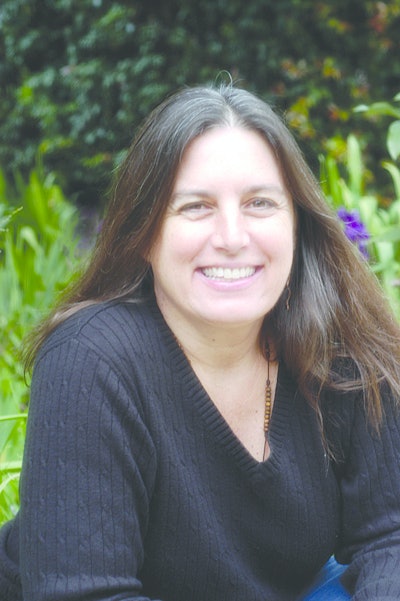
Leading cold storage providers are on a buying and expansion spree. This year has seen a number of M&As and new projects to meet increased demand for temperature-controlled facilities to support the transportation and distribution of fresh and frozen food.
Firms such as Stellar that specialize in the design and construction of these facilities understand the complexities and requirements of today’s cold storage facilities. In a recent white paper, Stellar shared the benefits of an integrated, team approach to designing a cold storage facilities while staying within budget considerations.
Taking an integrated approach
Industrial designers, architects, mechanical engineers, refrigeration experts and a thermal team all working together can lead to a more functional, efficient, and cost-effective facility. Working with multiple contractors in multiple locations increases the likelihood of miscommunication, competing workflows, and increased costs — in addition to a longer production schedule.
The benefits of employing a team approach to building a distribution facility include:
1. More informed decisions through building information modeling (BIM) — BIM allows all team members to see a three-dimensional view of the facility and many owners find it beneficial for the team to take a virtual walk-through together to address workflows. For example, refrigeration and mechanical engineers can review the layout with owners to ensure an efficient path for maintenance personnel to access equipment, or review piping arrangements to ensure they are fully coordinated with the building structure.
2. Industrial designers and product experts — Hiring a team with experience in the distribution industry can improve the facility’s overall function and workflows, in that there is required logic and intelligence behind the facility layout, product location, racking type, material handling devices, and picking methodology. Designers can work directly with internal distribution industry experts to optimize and analyze the product demand and picking process, placing faster moving products near the dock doors and slower movers in the back of the facility.
3. Refrigeration requirements — Because proper refrigeration is crucial to food safety in distribution warehouses, it’s critical that the refrigeration team and thermal experts collaborate with designers. With multiple temperature requirements within a single warehouse, refrigeration and thermal experts will often dictate which rooms need to be adjacent based on similar temperatures or future planned uses of a room. Thermal experts must also have input on the installation and thickness of the insulated metal panels between rooms, underfloor insulation, underfloor heat, and other related factors.
4. Projecting future temperature needs — As market demands change, so do the refrigeration needs for distributors. Refrigeration team members can often make recommendations to the designers on how to incorporate flexibility into cold storage areas. For example, a cooler can easily be converted to a freezer at a later date if properly designed initially. This provides more flexibility during future expansions to accommodate either cooler- or freezer-based products.
5. Location of mechanical room — With varying temperature requirements within the facility, electrical, mechanical and refrigeration engineers should work closely to determine the most efficient location of the utilities and mechanical rooms to ensure the most cost-effective solution, reliability, and energy efficiency.
6. Building envelope — The thermal team should be involved in every step of the process to determine the appropriate building materials. Roofing, insulated metal panels, and flooring will all be driven by the decisions made by other teams, with the potential to impact profitability and food safety.
And staying within budget considerations
From the outside, cold storage facilities can appear to be large, simple boxes. However that perception is far from reality—they actually require an advanced, detailed analysis in the design phase to achieve significant operational cost savings.
At its core, a cold storage facility is designed around the type of product to be stored and how long it will sit on the shelves. But as technologies and techniques aimed at improving efficiencies have proliferated, cold storage warehouses have become more complex to design. Here are five key budget considerations to keep in mind:
1. Energy Efficiency — Energy costs to operate cold storage facilities can reach tens of thousands of dollars each month. Factors that can influence and improve the energy efficiency of the facility include under-floor heating systems, consideration of adjacent room temperatures, and LED lighting. The orientation of a building can also improve energy efficiency with higher temperature rooms located at the southern end of the facility, and lower-temperature rooms at the northern end.
2. Refrigeration — Factors that influence the efficiency of a refrigeration system include compressor, condenser, evaporator and air unit selection, variable frequency drives, and premium-efficiency motors. These factors must be carefully balanced with operational demands and return-on-investment criteria.
3. Refrigeration Controls — In addition to mechanical efficiencies, automation can greatly improve refrigeration efficiency and optimize energy use. Automation allows engineers to generate trend analyses, alarm logs, energy management data, and runtime reports in real-time. This data allows them to make the necessary changes and modifications to ensure the refrigeration system is running at optimal efficiency.
4. Thermal and Roofing — With the staggering energy demands of cold storage facilities, it’s vital to construct a vapor barrier of uncompromising integrity. Numerous thermal details must be considered including insulation thickness for the floors, walls and roof, low-temperature door systems, and the use of insulated metal panels for adequate vapor seals. Roofing coated with a reflective white membrane can also reflect the sun’s rays for added energy efficiency.
5. Electrical Utilities — Loss of power in a cold-storage facility can lead to significant financial losses. Design considerations for electrical utilities should include operating voltages, reliability and redundancy of supply, standby generation and machine and electrical room locations that provide optimal utility distribution.