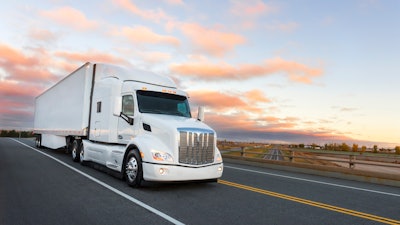
New technologies and improvements allow shippers, carriers and receivers to tackle a host of ongoing challenges in the industry.
Here’s how experts believe that trends in track-and-trace technology will impact the industry in years to come.
Real-time updates
One trend during recent years is the increasing demand for live updates on shipments during transit, says Ian Hess, senior vice president of brokerage operations for the Southeasts for Atlanta-based Nolan Transportation Group.
“Everyone wants real-time visibility on what’s going on with their shipments, where exactly they’ve been picked up and where exactly they are going,” he says. “We’re trying to use every technology available to us to give that real-time visibility to our customers, whether it’s through FourKites or ELD (electronic logging devices) integration or whatever we can do for customers.”
That’s why customers want real-time updates, and expect to receive them every 1-2 hours. ELDs allow carriers to not be on the phone with their dispatcher to get an update.
Meanwhile, other drivers simply want an alert when their trailer temperature rises above a certain threshold, says Zack Gibbs, senior product manager at Trimble Transportation, Minnetonka, Minn.
“There are people saying, ‘If it goes five degrees below that 40-degree threshold for this particular product line, I want an alert,’” he says. “They want a notification to be sent via email or text message.”
Real-time notification frequency
Frequency of real-time notifications is often based on cost, say David Cahn, director of global marketing at Elemica, Wayne, Pa.
“We see the need for real-time information varies because there’s a cost to it,” he says. “Traditionally, track and trace was, ‘I picked up the order, I delivered the order, I got the order unloaded and it got put away.’ Now, we have GPS technology, any-time information, where it is at any point in time. But, to get those GPS signals and actually get it onto your control tower, that costs money.”
Read Next: Food Logistics Honors Top Software & Tech Providers of 2019
For many, it’s not so much about the frequency of notifications as it is about building trust with the client, says Cahn.
“A lot of 3PLs are doing it for their customers, and are really trying to drive better supply chain relationships, so you can you trust your suppliers,” Cahn says. “From a supply network [perspective], you get to forge a better working relationship with the supplier. Updating your shipment status in real time can really benefit the relationship, in terms of product quality, reliability and online delivery performance.”
Extended shelf life
On-time delivery is important to help maintain the shelf life of perishable products. More often, clients expect more accountability when it comes to delivery time, and technology is increasingly playing a role in that.
“One of the things that has definitely become a core standard with technology and track and trace is, shippers and receivers are able to track shipments and whether it’s on time. They’re really holding their carriers accountable to make these on-time deliveries and on-time pickups,” Hess says. “I think one of the most standard numbers I’m seeing across the industry is, shippers and receivers, mainly receivers, are holding their carriers to have 98% on-time delivery, and they’re able to track that accurately. If they’re not compliant to their percent on time, they’re not going to invite them to the next bid for the next RFQ (request for quotation). That’s just valuable shelf life, especially in the food industry.”
To help ensure on-time shipments, many grocers request team drivers ship the load.
“Especially with the new ELD laws, something that used to be a day transit or a two-day transit isn’t anymore,” adds Hess. “So, we’re seeing a lot more requests for team drivers to hold to those transit times and make sure they get the product there and on the shelf as soon as possible.”
Tracking potential product recalls
Whether it’s food, pharmaceuticals or retail items, product recalls add a layer of complexity to the supply chain.
But, when it comes to recalling perishable items, technology can track down the recalled product to the exact farm plot it originated from.
“If there’s a big problem, people want to know exactly where this product came from,” Hess says.
Demand is also increasing for multi-tier track and trace, which tracks a recalled product anywhere along the supply chain.
“Can I go multi-tier, forward and backward with track and trace? I want to know, if this lot was bad, tell me all of the ingredients that went into this lot,” Cahn says. “And, then on the other case, show me all shipments that contain this lot number. I need it to go more than one stage down in the supply chain. I need to have multi-tier visibility. As a manufacturer, I sell it to a distributor, that distributor then sells it to a retailer and that retailer sells it to a consumer. Most of them are getting better at that multi-tier track and trace.”
When tracking perishable product recalls, the industry has a better handle on temperature, humidity and expiration dates, he says
Regulatory impact on track and trace
Strict regulations, such as the Food Safety Modernization Act (FSMA), has made real-time notifications more of a reality, Gibbs says.
“The data has become a lot more accessible because of the ELD mandate that’s finally taken full effect,” he says. “In the carrier ecosystem, you have a lot more accessibility to data than we’ve ever had before.”
While new mandates have brought positive change to the industry overall, a lack of standards remains a challenge, says Rick Zaffarano, vice president of consumer products solutions at Transportation Insight, Hickory, N.C.
“Food shippers have two pressures that have been heightened in recent years—food safety and must-deliver-by demands by consignees. Let’s take the mandate for electronic logs, for example. Everyone must have them, but there are many providers of that technology. New trailers have all the technology available to monitor location, temperature and even when the doors of the trailer are open. The challenge is universal compliance to one platform that is easy to integrate with,” adds Zaffarano.
Widespread technology adoption and integration
Adoption of software that provides real-time notification capabilities has been robust over the past few years, Gibbs says.
“It’s gotten a lot easier for the shippers in particular because most shippers have adopted TMS (transportation management system) technologies,” he says. “Because TMS technologies have been widely adopted, whether you’re a carrier, a shipper or a 3PL, there are a ton of different TMS providers out there that have offerings depending on who you are and what you do.”
But, not every player in the logistics supply chain has the most advanced, integrated technologies, which can make real-time updates a challenge.
“Connecting with our carrier systems using the tracking-and-tracing software, when they have it, works great,” Hess says. “Other times, carriers might not have a technology like that available or one that is difficult, or they don’t want to integrate with ours.”Elemica shares mobile-ready information with shareholders along the supply chain.Elemica
In those cases, Nolan Transportation uses GPS trackers or mobile-ready devices to receive shipping updates.
Meanwhile, Elemica uses barcodes, application programming interfaces (APIs) and other technologies to integrate between shippers, trucks, rail, marine and receivers.
“One of the things that we’re starting to see is the ability to really do multiple modes of track and trace through barcode,” Cahn says. “Technology has to integrate those different mechanisms to synchronize that data within our network.”
Hardware solutions Devices used to monitor refrigerated container temperatures are becoming more affordable, Gibbs says.
“There’s a lot more adoption of new hardware technologies that are not just at the tractor level, but also at the trailer level,” he says. “Then also at the product or SKU level, on individual pallets and certain bulkheads inside of a trailer. There’s more multi-zone technologies that are easily adoptable now than there ever have been in the past.”
Devices are also becoming more advanced, allowing sensors to send data in multiple directions. This allows drivers to change the temperature if needed.
“I’m checking a sensor on a truck, and that sensor is telling me that something is out of tolerance,” Cahn says. “The temperature has changed. We’re sending that information back up to the network, but the network is not doing anything about it. The network is not sending information back down to that sensor to readjust the thermostat in the truck.”
Instead of calling the truck driver with instructions to change the temperature, sensors can send those directions to the truck.
Moving to the cloud
Having data accessible on the cloud is another major trend impacting the industry.
“There’s a big move in general to the cloud,” Gibbs says. “You have a lot of on-premise solutions, where there’s been a TMS created, but it was created for somebody that was running it within their own data centers on their own servers, and that customer customized that software suite to fit their business. And, it’s all on-premise instead of being in the cloud or more accessible. So, there’s a big shift for all of the groups—carriers, shippers, brokers and 3PLs—to move to more of a cloud model.”One trend during recent years is the increasing demand for live updates on shipments during transit, according to Nolan Transportation.Nolan Transportation Group
Many brokers subcontract to smaller carriers, which may not have cloud capabilities. In that case, there are mobile solutions that can be used. However, even the vast number of small carriers remains to be a challenge for tracing.
“There’s so many small, owner-operator carriers out there in North America that it’s a big challenge to get some of the contextual information off of their systems,” Gibbs says. “They may use a mobile app to manage the day-to-day operations, or they may just take phone calls from their brokerage contacts. There are ways around it with mobile applications for smart phones.”
But, the need for a standardized, widely acceptable platform can be achieved through the cloud, Zaffarano adds.
“The solution no doubt lies with a third-party network that can talk to many diverse systems and pull it all together into one source of truth for the shipper,” Zaffarano says. “The cloud has advanced the potential of a handful of 3PLs that can move us closer to true real-time visibility of each shipment. The question will be, who pays for it?”
Predicting track and trace
The industry is headed toward creating technology that uses data analytics to predict and make recommendations, says Cahn.
For example, if a carrier is typically late to arrive, instead of expecting the shipment on Tuesday, the system can predict it will arrive on Wednesday.
In addition, technology will one day be able to make recommendations. For instance, if there is a virus outbreak or a hurricane, the system can recommend changing the source of supply to a different part of the country.
“That’s a next-generation artificial intelligence kind of machine learning capability,” Cahn says.
Whether it be real-time alerts, cloud-based systems or abiding by regulatory changes, today’s track-and-trace solutions allow shippers, carriers and receivers to tackle a host of ongoing challenges in the industry