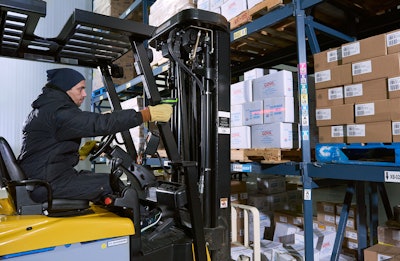
The rise in consumer demand for perishable food items, increase in international trade and expansion of the organized food retail industry are all contributing factors heating up the cold chain market. Each year, billions of tons of fresh food products are lost. The International Trade Association notes nearly half of all food never makes it to a consumer’s plate. The needs of the cold chain are vastly different from that of their temperature-controlled counterparts. Cold chain logistics guarantee the storage, transport and distribution of specific products – such as perishable food or certain vaccines and medications – at the proper temperature to ensure integrity and quality. In addition to product revenue losses, a cold chain that isn’t optimized to meet rising demand will see productivity, reliability and accuracy fall as quickly as the temperatures.
For mobility solutions to function at maximum efficiency in cold environments, they need more than superficial protection—they need to be custom-designed to have computer parts and materials that can effectively adapt to optimally function in freezing environments. Every component from the casing to internal circuitry can be optimized for use in the cold chain.
Condensation is the No. 1 cause of device repair and replacement in the cold chain. Device screens that are not designed for cold environments collect condensation both outside and inside the device. This causes internal components to corrode, short-circuit and fail. Mobile computers need to handle cold temperatures and constant movement between different temperature zones and changing humidity levels. Cold chain devices not only have housing specifically constructed to prevent moisture from getting inside the device, but also integrated heaters to keep scan optics from fogging up.
Frost is the next factor to consider when evaluating devices in the cold chain, as it can cut down on device reliability and readability – leading to increased errors. Standard grade LCD screens are prone to frost, which prevents users from seeing prompts and verifying data entry. Frost also impacts optical ports in barcode readers, which halts the functionality of the device and leads to increased downtime between shifts.
You wouldn’t be able to talk about the cold chain without mentioning temperature. Workers tend to be outfitted in specialized gear, which typically includes thick gloves to operate efficiently in cold chain environments. The ergonomics of the device need to be maneuverable and glove-friendly for data entry. Printing equipment has also come a long way, with certain mobile printers being able to compensate automatically to optimize and balance print speed and quality down to -4°F/-20°C. Labels need to be properly tested to handle sticking to surfaces below freezing while remaining adhered to surfaces and meeting Food and Drug Administration (FDA) material requirements for indirect food contact.
All these devices require energy, so battery technology is another consideration. The cold chain is dependent on batteries to keep the supply chain moving to ensure reliability and productivity. Standard lithium-ion (Li-ion) batteries can’t release their energy properly when temperatures drop, which is why low-impedance Li-ion batteries are ideal for colder environments.
The most modern mobility devices could be challenged to perform optimally if the wireless networking within the cold chain environment is not up to par. It is critical for access points (APs) to be installed directly in refrigerated or frozen storage areas to provide proper coverage.
Relying on APs outside the cold zone will result in weak and blocked signals because of interference of thick walls and insulation. This means APs within the freezer environment require specialized heated enclosures to protect against condensation and cold. Specialized antennas with common access points are also ideal to correct the multipath effect prone to cold environments with heavy condensation.
As processes change over time, it is important to evaluate alternative data-collection options. Consider using speech recognition and RFID alternatives to increase accuracy in data entry within the cold chain environment. Speech recognition terminals can be worn on a belt or holster and under coats where they aren’t exposed to cold temperatures. In fact, a recent report from Honeywell showed nearly 1 million distribution center workers using voice-directed solutions have achieved 35% productivity gains, 50% error reductions and 30% fewer safety incidents.
Using RFID to collect data requires no line-of-sight. As condensation frequently occurs after pallets are shrink wrapped, it can be challenging for laser devices to read labels underneath, where RFID can read data accurately and efficiently. Sensors can be added to pallets and trucks to ensure cargo security as food products are in transit from manufacturer to store.
The cold chain market requires specialized solutions for optimal productivity and profitability. A solutions provider with extensive knowledge and industry expertise can help achieve success.