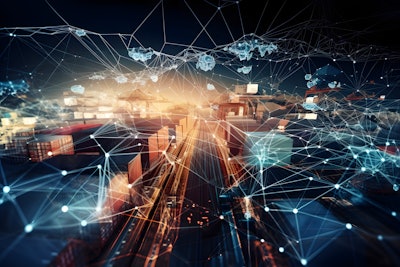
Passages of commercial vessels through the Suez Canal dropped by nearly 80% between May 2023 and May 2024, according to research by Project 44, as repeated attacks in the Red Sea by Houthi rebels have effectively stalled shipping in the region.
On the other side of the hemisphere, low water levels resulting from a drought exacerbated by El Nino resulted in restrictions on the use of the Panama Canal and a 36% decrease in transits between January 2023 and January 2024, according to UNCTAD.
Disruptions to shipping and other factors, from looming dockworker strikes to the impact of the Ukraine-Russia war on the oil and grain trades, have a significant impact on the supply chain and, ultimately, consumers. Shippers have increased rates as their operating insurance costs have risen. They use more fuel as they opt for longer routes. Because of all that, energy and food prices are increasing all around the world.
These developments are high-profile evidence of the tremendous complexity of global supply chains, but events don’t have to be the stuff of headline-grabbing news to have a significant ripple effect. Even a single minor disruption in one port or storage facility can create unforeseen complications for supply chains across the world—in a commercial embodiment of the butterfly effect.
When a major disruption like the one currently unfolding at the Suez Canal takes place, the impact to supply chains can be catastrophic. There are so many variables and uncertainties involved in transporting merchandise around the globe, that the ultimate outcome is impossible to predict. And there is no magical fix for it, either.
As supply chains continue to get more complex and less predictable, the ability of companies to make informed, real-time decisions becomes even more critical. Companies need clear visibility into supply chains and the ability to put their data to use in making real-time decisions.
Monitoring provides clear visibility
With complex supply chains that can be at the mercy of external factors, companies need unfettered visibility to make informed, timely decisions. Real-time monitoring and data management can provide that visibility, giving companies the ability to respond quickly—or even proactively—to events and alter routes, adjust inventories or make other changes that reduce delays and deliver the right products on time and in good condition.
Real-time supply chain and cold chain monitoring can be an expensive proposition, however, so it’s helpful to understand the different types of monitoring tools and how they can be deployed in the most cost-efficient manner.
Real-time, or active, data loggers can constantly monitor goods in transit and transmit critical data via GPS or cellular connectivity. Along with providing the exact location of goods at any point in time, they provide real-time monitoring of temperature changes and humidity levels which affect perishable goods. The loggers also transmit data on other factors such as shock, vibration and light exposure, which can be critical information for certain goods.
But not all data needs to be transmitted in real time to be useful. Sensors that aren’t connected cost less to operate but can also record data throughout a shipment on temperature, humidity, shock, vibrations and other factors. That data can then be used for planning and optimizing shipping routes, packaging decisions, and even identifying operational inefficiencies and areas where product damage, temperature fluctuations or transportation delays regularly occur.
Employing these sensors is effective for shipments that may not have a high value or transport goods that aren’t perishable. A company also can use the data to identify processes they can improve, choose more efficient routes and set benchmarks for future operations.
Real-time and passive monitoring can provide visibility into the supply chains and collect vast amounts of data, but making efficient, effective use of that data is still a challenge for many companies. Having a lot of data, even real-time data, doesn’t do much good if you can’t draw actionable insights from it in real time. This is where artificial intelligence-powered automation helps.
AI-powered automation provides real-time insights
Supply chain organizations that want to turn their data into action need to automate processes. Considering the amount of data they collect via monitoring, any attempt at manually extracting insights, or identifying patterns and anomalies in shipping routes will come up woefully short.
Automating the extraction and analysis of data from real-time monitoring and sensor data puts the most pertinent data at the company’s fingertips, enabling it to identify trends and make improvements. It also allows the creation of standardized formats for collecting information, which in turn makes analyzing that information more efficient.
In addition to analyzing historical trends and real-time activity in your supply chain, artificial intelligence (AI)-powered automation also allows you to look ahead, using its contextual analysis to predict disruptive events and recommend proactive actions to ensure the safe, timely delivery of goods.
Companies looking to make the best use of their data may consider building their own solution, but that comes with some drawbacks, including high investment costs, lingering technical debt and the burden of managing and updating an in-house system. Acquiring a purpose-built system from a provider that specializes in supply chain analysis and operations, on the other hand, allows companies to avoid some of those costs with an effective system that can be implemented quickly.
Conclusion
The lesson from recent years is that companies that rely on a global supply chain, including those dealing with cold chain data on perishable goods, need to expect the unexpected. Economic twists and turns, natural disasters and manmade disruptions play havoc with the global transport of goods, affecting shipping routes and inventories, while often driving up costs.
Real-time visibility and the AI-powered, automated analysis of historical and current data is necessary for companies to respond quickly, agilely and proactively to disruptions in the supply chain. It’s the most effective way to ensure on-time deliveries, satisfied customers and profitable bottom lines.