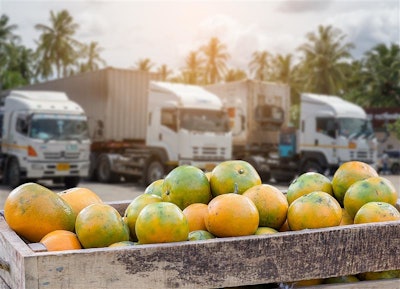
Choptank Transport is a full-service, third-party logistics (3PL) company offering full truckload (FTL) and less-than truckload (LTL) refrigerated and dry shipments for leading fresh and frozen food providers in North America and other international destinations. Headquartered in Preston, Md., — with additional offices in Baltimore, Tampa, Fla., Denver, Dallas and Atlanta — Choptank is a 3PL industry leader recognized for its award-winning customer service.
For Choptank logistics managers Douglas VanDerveer and Lora Creason, ensuring the proper temperatures within its refrigerated trailers (reefers) is an essential service that they provide to their customers. VanDerveer manages the LTL side of the business, where a single trailer may be loaded with multiple product types from different customers that need to be delivered to various destinations along a shipping route. If an LTL temperature rises above the desired setpoint, it could potentially threaten the quality and safety of the commodities onboard and thus affect multiple Choptank customers.
“If a delivery requires 10 different stops for 10 types of products, then the trailer’s holding temperature affects every customer in the shipment,” said VanDerveer.
Because of this, reefer temperatures must be monitored closely, especially during stops when reefer doors are opened, so that a particular product may be unloaded onto the receiving docks.
In the FTL scenario, Creason said that the shipments typically consist of one type of high-value perishable product that may be delivered to multiple stops throughout the country.
“From East to West Coasts, our customers typically require multiple drops along the way, so we’re always looking for any scenario that potentially could impact product quality,” she said.
To support their customers and protect profits, Choptank needs a logistics management strategy that allows for the continuous monitoring of locations and temperatures of their refrigerated FTL and LTL loads. For more than five years, Choptank has relied on Emerson to support this strategy with a technological infrastructure that delivers:
- Real-time access to the temperatures and locations of refrigerated shipments
- Alerts when temperatures deviate from shipment setpoints
- Data to resolve potential disputes and product refusals on receipt
- Information to make the best shipping and delivery decisions for each load
Challenge
According to VanDerveer, one of the biggest challenges of LTL shipments occurs when reefer doors are left open too long while the driver waits for product to be unloaded, making it difficult to maintain proper product temperatures. In fact, there are occasions when someone at the receiving dock may open the trailer doors for extended periods of time and then refuse the shipment due to the change in temperatures. In these instances, trucks are literally tied to the docks while waiting to be unloaded, which potentially may have further negative consequences by compromising the other products in the shipment.
“Oftentimes, it’s just a matter of a driver waiting for the paperwork to be completed to close the doors and release the trailer, but in the meantime, there are other products we need to protect,” said VanDerveer.
With the FTL shipments, Creason said that the logistics concerns are mainly keeping perishable product at the correct temperatures throughout a journey and making sure trucks are on schedule to meet their multiple drop-off locations. But even so, the potential for getting delayed at the receiving docks still exists, and Choptank needs the ability to verify reefer temperatures during transit and upon arrival at the receiving docks.
It’s important to note that a full download of reefer data (i.e., a reefer download), which pulls data from the unit itself, not the tracking devices, requires time to generate and does not provide instant access to live temperature data. Only the GO real-time trackers can provide that immediate information.
Solution/Result
In both LTL and FTL scenarios, the GO real-time tracker solution delivers what Choptank teams refer to as the “first line of defense” for protecting their refrigerated loads.
VanDerveer said that his team relies on real-time alerts to notify them when LTL loads are tied up at receiving docks and reefer temperatures start rising.
“Alerts let us know when our customers’ products could be in jeopardy, so we’re able to communicate with the receiver and the driver to make sure we get the trailer doors closed and out of the dock quickly,” he said.
If there are problems with product refusals or rejected loads, GO real-time tracker data helps pinpoint the precise times and durations of temperature spikes so Choptank teams can identify who is responsible and determine if product has been compromised. On FTL shipments, Creason indicated that her team leverages this data to not only resolve potential disputes at receiving docks but also make proactive decisions based on the locations and temperatures of in-transit shipments.
“If we see that a driver may be late to a delivery or there’s a discrepancy on the reefer temperature, we’re able to go into problem-solving mode to avoid issues before they occur,” said Creason.
Whether making decisions to reschedule a shipment, diverting a truck to inspect the refrigeration equipment, or resolving disputes at receiving docks, Choptank Transport relies on GO real-time tracker temperature and location data for real-time quality assurance.