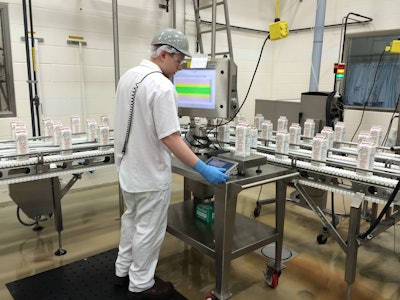
Supply chain managers have more software at their disposal today than ever before. Many options provide enterprise-wide solutions that can help improve the efficiency of operations, product quality and order accuracy. While new systems are designed to make management tasks easier, decision makers now face the challenge of trying to decide among a myriad of software choices. Software experts say it is important to consider the business’s long-term growth strategy when selecting new tools.
Cloud-based systems allow companies the benefit of complex capabilities without having to invest in on-premise systems. Companies that need to scale operations quickly oftentimes find cloud-based systems helpful in accommodating future growth. They can give access to more functions, even for companies that historically have not had the resources to invest in highly complex systems. Cloud-based systems can also allow a high degree of customization.
Enterprise resource planning (ERP) systems, data visualization software and enterprise quality hubs also create opportunities for companies to manage supply chain data more easily.
Growth brings challenges
As a company grows, it oftentimes encounters the need to integrate data from different software systems.
“The hard part has been merging data from disparate systems,” says Kevin Glynn, vice president and CIO at DSC Logistics, the Des Plains, Ill.-based supply chain services provider.
“Not everybody who delivers technology can be all things to everybody,” observes Charlie Piper, general manager at HarvestMark, the Redwood City, Calif.-based provider of food traceability and quality inspection solutions, a company recently acquired by Trimble. HarvestMark, for its part, has developed systems that can operate via the cloud and has programs for produce traceability, analytical insights and customer interaction. Piper is among those who believe cloud-based solutions make it easier for customers to access food information that is rising in demand in the supply chain.
“They (growers, manufacturers and retailers) are each getting involved at points of the supply chain they weren’t involved in previously as the food industry is being transformed by demands for greater transparency, quality and safety,” Piper says. “The most important demand for all parts of the supply chain is actionable information.”
Scalable system helps distributor add functions
Scalable systems help companies add more functionality without having to integrate data from different software systems.
Falsetto Fine Foods, an Ottawa, Canada-based wholesale food distributor to local stores and restaurants, invested in a scalable ERP solution several years ago that has allowed the growing company to manage its business in stages. The ERP solution from Queenston, Ontario-based Oneir Solutions manages inventory and accounting.
Falsetto Fine Foods recently upgraded its sales order guide module, a reference that sales reps use in making sales calls. This guide, which can be downloaded onto the screen of a sales rep’s laptop or tablet, enables the reps to inform customers of product data, including each customer’s order history.
More recently, the company added a supplier order guide, an automated purchasing module that makes purchasing decisions easier, faster and more accurate, says Silvana Falsetto, vice president and controller.
Chicken Express, the Benbrook, Texas-based restaurant chain, recently opened a 100,000-square-foot DC to service its 200 restaurant customers across Texas, Oklahoma, Louisiana, Georgia and Arkansas. AFS Technologies Inc.’s ERP and WMS software played a critical role in enabling Chicken Express’ expansion. The ability to work with radio frequency (RF) and voice devices at the DC allows the restaurant chain to increase productivity, improve order accuracy, and bolster inbound and outbound product velocity. In addition, the system’s modular architecture ensures the organization can scale capabilities as needed.
AFS Technologies, Inc., based in Phoenix, Ariz. recently enhanced its ERP software with new functionality designed to improve quality control. Two separate components, quality control and finite scheduling, complement the existing functionality within the ERP suite to deliver more comprehensive production capabilities.
The quality control solution provides real-time tracking using an Apple or Android smartphone, tablet or laptop. It enables organizations to implement and monitor measures to prevent contamination and to execute corrective actions quickly.
The finite scheduling enables real-time status on production lines, as well as potential delay alerts and instructions to the production staff. This can provide more efficient runs and minimal changeovers.
Other companies are finding it necessary to integrate different systems in order to use the more advanced capabilities, such as mobile enterprise functionality and graphically enhanced data visualization.
New features empower supply chain players
Nature’s Pride, a global fruits and vegetables distributor based in The Netherlands, recently deployed cloud-based visualization software to drive increased visibility across its supply chain from Qlik, a Reading, Pa.-based visual analytics provider.
To ensure each piece of produce is delivered at the peak level of freshness, the company needs to track the supply chain from grower to consumer. Prior to Qlik’s visualization software, the organization struggled to manage is growing amounts of data, often stored on disparate systems, and had difficulties presenting it in an understandable way.
Nature’s Pride worked with Qlik partner UNIT4, a Netherlands-based provider of enterprise applications, for the full implementation of QlikView. With the deployment, Nature’s Pride was able to streamline its processes to drive efficiency and reduce costs in the supply chain. Employees can now access the data they need with self-service analytics and can respond with visual insights at the point of decision.
Specific dashboards include:
- Advanced productivity dashboard. This delivers real-time insights into staffing, production speed, and whether employees are performing above or below the norm. The system displays the speed and number of stop minutes of each machine to provide insight into each production line.
- Commercial dashboard. This provides insights into certain product combinations and the total number of purchases broken out by product. This allows the organization to better meet customer needs and discover what products are most popular.
- Financial balance dashboard. This delivers insights into costs and revenues so Nature’s Pride can pin-point issues and make cost-saving decisions based on data.
“Everyone is aware of the value that data analysis can offer us and the simplicity with which the reports can be created,” says Roland Loykens, data specialist at Nature’s Pride. “Earlier, we had to pull the information from a multitude of sources, which was a laborious and time-consuming process. Now we have the information we need within a few clicks and the reports are beautiful. These provide a clear understanding of how we stand compared to the budget so we know if we should accelerate and if so where we need to do this.”
Whether or not a company finds it needs to integrate different software to add functionalities, new capabilities continue to emerge.
Real time data plays a key role
Real-time data monitoring plays an important role in improving the efficiency and quality control of manufacturing operations. Previously thought to be a components related to a single manufacturing operation, real-time data monitoring can integrate a company's entire supply chain. Cloud-based enterprise data hubs can centralize data collection into a single location and provide visibility of operations from the shop floor across the enterprise and into the supply chain.
The knowledge – or manufacturing intelligence – garnered from this data can be leveraged to improve quality control across a manufacturer’s facilities as well as its supplier plants.
“Real-time visibility of operations is especially important to quality control in f&b to ensure consumer safety,” says Mike Lyle, president and CEO of InfinityQS International, the Fairfax, Va.-based provider of manufacturing software powered by a statistical process control analysis engine. Within an f&b supply chain, there are a number of quality control precautions necessary to mitigate delivering a bad product, from metal shavings in frozen pizzas to peanuts in nut-free cookies.
An enterprise quality hub can identify and correct these issues in-process and prevent recalls, Lyle says.
Predictive analytics evolves
The data collected while monitoring the quality of ingredients and finished goods offer an often unknown benefit to manufacturers – predictive analytics. Predictive analytics is the application of advanced statistical analysis of structured and unstructured data sources to identify patterns and predict future events or outcomes. It can provide a look into the future and identify emerging patterns in the marketplace that can lead to effective and personalized customer engagement strategies.
Predictive analytics has taken the guesswork out of choosing settings for processing different cheeses for Minnetonka, Minn.-based Michael Foods, an InfinityQS customer. The data-based analyses attained through charting and real-time feedback from equipment has identified standardized settings that help plant managers reduce inconsistencies. This results in less waste and improved production efficiency.
Ben & Jerry’s, The Burlington, Vt.-based ice cream maker, another InfinityQS customer, uses predictive analytics to identify opportunities to improve run capability and raw material usage within its manufacturing facilities. Because high-quality ingredients are typically high-priced (up to $800 for a single barrel of swirl), the ability to finetune processes with more precise specification limits results in less raw material variation, increased cost savings and higher quality product for the consumer.
How accurately containers and packages are filled or ingredients are mixed can be important to a food processor, both in terms of quality and cost efficiency, Lyle says.
Predictive analytics provides similar efficiencies in distribution warehouses.
"We use predictive analysis for zoning SKUs in reserve storage and for slotting in the pick lines,” says Ken Heller, senior vice president of supply chain excellence at DSC Logistics. “Also, one of DSC’s Logistics centers uses predictive analytics for projecting volumes and pick percentages.”
F&b lags some other industries
Lyle says predictive analytics as well as cloud-based enterprise quality control systems are playing a bigger role in f&b manufacturing, but f&b is behind other industries. F&b manufacturers tend to be slower to adopt predictive analytics tools due to the high number of mergers and acquisitions which lead to standardization challenges. “However, if manufacturers take the time to implement enterprise-wide standardization and unify operations, they will more easily be able to ensure compliance, reduce scrap and reduce overfill with the cloud,” he says.
Cloud computing has provided a way to ensure “farm-to-fork” visibility of supply chain data, notes Lyle. Without cloud-based technology, it is difficult for most organizations to implement the traceability measures required under the Food Safety Modernization Act (FSMA). This would be hard to do without cloud-based technology. “Having supply-chain-wide traceability is crucial for optimizing and preventing recalls,” he says.
Cloud-based solutions only account for a minority of f&b manufacturers to date, Lyle says, but the number is growing.
Some companies still have concerns about the security and the availability of cloud-based systems. The three concerns Lyle hears in order of importance are 1) availability, 2) security and 3) cost. “A properly designed system can address and overcome these concerns,” he says. “If a company takes the necessary steps to create an environment that complies with industry regulations, ensures business continuity and disaster recovery, and employs high-level security precautions, you can provide a very stable, reliable system.”
A lettuce grower that oversees 16 food processing sites in two different parts of the country throughout the year has been able to take advantage of the cloud model, Lyle says. In one weekend, and without an internal IT team, they moved their entire facility – machines, lines and equipment – from one place to another without missing a beat. With the cloud, they have eliminated the time and costs of installation and implementation, and found an efficient way to coordinate quality at all their facilities.
More capabilities emerge
HarvestMark, the Redwood City, Calif.-based provider of food traceability and quality inspection solutions, has an interactive application that allows companies to engage directly with customers. General Manager Charlie Piper says a major U.S. retailer is using HarvestMark QR codes to share details about particular products and buying practices, and suggest recipes and complementary products. “The engagement with the consumer, if it’s not focused, it’s not effective,” he says. The program also gives consumers the chance to provide input on their produce.
In addition to its supply chain and traceability platform, HarvestMark offers a mobile analytics application. It guides quality inspections, provides analytics for improved buying and gross margin, and creates visibility in real time with automated performance reports and supplier notifications.
“One other significant technology I personally follow extremely closely: 3D printing,” says DSC Logistics’ Kevin Glynn. “The speed of development of this and its effect on supply chains will be more disruptive than all the others combined.”
Software specialists continue to improve ways for f&b supply chain managers to access and visualize data within their own operations and throughout their entire supply chains.
For more information:
AFS Technologies Inc., 602-522-8282, afsi.com
DSC Logistics, 847-635-4952, dsclogistics.com
HarvestMark, 866-768-7878, harvestmark.com
InfinityQS International, 800-772-7978, infinityqs.com
Oneir Solutions, 416-322-3580, oneirsolutions.com
Qlik, 866-616-4960, qlik.com
Trimble, 800-874-6253, trimble.com
UNIT4, 31 (0) 184-44-44-45, unit4.com