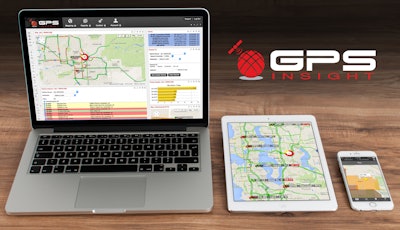
Connections and connectivity now seem to be at the center of everything we do. By connecting people to equipment to achieve intelligence, telematics can help food and beverage organizations keep dibs on the location, movement, status, behavior and performance of vehicles within their fleets.
Telematics devices—which can range from video cameras to electronic logging devices (ELDs) to temperature sensors to GPS—wirelessly connect to a vehicle’s engine control module, then collect, store, and transmit data to a mobile computer or application in the cab and/or office. The kinds of data these devices manage and transmit depend on the intended application of the device, but the data transmissions provide actionable intelligence to a fleet manager or operators who can modify processes or update routes based on fact-based (often real-time) analytics.
This data can be used to achieve any number of objectives, including the betterment of:
- Decision-making via asset tracking and visibility.
- Fleet management and maintenance.
- Vehicle, driver and cargo safety.
- Regulatory compliance.
Better Decision-Making via Asset Tracking and Visibility
Companies frequently say their employees are their best assets, yet fleet managers are frequently managing their workforce remotely as employees scatter in their trucks at the start of each shift. Telematics can help track not only where their people are, but also their trucks. They can monitor speeds, miles per gallon, fuel taxes, miles by state and myriad other data points as well.
Another vital asset that food and beverage companies must monitor is trailers, especially if those trailers are part of a cold chain, which must remain unbroken during hand-off points if the integrity of the food is to be protected. With telematics, according to Sue Rutherford, vice president of marketing at ORBCOMM, “Trailers can report their position and speed, load and tethered status, as well as temperature, fuel levels and reefer operational status. Trailer telematics enable users to remotely monitor cargo area temperature and receive alarms if values deviate from the specified range. Comprehensive, two-way trailer telematics solutions also enable you to remotely set reefer temperature, or turn a unit on or off.”
Fleet Management and Maintenance
Preventive maintenance, or proactively scheduling maintenance at specified mileage intervals, is an effective way to ensure continuous and consistent vehicle health by averting breakdowns and maximizing uptime. Rather than inspecting a vehicle every quarter, for instance, a fleet manager can schedule it by the mile, which is a more accurate representation of when the vehicle requires service. Not only does it same time, but also resources and money as unnecessary maintenance can be prolonged. An under-utilitzed vehicle, for example, does not need as many inspections as a fully utilized vehicle. Because telematics can integrate vehicle data with other systems, like preventive maintenance programs, as vehicles reach certain mileage or hourly thresholds, the program can trigger alerts to return the vehicle to the terminal for service or inspection.
“Management can schedule all maintenance for the fleet within software, receive reminders for each service and view maintenance reports. Users have the ability to respond quickly to customer delivery inquiries, service more customers per day, confirm job completion and bill more accurately.” Ryan Driscoll, marketing director at GPS Insight, elaborates, “If you have a list of orders and determine that 25 percent of the remaining work for the day could be reallocated to different drivers based on the number of drivers that fall behind and are ahead, it helps maximize efficiency and therefore profit on a day-to-day basis.”
Norm Ellis, president of EROAD, confirms that telematics also allow fleet managers and operators to better manage the number of vehicles they have in a fleet, thereby avoiding the under- or over-utilized vehicle conundrum. “If you’re operating a 100-truck fleet, how efficient is it? How many hours, per truck, are you running daily, weekly and monthly? The tools and data different telematics providers supply make it easier to understand how efficient the fleet really is. Are trucks being used only 20 or 30 percent of the time? Maybe there are too many assets deployed in a certain area.” If so, telematics can help determine how to most efficiently divert these extra vehicles and allocate them to an area that can deploy them more effectively, which leads to more responsible spending.
Vehicle, Driver and Safety
Vehicle and driver safety is of utmost importance in food and beverage fleet operations. Telematics can not only reduce risk to vehicle and driver safety, but also decrease liability, improve training, and even exonerate innocent drivers if and when an accident does occur. Because many telematics devices incorporate accelerometers, they can sense, and report on, rapid acceleration and deceleration, as well as hard braking and turns. When fleet managers have this data in hand, they are able to tailor their training programs to better avoid these risky driver behaviors—whether it be through a reward and punishment system, rerouting drivers around risky areas or just calling new recruits’ attention to risky scenarios.
Because video telematics integrates data from both telematics sensors and video data, it can deliver critical insights that can be used in training. Video telematics can help drivers avoid accidents by generating statistics and reports to identify risks within the fleet, so training time and resources can be better allocated. In addition, this data can help fleet managers establish benchmarks and safety goals.
“Members of the food and beverage industry have many things to protect, including their drivers, their cargo, and of course, their brand. Every person behind the wheel is a brand ambassador that can add to—or detract from—a brand’s image. Each vehicle in your fleet, too, is a brand asset and keeping the vehicle free from collision damage helps you put your best foot forward,” explains Kara Kerker, executive vice president and chief marketing officer at Lytx Inc.
Furthermore, Ellis says that most driving accidents are caused by not the commercial driver, but the motoring public. However, the burden of proof often lies on the commercial truck driver who is operating the larger, heavier vehicle on the road. Video telematics can assist in exonerating the driver because, if the other driver runs a red light, the video provides a record of all of the details that led to the accident, thus decreasing liability. Kerker concurs, “Safety telematics aims to tell you what happened, or even where or when it happened based upon GPS data, but telematics can’t tell you why it happened. Video telematics, on the other hand, delivers the clarity and certainty of video that answers the question of why, along with the analytic insights to help prevent the event from happening again.”
According to Rutherford, in order to protect the cargo vehicles are transporting from the point of origin to destination, telematics can also:
• Detect theft and ensure cargo is secure by monitoring door sensors.
• Keep drivers safe in high-risk areas with the use of reliable, two-way communications, panic buttons and geofences.
• Help prevent hijacking by detecting the use of GPS and cellular technology signal jammers.
• Track stolen vehicles using GPS location information.
Regulatory Compliance
Because the food and beverage regulations require more tracking than most other industries, telematics are a boon especially for food and beverage fleets. With the advent of the electronic logging device (ELD) mandate, however, is the easing of compliance with hours of service regulations, which stipulate when and how long drivers can be active on the road. The ELD mandate required by December 2017 is considered telematics technology based on the fact that it digitally communicates driver and vehicle information, as well as location data to verify hours-of-service and driver vehicle inspection reporting, thus eliminating paper logs, which can be inaccurate and time-consuming. Because ELDs monitor and record many data points, they facilitate the fulfillment of many food and beverage-related regulations as digital reports can be culled much more rapidly than manual audits.
Temperature sensors and monitors are also telematics devices because they transmit and record information about the temperature inside the reefer trailer, which can help prevent spoilage and verify that food is safe. “By installing a temperature sensor in the trailer, management can see temperatures in real time and react quickly to avoid costs associated with food spoilage,” according to Driscoll. “Reports can also be pulled to investigate the temperature of a trailer at a certain time, day or customer site in the case of any customer complaints.”
Rutherford opines, “With liability at stake, data integrity, collection, storage and delivery are key to compliance.”
The Future of Telematics
Raymond Zujus, director of business development for food and beverage at Telogis, believes, “Telematics is just the beginning, but connecting and optimizing vehicles is really where the true savings lie. Utilizing analytics to mine for insights that can help identify trends, predict behavior and empower decision-makers. What’s more important is taking that data and turning it into real value by analyzing it and using the intelligence you derive to gain a desired business outcome.”