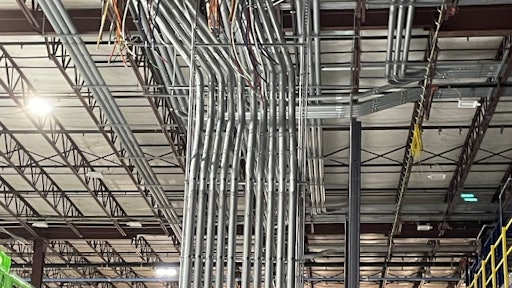
Whether in the grocery or frozen sectors, food and beverage users of all sizes understand the increasingly outsized role automation plays in warehouse logistics. A recent report from Insight Analysis shows spending on warehouse construction and automation is expected to ramp up in 2024 and 2025 as demand for fulfillment capacity continues to expand, but headwinds caused by the current real estate market are making greenfield construction less feasible and appealing. The natural response has been to explore retrofitting existing facilities to incorporate this critical technology, a tactic that can help save valuable time and dollars when considering the ever-growing costs and timelines for new construction projects.
While giant retailers opened the door to the initial automation retrofit boom, expect more players to become active in this next wave, as companies recognize these upgrades are necessary to keep pace with other evolutions occurring across the supply chain. Much has been written about the criteria to consider for selecting an automated solution and how to evaluate the different tech platforms available, but what do you need to know to get your facility ready for a retrofit and avoid a major derailment?
It can take up to a year to adequately plan for an automation retrofit when factoring in the evaluation, design and preconstruction that takes place prior to installation. Many companies we’re in discussions with are surprised to learn of all the preliminary steps that need to be taken before the first barricade is set up. Overlooking this step can inadvertently create early hurdles when considering demand forecasts.
For food and beverage users seeking to stay ahead of the curve, here are four pivotal areas to focus on when preparing for an automation retrofit:
1. Operations ramp down
Disruption to daily activity and reduced capacities are always the biggest drivers of anxiety for our clients when discussing the foundational step of ramping down operations. And while reduced outputs are inevitable for any type of warehouse retrofit, developing a clear strategy – in tandem with an experienced general contractor – on the front-end will ensure ramping down isn’t unnecessarily prolonged.
Designate areas that need to be blocked off, which often include dock doors. For example, 10 doors need to be blocked off, but if the client determines they simply must have access to at least eight doors to operate sustainably, you’ll need to adjust and find a workaround. Understand what matters for the long-term success of clients, and just by intentionally understanding their business can better help minimize impact. One strategy many clients choose is to burn off existing inventory for 60-90 days before the process starts, opening additional space for the automation infrastructure to be installed. This approach seems to help significantly.
Some challenges with ramping down aren’t product-related, as the client could have equipment or storage areas blocking access in the middle of the retrofit area. This part of the process is ultimately about communication and understanding the key variables that guide their business, primarily with product flow. For instance, initial plans called for a project to be divided into three phases. But when output started falling below the company’s preliminary estimates, the plan had to pivot and be modified to help maintain progress. In general, if the client can’t effectively continue moving their products, they might have solvency issues, so it’s crucial for everyone to be flexible when it comes to ramping down operations.
2. Concrete and structure
Clients lean heavily on the design team and general contractor to execute this portion successfully because the more efficiently concrete pours and new structures are completed, the quicker they can get racks up – and racks move product.
These foundational elements require a great deal of precision, as the vibration and levelness tolerance for the robotics being installed are very small. Large concrete pits and pad foundations are needed to support the structure and equipment, some of which get integrated into the existing foundation. Take for example, a large retailer who discovered during the design process that they needed to incorporate below-grade tunnels to maintain access to areas within their racking systems. Though it was an unexpected add-on cost, mitigating this on the front-end saved the company a significant amount of money, especially compared to the price tag they would have faced if trying to problem solve after installations had already started.
3. MEP infrastructure
Automation equipment requires a significant amount of electrical power and compressed air, as well as fire protection systems. Most existing buildings don’t have the spare capacity, so new utilities need to be established. This includes utility transformers and electrical switchgears, compressed air, and in some cases, additional or replacement fire pumps.
One unique challenge is estimating the power necessary to operate new robotics systems. Compared to building out a healthcare facility, for example, most of the equipment used in hospitals has been around for decades, so you know exactly how much power it takes to sustainably support it – like an MRI machine, for instance, always needs the same amount of power. With automation, as soon as it’s figured out what it takes to power a certain robotics system, new technology comes into play that can alter the entire equation. Like so many other components of the retrofitting process, it’s yet another moving target that requires adaptability and communication.
One of the biggest keys to project success is ordering the switchgear as early as possible, which is imperative for avoiding major delays. Some panels have smart breakers and require as much as 14 months of lead time to acquire and install due to ongoing supply chain issues, so the earlier you can get the switchgear operational, the quicker the transition to new automated systems. This can be facilitated by the builder, but must happen at the outset.
4. Disruptions
The installation of new MEP infrastructure requires the temporary shutdown of existing systems to support tie-in and integration. The disruptions often involve equipment being relocated and workers having to adjust their normal routines. By generating a one-page document that outlines any changes to the existing operational areas ensures there is a simple and streamlined “road map” for every team to reference in the event of an issue – no matter when or where it occurs.
The average time for a shutdown during the retrofitting process is 8-12 hours, which in many cases, can be integrated with regularly scheduled shutdown periods for maintenance, inspections, and software updates. Ultimately, good communication can align work with the clients’ scheduled shutdowns and reduce dead periods as much as possible. Again, you just have to know what matters for the long-term success of the client.
Considering all the factors that go into an automation retrofit, there are undoubtedly some challenges that must be addressed. Ultimately, the key to making this a successful transition is identifying an experienced general contractor early in the pre-planning process to lay out the roadmap. While the new robotics being introduced to the market are exciting to think about, the work must start at a foundational level – finding the right partner to help build-out a facility that will sustainably house the transformative technology.