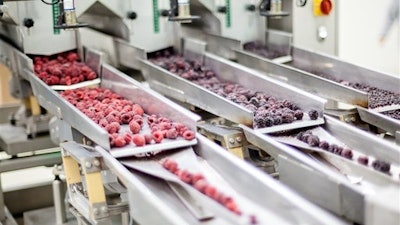
Following its successful launch last year by TOMRA Sorting Recycling, TOMRA Insight is now also being made available to TOMRA Food and Compac, part of the TOMRA Food family.
TOMRA Insight turns sorting and grading machines into connected devices that generate valuable process data. This data is stored securely in the cloud, converted into actionable information, and accessible from anywhere via a web portal for desktop and mobile devices. TOMRA Insight’s data-gathering helps processors in near real-time and retrospect. Because product quality is measured continuously, machine operators are empowered to make prompt and optimal adjustments to machine settings in response to product quality changes on the line. And, because TOMRA Insight provides previously inaccessible deep-dive data, customers are now empowered to make operational and business decisions based on more complete information. TOMRA’s engineers help customers analyze critical data every month as part of the TOMRA Insight subscription service. Accurate and timely comparison is now possible between multiple sites, shifts, batches and seasons.
Felix Flemming, Vice President and Head of Digital at TOMRA Sorting, commented: “By capturing and using valuable data, TOMRA Insight is transforming sorting from an operational process into a strategic management tool. And, this tool is constantly becoming more powerful as we continuously develop it in response to customers’ needs and priorities. New functionalities and features are released every three weeks – a routine during which TOMRA works closely with customers in pursuit of shared objectives.”
Thanks to the performance metrics gathered by TOMRA Insight, processors can benefit in many ways. Downtime is reduced by monitoring machine health and performance to support predictive and condition-based maintenance. Throughput is maximized by evaluating variations and optimizing sorting equipment accordingly. Efficiency is improved by identifying gaps in production and analyzing potential root causes. Sorting to target quality is enhanced by being able to make decisions based on accurate product composition data. And, operations are simplified through easier spare parts ordering and flexible access to data and documentation.