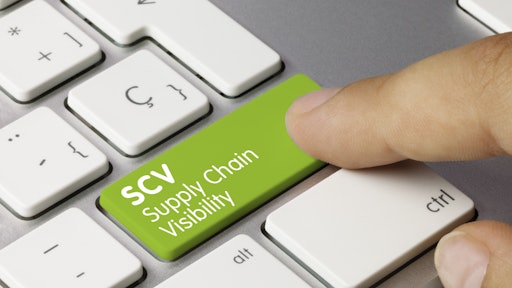
In recent years, the food and beverage industry has faced unprecedented challenges, such as supply chain volatility, workforce availability, retention, skills gaps and high turnover rates. Additionally, new and evolving regulations, like the Food Safety Modernization Act, demand that manufacturers collect, organize and report detailed information at every step of the process to ensure consistent monitoring of quality and compliance standards. In an industry increasingly relying on data, digital transformation and the adoption of automation and system integration have become crucial for growth and maintaining competitiveness while adhering to regulations.
End-to-end visibility is key
End-to-end visibility - having comprehensive oversight of the entire supply chain, from sourcing ingredients to production lines, suppliers, partners, and distributors - is key to efficient operations in modern food and beverage companies. Without such visibility, companies may lack essential insights into their operations, supply chain and supplier relationships, which can lead to disruptions, shipment delays, inefficient inventory management, and procurement and production issues, ultimately compromising quality and safety standards.
Given the time-sensitive nature of goods in the food and beverage industry, maintaining visibility across all business processes is paramount. This includes not only tracking inbound logistics for raw materials but also ensuring real-time visibility on the fulfillment side. For instance, in the event of carriers experiencing delays resulting in spoiled products, real-time visibility can swiftly identify the issue, enabling adjustments to avoid inventory and shelf-life problems and potential revenue losses from customers.
Importantly, the supply chain process directly interacts with food in many areas, posing potential health hazards. Failing to track and monitor the entire supply chain can increase the risk of unnoticed quality and safety issues until they escalate into significant problems. According to the U.S. PIRG Education Fund, "the Centers for Disease Control and Prevention (CDC) estimates that nearly 50 million Americans become ill every year from contaminated food or beverages. Among those, 128,000 end up in the hospital, and 3,000 die."
Food and beverage recalls not only threaten public health but also cause significant disruptions to the business operations of the companies involved. Let's consider one recent example: the June voluntary recall of more than 20 varieties of frozen, pre-cut fruit products suspected of contamination with Listeria monocytogenes. Three companies produced and sold these products under various brands in over 20 grocery chains. Despite being voluntary, the recall was still a huge undertaking. To competently, quickly and safely address these incidents, manufacturers must track batch identification and destination, generate alerts and establish procedures for a return to accurately resolve any recall issues.
Supply chain volatility poses another challenge that a lack of visibility can complicate, as demonstrated by Russia's recent withdrawal from its grain export deal with Ukraine, which both highlights and contributes to the instability in global food supply and price security. In the food and beverage industry, it is critical to support dynamic relationships and have visibility into supplier and logistics partners and processes to quickly adjust to political instability, weather, and other factors that can rapidly challenge a company's ability to produce and fulfill goods.
The benefits of automation and integration
To stay ahead of business challenges, food and beverage companies must prioritize automation and the integration of manufacturing and supply chain systems. They can achieve this by implementing end-to-end automation and consolidating all electronic data interchange (EDI), application programming interfaces (APIs), and non-EDI integrations onto a single platform. This approach connects and automates processes to streamline operations, reduces errors, and enhances efficiency throughout the supply chain network. It offers real-time visibility and intelligence, empowering businesses to proactively address potential threats, identify the origins of hazards, and ensure the delivery of high-quality products to consumers.
Establishing a clear line of sight and connectivity across manufacturing and supply chain systems enables food and beverage companies to dynamically manage partner relationships, such as suppliers, logistics partners and warehousing providers, through a single-threaded relationship. The enhanced supply chain intelligence and awareness facilitate swift adaptations, onboarding and transitioning between partners for different processes in response to delays or unforeseen issues. A platform that facilitates rapid onboarding and dynamic partner management significantly reduces customer onboarding times, thereby improving time-to-revenue as well.
While not all manual processes can, or should, be removed, there are several ways food and beverage businesses and manufacturers can automate and integrate the manufacturing and supply chain ecosystem to reduce friction and meet customer demands:
• Integrating legacy systems. Integrating legacy systems can be a complex task, involving manual interventions and custom scripts to adapt to evolving business rules and processes. This complexity grows when dealing with large, diverse partner ecosystems. However, by moving legacy coding processes into an integration layer and leveraging cross-reference tables, food and beverage companies can simplify the integration of multiple scripts into enterprise resource planning (ERP) systems. This streamlines the accommodation of partner business processes and requirements, reducing friction and enabling automation and standardization of internal systems and processes.
• Accelerating e-commerce, omnichannel or marketplace initiatives. Embracing e-commerce is essential for success in the digital world. To accommodate additional sales channels and growth, ecosystem integration through a single platform for file-based EDI and application integration becomes crucial. This platform allows businesses to optimize end-to-end integration processes within a dynamic network of trading partners, applications, suppliers, customers and digital marketplaces. With a unified platform, automation opportunities can be identified, manual intervention can be eliminated, and critical processes across the supply chain can be streamlined.
• Sync critical data between applications. Manually updating data between applications can lead to data inaccuracies, impacting business analytics and decision-making, and is becoming less compatible with modern business practices. To address this, modern API and EDI integrations are necessary, streamlining applications that were previously managed manually. By doing so, critical data is automatically synchronized between applications in a single source, eliminating the need for dual manual entry or batch processing.
• Migrate to a post-modern WMS/TMS/ERP system. Migrating and modernizing old ERP, warehouse management system (WMS) and transportation management systems (TMS) can be challenging, particularly when custom code from the past hinders progress. Adopting a strategic phased approach to modernization can help. Beginning with the introduction of a comprehensive visibility platform, embedded native systems can be unwound, and backend legacy files can be migrated into a new system in conjunction with onboarding supply chain partners.
In summary
Implementing automation and system integration in the food and beverage sector enables the real-time data and end-to-end visibility required for the comprehensive monitoring and analysis of production processes, supply chain logistics and inventory management. Automated systems and processes are less prone to human error and can help to ensure consistent quality in food and beverage products. The ability to accurately track the origin, processing and distribution of products also enables faster recalls should problems arise, supporting compliance with food safety standards.
Leveraging technology to streamline supply chain connectivity, mitigate challenges and disruptions, comply with regulations, and drive quicker decision-making all support more informed business strategies for food and beverage companies, ensuring efficient, safe and competitive operations.