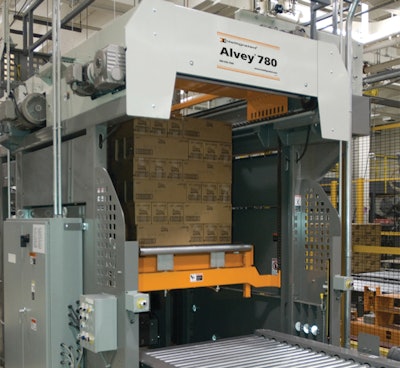
While the global economic downturn over the past few years has put the squeeze on business expansion, several success stories have managed to take shape. One in particular, the strong growth in warehouse automation, continues to flourish due to a convergence of factors that are creating a near perfect environment for both equipment and software providers and their customers.
Setting the stage for expansion
The current interest in warehouse automation is being propelled by several overarching drivers, according to Mike Kotecki, senior vice president at Dematic, and they are generating nothing short of a “revival” in the industry, he says.
For starters, the economy is coming back, albeit in spurts, and companies are spending again. However, unlike previous turnarounds in the food and beverage industries that were characterized by a rehiring bonanza, companies are not interested in bringing back excessive headcount.
“There’s a clear trend to apply technology where possible and reduce manual labor,” says Kotecki. In addition, the warehouse automation technology that’s available on the market today allows companies to “leapfrog competitors and improve flexibility,” he says. “If I implement a system that allows me to work with fewer headcount, then I’ll be more flexible as the economy changes and I’ll be more recession proof the next time around.”
Intelligrated’s executive vice president, Greg Cronin, looks at labor from another aspect, primarily from a cost standpoint.
“Baby boomers are retiring, and many of the younger generation aren’t interested in manual labor jobs,” he says. Moreover, an aging workforce coupled with the physical demands associated with warehouse jobs means the medical coverage for staff is also very high. “Many companies are willing to make capital expenditures today that they weren’t willing to make before to try and offset the labor situation,” says Cronin.
Other trends are at work, continues Dematic’s Kotecki. “There’s a good deal of consolidation going on; merger and acquisition activity is up. There is also a move to more regionally-based retail outlets and a surge in small format, neighborhood stores.” This includes smaller stores that are geared to appeal to a specific demographic, he notes. The result is “less on-site storage and a need for more deliveries, all of which cranks up the number of SKUs.”
Intelligrated’s Cronin adds e-commerce to the list of external factors that are fueling growth in warehouse automation. “E-commerce is definitely starting to make a play in the food and beverage industry. And, what it brings is so different. You’re not just shipping pallets and cases anymore, you’re opening up the cases and picking individual pieces.”
This requires an entirely new level of sophistication. “It requires different software and different automation equipment,” says Cronin. For instance, “A lot of the [older generation] WMS systems out there today don’t work well with automation and they don’t really work well in the e-commerce and each-picking world.”
Intelligrated’s response, therefore, “is not only to bring in new physical automation solutions, but increase our capabilities on the software side to be able to handle all of these new requirements on the automation side and the each-picking side.”
In a related development, home delivery is also experiencing a comeback, explains Dematic’s Kotecki.
“There were a number of false starts some years ago,” he says, referring to the Internet-based grocer Webvan. “But, home delivery is growing in popularity, especially in high population areas,” he says, which “presents a whole new set of challenges for the material handling group, including many sub-categories of product and so forth that each need to be available and stored for a long period of time, in some cases, but then must be available in a moment’s notice. Inventory levels are a little higher; visibility is a little lower because it’s instantaneous; and you also need a transportation network that’s phenomenal.”
Meanwhile, new federal regulations related to food security along with consumers’ changing demands are doing their part to drive changes and heighten interest in automation.
“Traceability is a significant external driver,” remarks Pete Hartman, president of Retrotech. He points to last year’s listeria outbreak in cantaloupes as a recent example of the visibility gaps that exist in the supply chain, and which the Food Safety Modernization Act (FSMA) attempt to address. “[Officials] knew it was the melons, but they couldn’t find out where they came from.”
A new breed of automation tools
Fortunately, the automation tools being introduced today are better than ever at addressing the challenges brought about by the proliferation of SKUs, longer and more complex supply chains, and traceability requirements, says Hartman.
“The automation market is maturing,” he says, much like the computer industry has over the past few decades. “There was a time when the computer industry was very fragmented,” recalls Hartman. The consumer was very focused on a particular manufacturer and its hardware technology, whether it was IBM, DEC, or Compaq, for instance. “But, if you go into someone’s office today and ask him what kind of computer he has, he may not even know. What he does know, however, is the functionality and capabilities that he enjoys by having a computer and software on his desk. And, that’s similar to what’s happening in the material handling and automation business.”
In other words, “People are becoming more focused on the application driven issues as opposed to the specific equipment or technology,” explains Hartman. “There’s a growth in what we call the ‘systems engineering’ aspect of developing these capabilities within an organization that is much less dependent on hardware. Just like in the computer industry, there is a wide range of providers with very good, very stable, very workable technology.”
Hartman is quick to note, however, that, “Most technologies are just an enabler. Unless the linkage has been made between the technology and the business problem to be solved, you don’t achieve success.”
In fact, one of the biggest challenges for potential buyers “is to understand—and to move past—the glitz of the equipment and be sure that the business problem is being properly addressed,” Hartman emphasizes.
The good news is that more sophisticated modeling and simulation tools are being developed to accurately identify those business problems so that the right automation systems can be implemented, says Hartman.
“We now have simulation tools that actually replicate the physics of a given situation. For example, if something goes wrong and a box falls on the floor, the simulation tools depict that box on the floor, its movement, and the result. We have the ability to see what’s happening in the systems with an incredible degree of accuracy, which in turn gives us greater certainty around the solution to the problem, before we commit to spending big bucks on the equipment.”
For Retrotech, their role is to provide customers with in-depth knowledge to make an informed decision.
“We are not an equipment manufacturer,” says Hartman. “Our value proposition to our customers is that we’ll do the front-end work,” which entails a comprehensive analysis that’s conducted before the equipment is purchased. Then, “Once a decision is made by the customer to proceed with an implementation, we’ll get the equipment from the manufacturer(s), Daifuku or Swisslog, for example. We then incorporate that equipment into the overall system that has been conceived.”
Indeed, Retrotech used three different equipment manufacturers for one system they designed for Cargill. “So, it’s not vendor specific, whereby one vendor can do this and the other can’t, the equipment is largely interchangeable,” explains Hartman. “What isn’t interchangeable is the design of the equipment and its alignment with solving the business process at hand.”
Adapting to a changing environment
Perhaps one of the best features of the new generation of warehouse automation is its ability to adapt to changing environments, explains Hartman. “Flexibility around information processing is one example, and that’s having the ability to alter, change, or override the decision rules that are built into the software and control systems to accommodate changing requirements in the marketplace.”
Another example includes “path flexibility,” which Hartman describes as “the ability to take anything, anywhere in your system and put it anywhere else, as opposed to being constrained by a very specific path.”
Although much of the previously installed warehouse automation systems didn’t offer these types of flexibility, “Quite often that existing technology can be upgraded for a reasonable cost,” he adds.
For its part, Dematic has rolled out several solutions designed to address the challenges of today’s marketplace. One is “a buffering system to decouple the inventory pulling activity from the shipping activity,” explains Kotecki.
“For example, let’s say you’re shipping a tremendous amount of SKUs to regional liquor stores. [The goal] is to make sure that when the truck pulls up to the liquor store that there’s a pallet, six cases, a bunch of loose items, and maybe some totes, all in precisely the order that the person in the truck needs them, and that the order is complete and the truck did not spend a lot of time at the dock door at the distribution center. So, I’m going to accumulate that order at the case or tote level in a buffer, called a Multishuttle. It’s a multi-access, high density storage machine for cases and totes that can accumulate an order, not necessarily together physically, but in the system. Then, we electronically ‘push a button’ and out comes everything in exactly the proper sequence for that order, it goes to the dock door exactly when you need it, totally complete, and goes on the truck in reverse order of the deliveries.”
Kotecki says there is also more interest in solutions targeting three common issues—slow moving inventory, automated pallet storage, and removing labor from the distribution center.
“Many people are starting to look at their warehouse and say, ‘Okay, I’m automated, I’ve got all the high speed stuff, but I’ve still got three quarters of my warehouse dedicated to pallets and pallets of sardine-flavored Jello that no one is ever going to use.’”
Dematic’s answer is RapidStore, a modular automated storage and retrieval system (ASRS) for unit loads like pallets. “You can stuff this thing with all of your slow moving inventory and the machine is super fast, it rotates the SKU at the pick-face, which is at floor level, so if the worker is on a pallet jack, he takes one lap around the ASRS and the system is constantly presenting the slow moving stuff needed to fulfill the order.”
And, while it’s admittedly “not sexy,” says Kotecki, “there is a tremendous desire to automate pallet storage. We’re going in to existing facilities that are already pallet racked and rather using a whole bunch of people on fork trucks, we use automated guided vehicles (AGVs), map the system in three-dimensions electronically, then the AGVs perform the task of storage and retrieval in that warehouse.”
Removing labor from the distribution center is another ongoing quest. Dematic’s LaserTrucks+ is a seamlessly integrated, voice-directed and driverless laser guided pallet truck that increases case picking productivity by eliminating non-productive steps.
“The amount of walking is cut down, productivity goes up (by about 20 to 40 percent), and workers aren’t deadheading back and forth to the dock,” explains Kotecki.
So, how much does it cost?
Not only is warehouse automation more robust, it’s decidedly more affordable today. And, while larger companies are making sizeable investments, there’s plenty of activity in the mid-level market too, according to Intelligrated’s Cronin, “because they also realize that they need to respond to the various issues in the marketplace.”
Cronin says that medium-sized companies are “looking to phase-in the automation so that it’s more of a realistic and economic reach for them.” Typically, that may include starting with conveyor and sortation equipment, he explains.