mobile robot that drives around warehouse shelves and picks items just like a person would.
Robotic Picking Arrives
IAM Robotics is currently developing a mobile robot with an arm on top and a camera system that can navigate an existing warehouse and pick items from shelves and place them into an order tote. The system was field tested in a warehouse where it was able to pick test orders from 40 items that it had never seen before.
The robot will be tested in a more general goods warehouse where it will be integrated with a warehouse management system (WMS) for the first time and pick live orders. IAM Robotics hopes to have a commercial version of its system available sometime in 2016.
The robot uses a 3D depth camera to identify items to be picked. The company has its own software that allows the machine to recognize certain objects and know where to grasp the product, says Tom Galluzzo, CEO. The first deployment will be in a pharmaceutical distributor, but Galluzzo sees “tremendous” application to the food industry, especially e-commerce fulfillment.
“We’ve talked to a number of folks that are interested in dark store applications,” Galluzzo says. “Grocery e-commerce has been successful in certain areas,” he says. He sees AmazonFresh as a major force for food e-commerce.
Target: Order Fulfillment
Galluzzo sees robotics’ main application in the fulfillment area. “The more advanced applications to robotics and the lower hanging fruit on cutting costs and increasing throughput productivity is in the fulfillment operation,” he says. There is also a lot of interest in deploying autonomous vehicles for home delivery, but this is further in the future.
“I think it is the retailers [food and non-food] that are preparing for the larger dynamic of consumer trends,” Galluzzo says.
“This is more of an early adopters game,” he adds. “It’s absolutely going to be commonplace five to 10 years from now.”
E-Commerce Drives Growth
The DHL report notes the expansion of e-commerce as a driving factor. Instead of moving product to a retail store in bulk, the organization must pick and pack online purchases individually by hand. The need for freight and parcel handling labor increases since these goods must be shipped as separate parcels to be delivered directly to consumers’ homes.
The technology is beginning to catch up with the need to have a robot that is flexible and low cost enough to work in the logistics and distribution environment.
Patrik Seibel, global market leader for food and beverage at Swisslog AG, says some of these systems have deployed in food retail environments. Swisslog’s parent company, KUKA, has deployed robots in food production environments. Swisslog is using the KUKA robots to handle single items or crates of food. The new KUKA LBR is a collaborative robot this is safe to be in the same environment as humans.
“Food has historically dealt with full pallet movement of one SKU, and is now seeing [or ‘feeling’] what e-commerce can do to their traditional order fulfillment model,” says Sean O’Farrell, market development director at Dematic Corp. “I believe the food sector has been taking a ‘wait and see’ approach to robotics because of the rapid changes made in other markets and the tight margins in the food industry.”
In North America, grocery warehousing is investigating and implementing robotics because of labor availability and the effect of e-commerce, O’Farrell adds. “Orders are becoming smaller and more frequent, which changes the order build and delivery of the orders. Grocers are looking for flexibility in fulfillment, but are not experiencing the flexibility because a lot of their time is spent on finding and training employees to work in a very demanding environment. The right robotics solution can be a complement to flexible order fulfillment operation.”
Buying Habits Change
“As the buying habits change from consumers and requirements change from retail and warehouse customers, the complexity becomes greater,” says Tom O’Dette, director of engineering at Retrotech. “Robotic solutions have proven to bring an opportunity to increase speed, accuracy, efficiency, flexibility, along with reduced cost. The demand for robotic interest has been strong in this market, but it starts with clearly defined economic and competitive benefits. Our design and analytic teams are engaged in more projects than ever before.”
When designing the next generation of logistics robots, there is one key element needed to tie together advanced perception, mobility and collaboration: computational power, also known as “brains.” More than any one component, the emergence of advanced robotics is clearly tied to improvements in computing speed and power.
Advances in visual image processing, real-time obstacle avoidance, and other functions require access to cutting-edge mathematical algorithms and faster computers. Robots will continue to improve and assume more complex tasks as computational power increases.
“We’re seeing more and more of it in the U.S.,” including food companies, says John Clark, director of North American marketing at Egemin Automation Inc., a system integrator which makes AGVs and deploys software in automated material handling equipment. Clark notes that facilities with older, early-generation automated systems are now looking to modernize that existing equipment with newer software and controls that improve operation and extend the life of equipment. “Automated picking allows for more accurate and more precise picking methods,” he says.
Modern AGVs do more than just move items. They can be fitted with forklifts or clamp lifts to pick up and transport products in a warehouse. They can also have conveyor roller sections on them that allow the AGV to transport product from an ASRS to an AGV to transport to other areas of a distribution center.
Traditional Versus Collaborative
Observers agree that both traditional and collaborative robotics will find a place in the food supply chain. Traditional robots are typically fenced off to prevent contact with humans, while collaborative ones are designed to interact with humans.
“I think the classic [traditional] approach is still the more likely application,” Swisslog’s Seibel says, because it is faster. “If there is no need (for human presence), it’s easier to fence it off and have a higher performance,” he says.
“Traditional robotics will have most of the play with order picking, mixed case palletizing and transportation,” says O’Farrell of Dematic. “I believe collaborative robotics will be slow to develop in the food sector, but can start out in value-added services like kitting of products, labeling, piece picking,”
The cost of automation is coming down, O’Farrell adds, while the costs to process an order are going up. “This is making the investment more ‘palatable.’ However, companies are finally taking a longer view to investments and not looking to hit a two-year ROI because of shareholder demands. Companies understand that taking a five- to seven-year approach is a better strategy and gives a competitive advantage with the right kind of investment.”