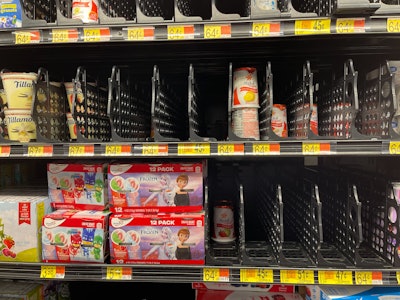
The world of retail is an interwoven industry that encompasses businesses, consumers and transport services to ensure that products are efficiently moved from manufacturers to stores and eventually into the hands of customers. Inventory management has always been key in such a large supply chain, but the food and beverage and cold chain sectors are starting to suffer more and more from inventory disparities due to miscounts or shipping errors. These mistakes lead to stockouts and overages – both of which are costly for retailers and impactful on their relationship with consumers. Tech freight management is a solution that can help stop these losses and increase retailer efficiency.
Inventory discrepancies
Inventory discrepancies happen often in retail, especially in industries or sectors that deal with perishable products. Miscounts and shipping errors are the main issues for most retailers, which ultimately lead to major financial losses that companies must pivot to recoup from.
Stockouts are probably the most damaging to retailers. When customers visit a store and can’t find the products they need, it results to $1.2 trillion in losses for retailers annually. Overages, on the other hand, lead to heavy discounts and spoilage resulting in $562 billion in losses in 2023.
Ways to minimize discrepancies
Many retailers are moving to supply chain technologies to avoid inventory mishaps. In 2023, 97% of companies invested in these technologies and 80% saw revenue growth within the first 12 months of investment. This often include:
- Automation systems. Automated systems can help count and track inventory. Artificial intelligence (AI) technology is able to assist with tasks like picking and packing to ensure precision in order fulfillment. This aids in avoiding or correcting human error.
- Real-time data tracking. Using real-time tracking systems allow retailers to closely monitor inventory levels and movements in real-time. This helps to identify oddities as soon as they happen.
- Advanced analytics. Using advanced analytics, retailers can predict demand more accurately and adjust inventory as needed. This reduces the chance of both stockouts and overages.
- Blockchain technology. Blockchain has the ability to increase transparency and traceability in the supply chain by constituting a system that tracks and verifies a product’s entire journey from start to finish.
Accountability measures by big box retailers
Maintaining accountability at every level of the supply chain is crucial to managing inventory effectively.:
- Vendor scorecards. Vendor scorecards are used to measure vendor performance and can track delivery, order accuracy and product quality.
- Contractual agreements. Retailers include specific performance requirements in their contracts with vendors. These agreements spell out the consequences of missing delivery times or order accuracy standards, so vendors are motivated to meet the terms.
- Collaboration and communication. Communication between retailers and vendors is key. Collaborative platforms and regular meetings help both parties stay in sync and address issues quickly.
- Technology integration. By integrating with their vendors’ systems, retailers can get visibility into the supply chain. This integration allows for real-time data sharing so you can spot and fix any issues.
Enhance supply chain efficiency and security with vendor accountability
Big box retailers’ efforts to hold vendors accountable have had a big impact on the industry. By focusing on accuracy and efficiency they’ve reduced inventory discrepancies and overall supply chain performance. Supply chain disruptions can cost up to 62% but a streamlined process that provides efficient management and holds retailers accountable can minimize the risks. Retailers who invest in supply chain tech and hold their vendors accountable see higher revenue and customer satisfaction.
Plus, technology has given us better visibility and traceability in the supply chain. This helps reduce discrepancies and prevents issues like cargo theft. According to CargoNet, $130 million worth of goods were stolen in 2023, most near warehouses, distribution centers and unsecured parking lots. By implementing advanced tracking and security measures retailers can protect their cargo and reduce theft incidents.
Keys to retail supply chain success in 2024
By investing in automation, real-time data tracking, advanced analytics and blockchain retailers can reduce inventory discrepancies and overall supply chain performance.
Big box retailers are showing the way by holding vendors accountable with scorecards, contractual agreements, collaboration and technology integration. These have resulted in reduced financial loss, higher customer satisfaction and supply chain visibility.
With retail sales expected to grow 2.5-3.5% in 2024 to $5.25 trillion, inventory management has never been more critical. By using tech and holding vendors accountable retailers can be ready for their customers and stay ahead of the competition.