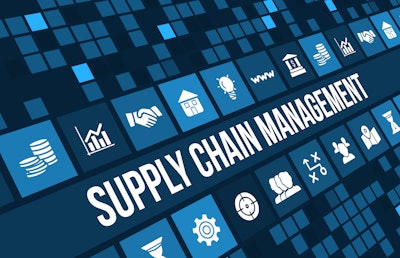
Now more than ever, food manufacturers must prioritize operational efficiency, productivity and cost reduction. With manufacturers already feeling squeezed with the costs of supplies, labor and equipment creeping ever higher, companies must take urgent steps to minimize downtime, overhead and waste in their operations.
Equipment maintenance plays a crucial role in production efficiency, and neglect or procrastination directly impacts output, on-time delivery, product quality, food safety, worker safety and machine longevity. Under increased pressure to ramp up production, these issues are exacerbated when equipment is pushed beyond its intended parameters and design capabilities for speed, pressure or temperature, for example.
The problem is that many manufacturers view maintenance as a necessary evil and, therefore, try to do it as little as possible to minimize downtime. But instead of saving time and money, this strategy inevitably drives up costs and inefficiency as minor equipment issues quickly balloon into major projects, unplanned replacement, or even prompt recall risk.
Why predictive over preventive for 2025
Preventive maintenance can help reduce the risk of unplanned downtime, but too often, it means the work is performed before it’s actually needed. A calendar-driven schedule can result in unnecessary expense, downtime, and safety risks for maintenance crews.
Instead, predictive maintenance has proven to be a better way forward in 2025. By using operational data to forecast equipment needs and failures, predictive maintenance ensures maximum efficiency, machine reliability, on-time production, consistent quality and cost savings while minimizing downtime and maintenance requirements.
In fact, a well-executed predictive maintenance plan can reduce unplanned downtime by as much as 40% and cut overall maintenance costs by 25%. And that’s just scratching the surface—it also can lower downtime costs by up to 40%, improving both technician efficiency and customer satisfaction.
7 steps to launch a predictive maintenance plan
Getting started with a predictive maintenance program requires some planning and pre-analysis, but the time spent preparing a strategy is well worth it. Here’s a step-by-step guide for a smooth launch.
1) Assess current maintenance practices. Review your existing maintenance program—not just what you’re doing and how often but also how effective it is in reducing failures and inefficiencies. Is the slicing equipment actually maintaining tolerances or having fewer off-spec incidents with the current scheme? Where might predictive insights be helpful in optimizing the schedule?
2) Set clear objectives. Establish clear and measurable KPI targets for the program. Consider metrics like lowering unplanned downtime, predicting and preventing equipment failures, or even reducing spillage or energy consumption, and ensure these goals align with overall business objectives. The goal is to find the right balance between performing maintenance often enough but not too often.
3) Gather and analyze equipment data. Predicting future needs requires looking at historical data—there’s likely a pattern connecting equipment efficiency decline with maintenance needs. Start by gathering detailed data on equipment performance and failures, including maintenance records and operational data. Is inconsistent oven temperature a concern? How often do the conveyors require emergency cleaning? This data can help form the foundation of your predictive model.
4) Implement condition-based monitoring. Just like a surgeon would monitor a patient’s vital signs during a procedure, you’ll want to monitor your equipment’s vital signs during operation. With monitoring technologies like ultrasonic and thermal infrared scanning and other Industrial Internet of Things (IIoT) solutions, maintenance teams can continuously track equipment health and even get alerts when an out-of-tolerance condition is impending so they can plan for service accordingly.
5) Develop a predictive maintenance schedule. Going predictive doesn’t mean scheduling goes completely out the window. Instead, it’s about optimizing the schedule for maximum efficiency and efficacy.
Using the data and insights obtained from historical analysis and monitoring, maintenance teams can forecast needs and schedule maintenance activities proactively. For example, you might find that the filling scale would benefit from recalibration every 30,000 packages to maintain consistency, or a conveyor needs realignment every 2,000 hours to avoid jams. Here’s where technology can help: Computerized maintenance management systems (CMMS) can track performance, streamline maintenance tasks, and help keep things running smoothly.
6) Train your team. This new approach requires specialized training to bring your maintenance and production staff up to speed. They’ll need to learn how to interpret the data insights so they can effectively respond to predictive needs and maintain equipment reliability.
As part of the process, set some protocol for alerts (who gets them and when), what next steps are expected and in what timeframe. While you’re at it, review and optimize the work instructions for each maintenance task so that they’re clear, efficient and safe.
7) Monitor, evaluate and adjust. Implementing predictive maintenance isn’t a one-and-done project. It requires regular assessment to compare actual outcomes against your objectives. After all, equipment needs will change with age and utilization. Teams may need to adjust strategies, schedules and techniques to fine-tune the program and optimize equipment performance, but it’s well worth it.
Predictive maintenance allows food manufacturers to hit the sweet spot of addressing equipment needs just-in-time without unnecessary downtime while lowering the risk of unexpected failure. In today’s competitive market, it’s essential for protecting equipment investments and ensuring longevity of some of your most critical assets.
By creating a structured plan and a schedule—and sticking to it—predictive maintenance can keep your equipment operating at peak performance, ensuring smooth operations and long-term success while reducing costs, safety risks and quality issues.