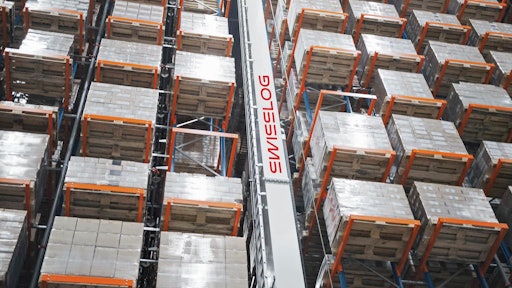
The demand for cold chain storage continues to grow while the market continues to experience numerous challenges
For instance, many warehouses are still struggling to attract and retain skilled labor, especially in cold storage facilities where working conditions can be harsh. Limits on how long employees can spend in freezer environments often results in low hourly productivity rates. These facilities are also under pressure to manage energy costs, as energy is the second biggest expense in cold chain warehouses, behind only labor.
Additionally, the nature of cold chain storage is changing. Long-term storage, once dominant, now represents a fraction of total warehouse income in many facilities. Today’s cold storage facilities must accommodate higher-turn velocity inventory.
Fortunately, automation technology can play a key role in addressing these challenges. However, unlike other facilities where flexible automation systems can be adapted to virtually any environment, achieving the true benefits of automation in a cold chain warehouse requires tight integration between the building design and automation system.
Designing for efficiency
Traditional warehouses with 32- to 40-foot ceiling heights are not conducive to efficient refrigeration because the square footage of the roof introduces heat from solar energy, increasing the load on the refrigeration system. If the facility is a deep-freeze warehouse it will also have a heated floor, so a large square footage floor also adds to the heat load.
These issues can be minimized by a building design that reduces roof and floor square footage without compromising storage capacity. That requires building taller warehouses, enabled by automation systems that support vertical storage. Relying on these automation technologies allows the building designer to achieve a footprint approximately one-third that of a conventional facility.
These high-bay warehouses typically have ceiling heights of 100-140 feet and, in addition to reducing refrigeration costs, increase inventory density by reducing aisle widths and enable multi-deep storage channels, further increasing cooling efficiency.
Designing the building to fully leverage the space-saving capabilities of the automation system can result in a reduction of building energy consumption of 20%. That equates to a 10-15% decrease in electrical power draw in the refrigeration system, reducing both the initial cost of the system as well as ongoing operating costs.
Getting the automation vendor involved in the design process as early as possible helps ensure footprint and energy savings are maximized through the integration of the automation system and building design.
Automating the cold chain warehouse
When it comes to integrating automation technology into the design of cold storage facilities, there is no single solution that meets the requirements of every facility. Automation should be tailored to product type, throughput and desired density, as well as the large variation and changes of inventory and order profiles, which are often found in third-party logistics (3PL)-operated warehouses.
It’s also important to consider the automation control platform offered by the automation vendor. Stand-alone automation control systems can create data silos while forcing operators to adapt to different interfaces for each system.
A modular automation platform that integrates automation control into the warehouse management system (WMS) platform is preferred. This approach enables increased use of data for system optimization and business intelligence and supports a universal operator interface across the warehouse. The system should also include standard APIs to integrate with the enterprise resource planning (ERP) system for enhanced inventory management.
The primary automation solutions used in cold storage warehouses include pallet cranes, pallet shuttles, pallet conveyors, robotic layer picking and automated carton transport and handling systems.
Automated storage retrieval systems (ASRS) pallet crane systems are a cost-effective and reliable approach to enabling high-bay warehouse designs where the highest density and throughput are not required. In addition to enabling vertical storage up to 140 feet, by eliminating the need for forklifts, they allow aisle widths to be reduced from 12 feet to 5 feet, freeing up additional space for storage. Storage rack configuration can be from 1- or 2-deep (fork fitted cranes) up to 10-15-deep (shuttle-based cranes). Adding a second load handling device on a stacker crane increases throughput capabilities even further, especially at long crane aisles.
Pallet shuttle systems for high-bay storage in deep-freeze and chilled temperature warehouses are capable of storing pallet loads in the highest density configurations at heights up to 110 feet. They can also support the high throughput requirements of today’s high-turn cold storage facilities.
Pallet conveyor systems provide energy efficient and space efficient transportation of pallets for both light and heavy loads. Certain of these multifunctional systems have a flexible design that allows them to be configured to meet a wide range of requirements for automated pallet transportation
Automated carton handling systems use robotic delayering, re-layering to layer order pallets and case picking to automate downstream operations within the cold chain warehouse. Some systems automate the task of building store-friendly, multi-SKU pallets by combining light-goods shuttle systems, conveyors and high-performance de-palletizing and palletizing robotic technology.
Managing for efficiency
The building design and choice of automation system can significantly reduce the costs of building and operating a cold storage warehouse. However, innovative warehouse operators are also employing supplemental technology to reduce energy costs.
Energy costs on a per kilowatt hour basis are based on demand. Reducing energy costs during high-demand periods can drive down average overall energy costs. This is challenging because surge pricing is often triggered by high ambient temperatures, which increase the thermal load on the refrigeration system.
In a standard industrial controls system, systems are turned on and off without consideration for peak energy costs. However, by tuning the operation of the control system using advanced control algorithms that factor in internal and external temperature, the environment can be effectively overcooled during non-peak hours, significantly reducing energy consumption during peak hours.
Monitoring is key to this approach. Sensors installed across the warehouse enable visibility into the thermal envelope across the warehouse and support the algorithms that manage temperature control automatically.
Meeting the energy efficiency, low labor and high throughput requirements in today’s cold storage warehouse can best be accomplished by collaboration across the building designer, automation provider and warehouse operator.
This collaborative approach ensures the building designer can fully leverage the space and energy-saving capabilities of the automation system, while significantly reducing exposure to cold environments by warehouse staff. When supported by advanced energy management strategies that minimize the power draw during peak periods, these facilities can achieve new levels of energy and labor efficiency.