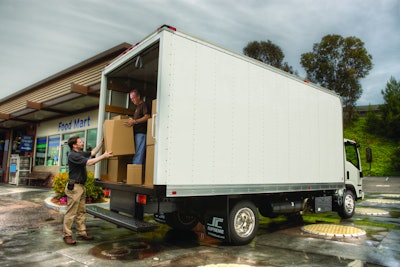
STATUS REPORT: TECHNOLOGY
TMS Update
Most operations executives in the industry would agree that an efficiently run business is also a business that is operating sustainably—namely, operating without waste and focused on reducing petroleum consumption. Transportation management systems (TMS) have evolved to the point of offering users a wide range of functionality yielding numerous opportunities to increase operating efficiencies, contain costs, and achieve sustainability goals.
No Idling Zone
Although conventional wisdom suggests that if you are operating your transportation network efficiently, you are probably operating sustainably as well, Cyndi Brandt cautions with a caveat to that belief. “You would be surprised to learn that it is not truly a one-to-one correlation,” says Brandt, vice president of marketing for Baltimore-based Roadnet Technologies. “Although you might reduce fleet miles—which is what our software does—you can completely erase any of those savings when you park your truck and leave it running. Sustainability ultimately comes down to reducing your petroleum consumption, which in turn reduces your carbon footprint. What is an eye-opener to many is the fact that idling is a very expensive endeavor, and we have found that truck drivers typically spend anywhere from 20 percent to 60 percent of their day idling.”
Some drivers believe they are operating their trucks efficiently because of the idling governors they have in place. “Governors are great because they will turn off your truck after it has remained idling for 5 minutes,” Brandt explains. “But what if you have a firmware updated to your engine and it is no longer working. We actually found that happening with several of our customers, who were surprised to discover they were really idling at tremendous levels every day.”
Most idling occurs during deliveries and when trucks are being loaded. “We have a few customers who couldn’t understand why their fuel consumption was so high,” continues Brandt. When Roadnet investigated, it discovered that employees loading the trucks and yard jockeys were starting the trucks at night, not turning them off until first thing the next morning. “It turned out to be a huge expenditure for those customers. The point I am making is you need to watch your idling habits—and it’s not just about making deliveries. It’s about monitoring your trucks when they are in the yard as well.”
Understanding these numerous cost-gobbling challenges facing transportation companies, Roadnet last June launched Roadnet Telematics, a box that floats into the engine control module. Advanced capabilities have been added to the product since its launch, notes Brandt, who adds that the company already has over 3,000 of these units in the field. “It has the ability to know when you are not moving when the ignition is on, and after a prescribed time period—our default is 300 seconds—it sends an alert through what we call an idling exception to advise someone is idling when they shouldn’t be.”
This information is critical in helping drivers develop habits that will enable them to perform more efficiently. When drivers are alerted to the number of idling incidents they were responsible for over a period of time, they can consciously stop bad behavior, Brandt says. An audible alert is also available that alerts a driver on the spot that he is idling and that his manager is aware of it. “We can even create a green scorecard based on mileage and the amount of time a driver idled relative to the number of stops and the number of total miles a driver drives every day.”
Brandt reports that a best-in-class driver with no power-take-offs should be able to achieve as low as 3 percent idling time throughout his total route time. “The thing to remember when thinking sustainably is that an hour of idling uses a gallon of gas, which is approximately 22.2 pounds of carbon that shoots out into the atmosphere.”
Safety Telematics
Another function of Roadnet Telematics is its ability to inform how a truck might have been hit in a parking lot. “In conjunction with our enhanced GPS, our accelerometer can report such incidents to determine if the truck was moving when such an accident happened or if it hit a pole—just by looking at the accelerometer data,” Brandt says.
The accelerometer allows companies to measure safety and can report how fast drivers are driving and even what the tilt of a truck is as it travels around a curve. It also reports on incidents of harsh braking and rapid acceleration, each of which consumes additional fuel. “So this unit delivers more and better information relating to sustainability to help you better protect your expensive equipment. Just remember that every time you have to replace your brake pads, you are using up a petroleum-based product.”
Another benefit to the telematics unit is that it monitors speeding incidents. “Speeding is really a sustainability killer,” says Brandt. “For every mile an hour over 50 mph, you increase your fuel consumption by 1.5 percent and you increase the drag on your vehicle, which makes the engine work harder than it needs to work. Speeding also increases your maintenance costs for things like gears, bearings, suspension, clutches, and drive trains—which all wear much faster at higher speeds. You could actually increase your annual costs by anywhere from 40 percent to 80 percent as a result of speeding.” She reports that driving 60 mph instead of 50 mph increases your costs by 38 percent; and if drivers consistently drive at 70 mph rather than 50 mph, costs increase by 80 percent.
Intelligent Designs
Sustainability as it relates to TMS solutions begins with an intelligent and efficient network design, notes Matt Menner, senior vice president of sales and alliances for Transplace in Dallas. “The process begins with the application of optimization-based routines and algorithms that generate the best possible routing solution taking into consideration transportation costs, customer service levels, modal options, capacity availability and increasingly these days the green coefficient of those designs by combining multiple LTLs into truckloads and finding loads for empty backhauls. The result is the development of a sustainability score.”
For instance, if a shipper wants to know what its carbon footprint will be for a number of different scenarios, Transplace can present each of those in terms of cost, service level, and environmental impact. “So the process begins with the design and then the design is loaded into our TMS solution which captures the consumption of services and the green coefficient of carriers to help align them with SmartWay’s scorecard,” explains Menner. “Every SmartWay carrier has a fleet model score, which we also take into consideration in the decision-making process of whether we would use one carrier over another during bid lane selection and assignment.”
One of the fundamental requirements in achieving higher sustainability performance is to use SmartWay carriers who have made intelligent capital investments in their rolling stock to operate in an efficient and sustainable manner, Menner says. He sees many companies dealing with the challenge of how to go about identifying a set of pragmatic programs for a financially acceptable outcome that is good for the company as well as for the environment. “Efficiency equates to sustainable practices which, in turn, equals a greener coefficient for the shipper. Consequently, one of the core philosophies for Transplace is aggressively supporting the SmartWay initiative.”
Shippers prefer aligning themselves with carriers who have made the right capital investments such as current-specification tractors with the appropriate engines that meet current emissions requirements. “These carriers have also gone to the expense of using single-wide-based tires, skirtings on tractors and trailers to increase the aerodynamic coefficient of the vehicle, and APUs in tractor cabs,” explains Menner.
All of these investments pay off in terms of operating efficiencies, cost savings, and sustainability goals. “If I am a shipper, I won’t want to use a less-efficient carrier getting an average of five miles per gallon when fuel is at $5 a gallon and I am paying a fuel surcharge that might be the equivalent of 40 percent of the cost of moving my freight,” says Menner. “I will want to do more work with carriers that have deployed the technologies and practices that net them six miles per gallon—which will directly impact my fuel surcharge exposure and ultimately my fuel expense.”
He says the financial aspect involved is probably the single leading quantifiable indicator in terms of efficiencies and is the reason shippers who are dollars-and-cents minded are embracing these programs.
Smarter, Greener Routes
Brandt at Roadnet explains that there are two methods of optimizing routes: standard routing and dynamic routing. Standard routing is used extensively in the food and beverage industry because of the exceptional level of customer service it delivers, including a consistent driver and a consistent delivery day and time.
Roadnet’s Territory Planner product considers all of the customers you deliver to and creates territories, with one truck covering each territory. It examines how much you deliver, the capacity of the vehicle, and the time window commitments in order to create the most optimized standard route. “What makes a standard route inefficient is the fact that not everyone always orders,” Brandt says. “So if the driver has 10 stops and only five people order, it is not very efficient from a mileage standpoint and from the standpoint of your vehicle’s capacity. Roadnet helps balance out when one route has 125 percent capacity opposed to another route with only 50 percent capacity.”
But this standard routing method also creates inefficiencies relative to mileage, Brandt explains. “With fuel continuing to top over $4 a gallon, maybe you need to make some changes so it’s not just Joe who delivers to Paula’s Deli and who has a great relationship with Paula. Maybe it needs to be Joe, Jack and John delivering to the deli and developing rapport with Paula. If you want to become more efficient and more green by reducing miles, you might want to look at another routing optimization method such as dynamic routing.”
Dynamic routing considers up to 200 different rules—such as who you need to deliver to tomorrow, what time are they open and what time do they close, and what is their preferred time windows for deliveries. “We then develop the best route based on these rules and the program creates density because the more dense the routes are, the more efficient they will be,” Brandt says. “But the cost of doing it this way could be that Joe delivers one day, Jack the next day, and John the next.”
Brandt reports that Roadnet is seeing more of its traditional standard routing customers embrace the concept of dynamic routing. “The thing to remember is that you don’t have to go to full dynamic right away. You can begin by starting with zone dynamics first, creating cells and dynamically route within the cells.”
Delivering The SmartWay
FreightMaster is Next Generation Logistics’ TMS product allowing users to manage and maintain their carriers participating in the SmartWay Transport Partnership administered by the EPA. “The system allows users to see which carriers are SmartWay participants and which are not,” says John Riske, vice president of business development for the Inverness, IL-based company. “Our customers can determine whether they want to choose a SmartWay carrier versus one that is not as they undertake the process of selecting a carrier for a particular route.”
Although not every carrier participates in SmartWay, those who do are leveraging sustainable results as they reduce miles to gain marketing advantages, Riske says. “As a SmartWay partner, you should be looking at your role in the sustainable world relative to carbon emissions because it impacts you and your customers. As a carrier and a shipper, you can leverage your marketing efforts around reducing your carbon footprint.”
Riske adds that shippers more than ever before are asking that their carriers become a SmartWay partner so they can manage, track, and report their sustainability performance. Many companies are looking for advance reporting and KPI reports relative to a carrier’s carbon index. “FreightMaster allows users to analyze and plan their orders in terms of building like orders and trying to consolidate loads to reduce their carbon footprint. The system allows them to maximize capacity and produces the most efficient route with the least-cost miles. It does this by taking multiple LTL shipments and combines them with multi-stop loads to reduce miles in your network while reducing your costs.”
Some carriers were reluctant from the beginning to become SmartWay partners because they were not sure about possible governmental regulations, Riske says. “From the start, not every carrier was compliant with this program; but carriers will eventually have to comply or risk losing business because many more shippers now are requiring their carriers to become a SmartWay partner and have programs in place to reduce emissions overall.” Shippers are even demanding that their carriers have newer and more efficient equipment that complies with SmartWay emissions stipulations.
The ability to track miles to determine the percentage of SmartWay carriers versus non-SmartWay carriers a shipper is using provides a conceptual snapshot of the shipper’s overall achievements relative to reducing emissions. “Being able to track and report this data enlightens many people in the organization, even at the C-level,” notes Riske. “Tracking their miles run on an annual basis urges them to optimize routes more frequently. FreightMaster allows them to work faster and better so they can spend more time managing carriers and not as much time in the day-to-day requirements of guessing who they should use or how to put routes together in the most efficient way possible.”
Shippers are demanding these systems that enable them to be able to properly manage, monitor, and track KPIs. TMS implementation is projected to increase substantially over the next several years, says Riske, adding that TMS solutions like FreightMaster will be the norm in several years. “With the economy in the state it’s in and carriers concerned about additional regulations coming down, these solutions are not at the forefront of their thinking, although inquiries are in the increase. But without leveraging technology like TMS, you don’t really know how many miles you have traveled—let alone if you optimally routed those shipments to minimize miles.”