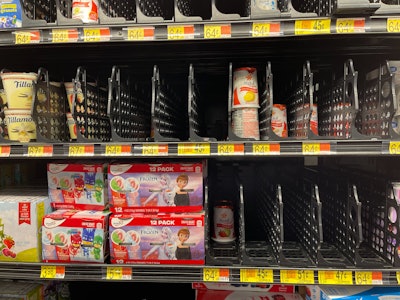
Throughout 2022, consumers have felt the pain of supply shortages via inflation and longer wait times for goods and services, even as significant COVID-19 threats subside. So, what more appropriate way to close the year than a beloved holiday staple missing from the table?
In the weeks leading up to Thanksgiving, grocery stores prepared for a potential shortage of turkeys, driven by an outbreak of bird flu. While some varieties of turkey were impacted more than others, the news is a reminder that sometimes, the global supply chain throws food manufacturers curve balls that aren’t within their control. And the holidays are no time to leave customers in a lurch.
As you look back at your holiday season operations and start planning for the 2023 holidays, remember that supply shortages are a cascading issue – the bird flu outbreak began impacting turkeys in the spring – so don’t wait to prepare for potential 2023 holiday roadblocks. Here are a few ways to start preparing the supply chain to avoid shortages ahead.
Don’t put your eggs in one basket
Uncontrollable crises can severely impact the food supply chain, whether it’s COVID-19 slowing down production, or natural disasters such as fires and hurricanes shutting down production entirely. Another example of cascading impacts: Hurricane Ian is estimated to have caused up to $1.5 billion in agricultural losses, and because of flooded fields, the start of harvest was delayed, potentially impacting prices and availability even more in the coming months.
Food manufacturers often don’t have the luxury of quickly switching to new suppliers in a different region because of growing conditions, but that doesn’t mean food manufacturers can put supplier diversity on the backburner. It’s important to have already established relationships with multiple suppliers in fertile regions in the event one supplier goes down for reasons that don’t impact other suppliers. Manufacturers should also have a plan in place if the entire region is impacted. This could mean having contingency plans to substitute an ingredient, have alternative packaging available or re-routing distribution to ensure the products that are available are heading to areas of higher demand.
Get smart(er)
Consider an alternate situation that is a reality for many manufacturers: having more than enough supply. In fact, having too much supply. Although some manufacturers are no longer struggling to meet demand, they now have the challenge of excess materials spoiling, or inefficiencies with too much work-in-process. The result could actually leave customers still waiting for the product to restock at the store. Automating manual processes and ensuring flexibility across the supply chain can help move more materials faster and with more consistency to the end customer.
Of course, automation can only be successful if a manufacturer’s team understands how to use it – a common issue across businesses, with the World Economic Forum estimating 50% of all employees will need to be reskilled by 2025. Now is the time for supply chain professionals to reskill employees, whether that’s getting their certification to operate equipment in the warehouse or helping them understand best practices for monitoring and managing autonomous mobile robots (AMRs), as an example. This can help manufacturers ensure efficiency for the next holiday season and inoculate themselves against labor shortages.
Let data be the guide
Manual processes might be okay for manufacturers focused on slower bulk purchases, but for fast-moving consumer packaged goods, a paper-based or Excel-managed supply chain system won’t cut it anymore. Supplies can spoil too easily if not monitored and tracked, leading to waste throughout the supply chain and amplifying the impact of existing shortages. And without deeper visibility into sales trends, it can be difficult to understand what inputs need to be ordered to keep store shelves stocked.
Demand planning technology can help alleviate inventory issues across the supply chain. With a deeper understanding into available supply and sales history, manufacturers can prepare for potential shortages during times of anticipated higher demand – as well as pivot quicker when responding to shifting demand or unexpected shortages. In addition, by better managing inventory levels, manufacturers can reduce unnecessary waste.
No more half-baked strategies
Demands on the food supply chain have only accelerated in the last few years, requiring manufacturers, distributors and retailers to rethink their strategies to keep products on the shelf. But while the complexity of these changes isn’t going anywhere, being proactive and planning for cascading disruptions – by diversifying suppliers, training employers, and adopting next-gen technology – can help take shortages off the menu for the 2023 holidays.