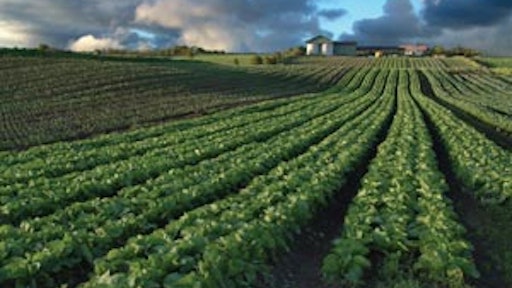
Though it is of little comfort to the families of the more than 200 people across 26 states stricken with E. coli from eating tainted spinach, the late summer outbreak could have been much, much worse. It was through fast action—and software—that the contamination didn’t affect more people.
In fact, the U.S. Food and Drug Administration (FDA), Centers for Disease Control (CDC), other government agencies involved, and even the company at the center of the crisis, Natural Selection Foods of San Juan Bautista, CA, are all being commended for the speed and efficiency with which they responded to the national crisis.
“We commend the FDA and industry for working together to first protect public health, and then isolate the cause of the outbreak to help restore confidence in the overall spinach industry as quickly as possible,” says Tom Stenzel, president and CEO of the Washington-based United Fresh Produce Association.
The FDA first was alerted to the outbreak on Sept. 13, and within hours, issued a warning to all consumers to avoid eating any and all spinach. It then launched one of the most extensive investigations in its history as more than two dozen investigators fanned out to try and trace the root of the contaminated spinach from fork to farm.
“At 1:30 in the afternoon on Sept. 14, we got a call from the FDA that there might be an outbreak and that it looked like it might be tied to spinach. By the next afternoon, we started to get reports that it was our brands that people were getting sick from,” recalls Samantha Cabaluna, a spokesperson for Natural Selection Foods.
Ultimately, product identification codes printed on bags of spinach left in the refrigerators of a few of those that were sick led FDA and CDC investigators to Natural Selection. The company immediately issued a recall of all 31 brands of its spinach products shipped with “best if used by” dates of Aug. 17 through Oct. 1. Five companies that received affected product from Natural Selection also issued voluntary recalls within a few days. They were Kenter Canyon Farms, Sun Valley, CA; River Ranch, Salinas, CA; RLB Food Distributors, West Caldwell, NJ; Pacific Coast Fruit Co., Portland, OR; and Triple B Corp., Seattle.
“We pulled everything and immediately went into action to notify our customers,” says Cabaluna. “It was one of the smoothest recalls we’ve ever done. Overall, the recall went very well and everyone executed it very well.”
Finding The Source
In addition to helping execute the recall, supply chain software allowed Natural Selection to trace the lots of contaminated spinach back to nine farms in central California’s Salinas Valley. FDA and CDC investigators later narrowed the investigation to four fields. They are still trying to determine exactly how the bacteria got onto those farms, but it is believed that the bacteria originated at several cattle ranches nearby.
For Natural Selection, the software from HighJump Software, Eden Prairie, MN, stores everything about incoming product, including the farm where it was grown, the plant where it was packed and even the specific shift and line where it was cut and processed. It also traces outbound product to the companies that receive it.
“The solution, Supply Chain Advantage, can help identify products from the source of supply to the point of consumption, and give a complete history of the product no matter where it is in the supply chain,” says Chad Collins, director of product strategy at HighJump. “One of the keys is speed to recall, how quickly you can identify where the product is in the supply chain and what the roots of that product are.”
The software gives users “tracking at all levels of the supply chain. You get full visibility into when and where everything is shipped, and to build up a product trace record with all the ingredients that went into the finished product,” Collins says. “You can track which lots went to which customers and track their movement around the warehouse.”
That’s no easy task, considering the volume of product that Natural Selection handles. The company receives spinach and other fresh fruits and vegetables into its San Juan Bautista facility from dozens of farms covering 17,000 acres in central California, and then processes and packages them into 31 national and private-label brands, including Dole, Earthbound Farms, SYSCO, Trader Joe’s and President’s Choice.
Product is distributed to retail and foodservice channels across the United States and into Canada and Mexico, days from when it is picked.
“Through the many various brands involved, the infected lots were probably all across the country in a very short amount of time,” admits Cabaluna. “It was probably on the store shelves within about five days at a maximum.”
Contamination Spreads Quickly
That’s one of the weaknesses of the modern food chain. A system that so quickly delivers foodstuffs to consumers across thousands of miles can spread disease just as quickly, according to food safety expert John Surak, a retired vice president of quality and food safety at Brooks Food Group, Bedford, VA, who is now running his own food safety consulting firm in Clemson, SC. The outbreak, he says, was typical in size for a product that is so widely distributed.
“That the E. coli spread so fast shows how inter-connected we truly are,” says Bruce Bowen, vice president of retail and wholesale solutions at Aldata Solutions, Atlanta. “We can’t rely on proximity any more to rein in an outbreak. With the sophisticated supply chains that we have in place, product can get across the world in a few hours.”
That’s also why it took so long for the CDC to trace the spinach back to Natural Selection. Those involved in the investigation say there are many arduous and comprehensive steps that must be taken first to identify an outbreak and then to isolate its cause to a single food item.
“It took time to identify spinach as the source and then trace it back to a particular manufacturer,” says Surak, a former U.S. delegate to the international committee that drafted the ISO22000 international food safety standards and a member of the American Society for Quality’s Executive Committee on Food, Drugs and Cosmetics. “That’s some of the most difficult information to put together because you have to develop a diet profile for each patient and then pull together some commonality. It took a lot of police work to come up with those answers.”
The entire process—including the initial medical diagnosis, federal agency notification, patient interviews to compile a diet history, sampling and lab work to develop a DNA fingerprint of the bacteria strain—can take up to three weeks. The average for cases in the spinach outbreak was 15 days.
But, in responding so quickly, the FDA is drawing fire in some industry segments. The major complaint being heard across the industry is that the FDA may have acted too hastily when it urged U.S. consumers to avoid consuming any and all fresh spinach. As a result, many U.S. retailers pulled all fresh spinach products from store shelves—regardless of the brand name.
“While it’s always better to err on the side of caution, there was a lot of money and effort wasted to pull it all off the shelves,” says Duncan McCollum, principal at Dallas-based Computer Sciences Corp.
The FDA “moved quickly, but did not identify the source. Instead, they pulled all spinach, and that hurt the entire industry,” adds Scot McLeod, senior vice president of marketing at CDC Software, Atlanta, the parent company of Ross Systems. “The damage was done. There were a lot of East Coast businesses, for example, that did not have to have their product pulled.”
Protecting The Public?
One such company was AP Military Group, Hudson, FL, the chief supplier of bagged spinach and salads to the U.S. military commissary system worldwide. As soon as the FDA issued its consumer warning, the Defense Commissary Agency (DeCA), the organization that runs military commissaries, ordered its stores to immediately remove from their shelves all fresh spinach. AP Military Group has had to file for Chapter 11 bankruptcy protection due to lost sales as a result.
Bob McMenemy, general manager of AP Military, said his company does about $400,000 a week in salad sales to DeCA, and of that amount, spinach accounts for about 26 percent. Overall sales dropped off about 40 percent at the time.
“As it happened, everything was pulled from the shelves, and we lost not only the product right away but also sales over time,” he says. “We didn’t start selling spinach again until late October.”
For other produce growers, distributors, wholesalers and retailers, the spinach E. coli outbreak caused more than $100 million in lost sales. Industry wide, sales of packaged salads fell off about 30 percent immediately after the FDA’s warning, and have remained 15 percent to 20 percent below normal since.
Fresh Express, Salinas, CA, which supplies about 40 percent of all salads in the United States, was not implicated in the E. coli scare, but its sales have plummeted nonetheless. “We were guilty by association, says its president, Tanios Viviani.
“Many other companies also got caught in the wide net needlessly before the precise DNA fingerprint [of the E. coli strain] was identified,” says Kevin Hume, director of consulting services at supply chain consultants ESYNC, based in Toledo, OH.
But Surak and many others defend the FDA’s decision to issue the far-reaching warning against all spinach. “It’s a moral issue first, but also a due diligence issue,” he says. “It’s in their best interest to pull all product until they can trace its source exactly.”
“For the FDA, their first concern is to protect public health, and they had an obligation to issue a blanket warning,” adds Natural Selection’s Cabaluna. “It took time to determine what produce was at the root, and then from which company it came.
Track/Trace Interest Grows
Thanks to sophisticated supply chain solutions available today, many in the food industry are finding that tracking and tracing product through the supply chain, no matter how far-reaching, is not as difficult as it seems.
Using its HighJump ERP system, J&J Snack Foods, Pennsauken, NJ, a maker of pretzels, cakes, cookies, frozen drinks and novelty items, can locate anything in its supply chain in 10-15 minutes.
The company ships products across the country on hundreds of trucks every week. Every product in every one of those shipments is tracked with a unique lot number.
“Everything we produce is given a lot number based on the production date and time. HighJump automatically attaches that number to everything we do,” explains Tom Appleton, assistant manager at J&J’s Pennsauken warehouse facility.
During a recall, the system takes that same lot number and can give a complete report of what was shipped, how much was shipped, when it was shipped, where it was shipped and contact information there, the carriers involved, and where it is in the supply chain, he explains. “We can pull out every bit of information we need in about 10 to 15 minutes, and then pass it on to our Quality Control Department to address it with our customers.”
By implementing Ross Systems’ iRenaissance enterprise solution, including lot traceability, Berner Foods, Rock City, IL, a producer of cheeses and soy beverages, has cut the time needed to complete recalls to under an hour. It used to take almost an entire day.
“It’s a huge savings of time, and it provides some comfort level to know that we can respond quickly and reduce our pain in the process,” says Troy Grove, its director of business technology. “With full lot tracing, we can determine the disposition of any raw ingredient throughout production and distribution of all finished products and quickly contain the scope of a potential recall.
“Attribute tracking in iRenaissance allows us to monitor quality and product attributes uniquely for each batch or lot, and make sure we are delivering products that will meet the expectations of each customer,” Grove says.
That is what’s motivating Fresh Express, the packaged salad producer, to implement an RFID tracking solution from Boston-based TR3 Solutions.
“Fresh Express is excited about the opportunities that RFID presents to ensure that only the freshest product is on store shelves,” says Dan Wasser, vice president of business information and analysis at Fresh Express.
“If you’re looking at lettuce, spinach or other produce, it typically comes from the farm in totes,” notes Ashish Asthana, co-founder and vice president of marketing and product strategy at Intelliflex, Santa Clara, CA. “You can have RFID in the tote and include information on the farm it came from, whether it’s organic or not, the date it was picked, etc. During shipment, you can also include temperature data so that the retailer can know that it was maintained at the right temperature throughout the process and refuse to accept it if it was not.”
No Longer An Option
Though their numbers are quickly growing, companies like those listed above are still fewer in number than they need to be. Too many companies view tracking and tracing as overhead, CDC’s McLeod maintains. “It’s becoming a necessary component for operating a business, but they do not see the value in it. It doesn’t help them sell product or grow the business; it’s strictly for mitigating risk,” he says.
Aldata’s Bowen disputes that way of thinking. “On the marketing front, it’s one thing to say that you’ve got fair trade coffee, no genetically modified ingredients, organic produce or whatever, but you can be able to prove it by giving people a trace-back to the farm,” he says. On the recall front, “it’s also one thing to say that your product was not affected, but it’s another to be able to back it up.”
These are all important business realities in Europe, where Aldata has thus far done most of its business, especially in the meat, dairy, produce and pharmaceuticals segments. “Traceability is something that European companies started pressing us on a few years ago because of the large-scale mad cow disease scare,” Bowen says. “It’s really in response to them that we developed Aldata GOLD Track.”
Bowen sees supply chain tracing software picking up steam in the United States now as a direct result of the recent produce scares. “You’re definitely going to start seeing more interest,” he predicts. “This is the type of thing that gets the CEOs of the major grocery chains into the mode where they question everything.”
For now, though, many U.S. food processors are still keeping manual records. CDC Software’s McLeod estimates that about half the U.S. food processors fall into this category.
“The U.S. food industry is somewhat lagging in using solutions from source to store,” adds HighJump’s Collins, “but if you benchmark it with other industries, it’s probably on a par.”
Though still not as widely adopted as it could be, tracking and tracing “provides a much more valuable business case now than it did a few years ago,” says ESYNC’s Hume. “The industry is getting better every year with tracking and tracing,” he says. “Pre-9/11, it was an option. Now, it’s more of a requirement.
“You need to know what you’re getting in, who it came from and where it was sent, and to be able to get that information where it needs to be in the event of a recall,” says Hume. “There’s a full range of technologies available. Technology is the first line of defense. Technology can make the supply chain more secure, more visible and help maintain tighter controls. If there’s any opportunity to close the loop on these kinds of things, it makes sense to do it.”