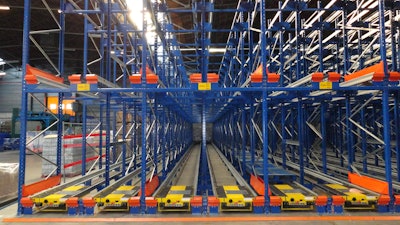
Because inventory represents one of the biggest costs in the food and beverage supply chain, material handling system providers continue to find ways to manage inventory more efficiently. As SKU proliferation, globalization, safety and sanitation requirements add costs to managing inventory, supply chain managers have to consider all options for improving this critical function.
Supply chains already invest significantly in material handling of inventory. A survey on material handling investment by viastore systems Inc., the Grand Rapids, Mich.-based material handling systems provider, found rack systems are the leading material handling application. The survey found that when asked about 11 material handing applications, 66 percent of the companies have rack systems; the second most common application was conveyor/sortation systems – 44 percent.
Food and beverage supply chain managers look at several factors when choosing inventory storage tools. A key consideration is improving storage density, along with minimizing product damage, protecting worker safety and ensuring product sanitation.
“Historically, food and beverage customers have chosen structural steel systems over rollformed steel systems due to the ease of cleaning structural steel systems,” says Mike Adducci, Midwest region area market manager at Chicago-based Interlake Mecalux. “That trend currently continues. However, that comes at a cost as well, as structural steel systems tend to cost quite a bit more per pallet position versus roll-formed steel systems.”
Pallet Flow And Other Options
Pallet flow racking – in which pallets are loaded at the top end of the slightly inclined rack and glide safely and effortlessly at a controlled pace to the other side -- is ideal for products with expiration dates, Adducci says. Since it is a first-in, first-out system that allows for precise product turnover, these systems are perfect for freezer warehouses, food distribution centers and most any type of high-volume consumer goods.
Push-back racking – which uses nesting carriages to store pallets up to five deep, providing multiple pick facing with extremely high throughput – allows for efficient use of space without sacrificing product accessibility, Adducci says. There is no wasted space with push-back. Because of the increased depth of the system, push-back minimizes the number of aisles needed to access product, creating a high-density, high-efficiency storage solution.
Selective pallet racking – which provides direct access to every pallet in storage – offers versatility for warehouses that have wide varieties of product types, Adducci says. High volumes of a limited number of products will more likely require a double deep system that has enough capacity to store two pallets deep by reducing the number of forklift access points. The double racking or back-to-back racking of the single deep system allows forklifts easier access to a larger number of SKUs stored at half the pallet depth.
Mobile Storage Systems Arrive
High-density mobile storage systems are gaining traction in North America since they optimize space utilization and decrease energy demands.
“Today’s cold storage warehouses need flexible, high-density storage solutions that unite efficient space utilization, direct inventory access, increased productivity, and reduced labor demands,” says Todd Jessup, principal at Storax America/Flexspace. “Cold storage environments are energy dependent and cost-intensive environments to operate and build; facility owners and managers are seeking storage methods that maximize their “cube” while trying to maintain immediate, unobstructed access to their products.”
The Storax Ranger, a high-density storage solution, automatically circulates pallets on a shuttle system. The system automatically circulates pallets on a shuttle system by hand-held remote control or WiFi PDA. Utilizing photocell technology, the Ranger detects and positions itself underneath a pallet to lift and move pallets within a deep lane tunnel rack system.
Storax Poweracks consolidate multiple static access aisles to a moving aisle. The system maximizes space utilization through use of a moving aisle, which provides direct access to every pallet location and reduce the number of static access aisles required.
Spacesaver’s mobilized storage system can make operations more efficient in cold chain environments as low as -4 degrees F, with optional stainless steel for performance at the lowest temperatures. By mounting new or existing racking onto mobile carriages and eliminating static aisles, a warehouse can double storage capacity. The mobile racking holds up to 30,000 pounds.
At one Midwest beverage distributor, an influx in craft and seasonal beer SKUs put a strain on cooler space and required employees to pull dozens of 170-pound kegs out of the cooler in order to access the items needed for daily delivery.
By installing the Storax mobile system, the distributor created space for 7,000 kegs, nearly double the capacity of their static racking. The high-density storage has allowed the distributor to more efficiently utilize their expensive cooler space and expand their number of offerings without sacrificing accessibility.
Pallet Versatility Plays A Role
ORBIS has expanded its pallets to allow companies more pallet versatility, thereby improving storage space density. One option is the 40 x 48 StackR pallet line, now expanded to include three pallets to meet a variety of application requirements.
The 40 x 48 StackR LD Pallet is the made of 100 percent recycled content and can stack up to 30,000 pounds. And, the 40 x 48 StackR MD and HD pallets are designed for racking and will rack up to 2,100 pounds and 3,000 pounds, respectively.
In addition to improving storage density, the pallets are non-porous and do not absorb moisture or odor. Customers can choose pallets with an open deck that creates a hygienic solution for customers who do not have pallet washers.
“There are also new pallet material options for different food applications,” says Curt Most, ORBIS Corp. senior product manager-pallets. “Specifically, metal detectable and X-ray detectable pallets are being considered to streamline the inspection process, while FDA-approved materials are important for direct contact applications. Companies also need to take into consideration the temperature of their facilities and develop a cold storage pallet solution accordingly. Hygienic pallets continue to be important as food processors strive to keep their plants and equipment clean.”
Consider Sanitation
Facilities with strict sanitation requirements cannot have painted carbon steel mezzanines, says Shannon Salchert, marketing director at Cubic Designs, the New Berlin, Wis.-based manufacturer of mezzanines. Instead, the mezzanines use stainless steel which is ideal for areas that require frequent washdowns since it is highly resistant to corrosion. Cubic Designs’ mezzanines also have a closed-shape design which minimizes catch-points in which debris or bacteria can gather.
Not all companies handling food and beverages have to adhere to the strictest sanitation constraints, which require all-stainless steel construction. One beverage manufacturer wanted all platforms to be constructed with closed shapes, aluminum decking, and to incorporate clean surfaces with minimal crevices and catch points in the structure.
Another beverage manufacturer needed a system that would prevent beverages from seeping through and collecting in crevices in the event of a spill. The solution was to use high density-wood with seal coating, along with an FDA-approved sealant to fill all joints.
Automation Brings Options
Automated storage and retrieval systems (AS/RS) and automatic guided vehicles have offered more options to meet the challenge in recent years. Automation, however, requires a major investment that not all companies can afford.
“Always, at the top of the list of concerns for customers is price,” says Adducci of Interlake Mecalux. “That said, educated customers and distributors are concerned about steel pricing and volatility and how that plays into pricing of finished product for material handling systems. “The next concern is technical systems and automation along with density of storage versus selectivity of warehouse SKUs. Technology and dynamic products solve the density/selectivity problem for customers, but at a higher cost than strictly selectivity concerns.”
The Interlake Mecalux Pallet Shuttle is a high-density, semi-automated pallet storage and retrieval system that makes it easier to load and unload goods. “This solution is excellent for deep lane storage and allows for the storage of different reference numbers per pallet shuttle and therefore a higher number of stored references,” Adducci says. “It also optimizes space by compacting pallets with different widths inside the lanes and by minimizing the height between levels. The pallet shuttle system is ideal for high-density, compact storage as well as cold storage.”
As cold storage space increases, food and beverage companies must reconsider storage density along with a host of other factors. There racking options available continue to expand.
Warehouse Consolidation Drives Storage Change
Coloma Frozen Foods Inc., a Benton Harbor, Mich.-based provider of frozen fruits, vegetables, juices, and juice concentrate, reconsidered its racking system when it built a new distribution center. The company outsourced or leased its frozen storage to four commercial facilities spread out over a 20-mile radius in southwest Michigan and it wanted to consolidate its frozen storage.
“Transferring product between four inter-company locations for production, frozen storage, and repacking was costly and inefficient,” says Brad Wendzel, company president. “One of the leased freezer facilities had aged beyond its useful life, and much of the racking was too low, requiring inefficient pallet unstacking and restacking before shipping.”
The company built 90,000 square feet of new freezer space, including 75,000 square feet of racked freezer space in a centralized facility. Looking to maximize frozen storage efficiency and repacking capability, Wendzel turned to Southwest Docking and Handling, a Dowagiac, Mich.-based material handling and automated systems distributor.
Southwest Docking and Handling suggested drive-in rack to optimize cube utilization. With drive-in racking, forklifts access the rack from an aisle.
“They did not have any of that type of racking before,” says Jim Nowicki, president of Southwest Docking. Southwest Docking believed a drive-in rack would provide cost-effective, high-density storage capacity that requires fewer aisles than a selective rack, which allows direct access to every pallet in storage.
With drive-in racking, forklifts drive directly into the rack to allow storage of two or more pallets deep. But because forklifts drive directly into the rack, they tend to take more abuse than other rack structures. Wendzel was concerned that the light gauge, roll-formed rack he had previously reviewed would be prone to forklift damage and costly replacement.
As a solution, Southwest Docking and Handling recommended a bolted pallet rack with structural channel columns made by Stevens Point, Wis.-based Steel King Industries.
“We expect to save about $150,000 to $200,000 a year in reduced labor, management, transportation, energy, and maintenance costs using the drive-in rack at our campus facility,” says Wendzel. “Our growth potential is substantial, and we expect ROI in under two years.”
For more information
Cubic Designs, cubicdesigns.com
Interlake Mecalux, interlakemecalux.com
Orbis Corp., orbiscorporation.com
Spacesaver Corp., spacesaver.com
Steel King Industries, steelking.com
Storax America, storaxsolutions.com
viastore systems, viastore.com