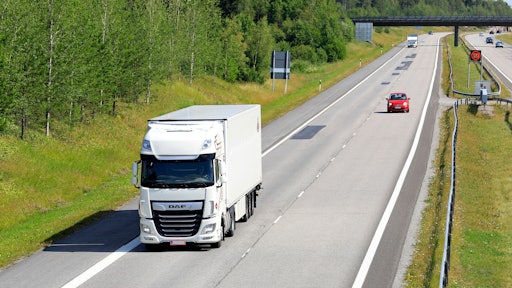
Amidst the hustle and bustle of the holiday season, cold storage and produce shippers often face more logistical challenges than usual.
Demand for fresh produce, frozen products and refrigerated goods skyrockets as consumers plan holiday gatherings. In fact, a recent Forbes survey found more than half of Americans anticipate food purchases will be one of their biggest expenses this holiday season.
There are many moving pieces for companies to consider this time of year. As demand increases, operational challenges also arise, including cold and icy weather in most regions of North America, impacting scheduled deliveries. At the same time, employees take more time off than usual to celebrate the season.
With this in mind, it’s critical to evaluate your carrier partner(s) to ensure they have the temperature-controlled shipping capabilities you need during this critical timeframe.
‘Must haves’ when considering a temperature-controlled carrier
The right truckload carrier will have the solutions and expertise needed to navigate any obstacles the holiday rush brings. Here’s a list of things to consider to ensure your chosen provider is equipped to work through labor shortages, weather challenges and demand increases.
Capacity. During this hectic busy time of year, it’s essential that carriers can handle increased shipping volume while maintaining the integrity of the perishable goods they’re transporting. Look for carriers with a proven track record of scalability and flexibility in accommodating seasonal spikes. What is their fleet size? Even if you only anticipate needing a set number of trucks, do they have additional capacity should your needs change?
In addition, what other capabilities do they have beyond refrigeration? What is the track record of goods being transported at the optimal temperature ensured by the carrier?
Reliable equipment. Reliable, temperature-controlled equipment is non-negotiable when transporting perishable goods. Make sure you’re working with a carrier who invests in well-maintained equipment. Ask them about their fleet, the age of their trucks, what technology they employ to maintain refrigeration and how they ensure regular maintenance and adherence to industry standards. What is the carrier’s track record in ensuring goods are transported at the optimal temperature? Find a carrier who prioritizes the integrity of your products.
Clear communication. No matter the occasion or season, work with a carrier who is accessible and communicative. A reliable partner will provide real-time updates on the shipment status, potential delays or unforeseen challenges.
In addition, it’s important to ask the specifics behind their communication styles. Do they connect mainly via phone or email? Do they have a mobile-friendly platform you can access on the go? With people often away from the office and home during the holiday season, how easily can you access the people and information you need at any given moment?
With accessible and real-time communications, you can easily make informed decisions to mitigate risks and optimize delivery schedules.
Adaptability and problem-solving skills. Staffing shortages are challenging during the holiday season as people take time off to celebrate the season with friends and family. Your carrier partner should work with you to find creative ways to overcome the obstacles of a limited staff. This might include timing delivery to match a particular employee’s receiving schedule or coordinating to find a professional driver to assist with unloading.
In the event there’s a delay in shipment, your carrier should not only be communicating with you in real-time, but they should also be working with you to solve problems. A collaborative approach to troubleshooting helps ensure both parties can work together seamlessly and meet delivery expectations.
A carrier with contingency plans for seasonal staff shortages and a proactive approach to real-time problem-solving helps keep deliveries on track and running smoothly.
Going beyond technology in forecasting. With the rise of AI and data-driven solutions, it’s essential to ask what abilities a carrier has to forecast and predict how weather, fuel costs and demand will affect your shipments. In addition to tech-based solutions, which are table stakes with transporting temperature-controlled freight, a carrier with years of experience in shipping temperature-controlled products can provide recommendations and insights based on familiarity with the nuances of the season.
Finding the right carrier partner to work with you during the holidays is critical for success. Ultimately, it all comes down to experience. How familiar are they with managing refrigerated shipments during this challenging time period? Do they have the right equipment? Asking the right questions upfront will help save you potential headaches in the future.