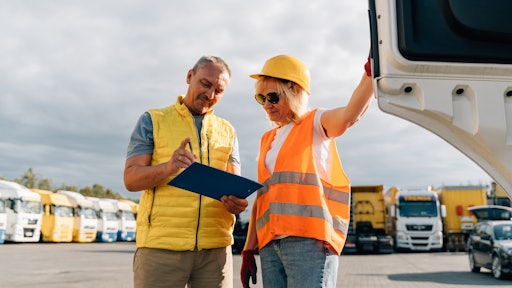
The food supply chain can be hazardous – at the farm, processing plant, loading dock, and restaurant kitchen line.
According to U.S. Bureau of Labor Statistics data, in 2021 there were 253,100 workplace injuries and illnesses in transportation and warehousing, 196,400 in foodservices and hospitality, and 43,500 in agriculture, fishing, forestry, and hunting. Tragically, there were also 976 fatal workplace injuries in transportation and warehousing, 453 in agriculture, fishing, forestry, and hunting, and 179 in foodservices and hospitality.
To curb workplace injuries and fatalities, government regulators such as the U.S. Occupational Safety and Health Administration (OSHA) have been ordering up new workplace safety initiatives, such as the Hazard Communications Standard and a final rule to optimize data collection for workplace injuries and illnesses. But more regulations aren’t going to magically make the food supply chain safer.
Business leaders across the food supply chain need to elevate their worker safety programs – above and beyond compliance – to reduce accidents and injuries and ultimately save more lives.
Ensuring worker safety – A tall order for the food supply chain
Business leaders at every stage of the food supply chain are responsible for ensuring the safety of their workforce. But without the proper programs, processes, and technologies in place, it’s nearly impossible for managers to safeguard dozens, hundreds, or even thousands of geographically dispersed workers.
Leaders must ensure company compliance with OSHA laws and regulations and alignment with internal environmental, health and safety (EHS) policies. Companies with a large workforce comprising full-time, part-time, contingent, and contract workers, plus service providers and vendors are especially challenged. They must also adhere to local labor and workplace safety laws and regulations for each labor category in each country, region, and industry in which they operate.
Overcoming worker reluctance to adhere to EHS policies and best practices also challenges leaders. While safety compliance is vital, it's often seen as cumbersome and can increase employees’ workloads. Policing these policies can also be laborious, intrusive, and uncomfortable. Yet, the fallout from ignoring rules, cutting corners, and neglecting oversight can be catastrophic.
For companies operating in the food and hospitality industries and those that fuel and replenish them, EHS audits are a recurring mandate. The size of the company's global presence and the extent of its auditing team can significantly influence the likelihood of overlooking safety, regulatory, and compliance policies, potentially resulting in serious incidents or fines.
However, complying with laws, regulations, and mandates is the bare minimum for companies operating within the global food supply chain. Leaders need to go above and beyond driving compliance to ensure greater workplace safety. The optimal approach fosters a culture of workplace safety and blends its EHS programs and processes and advanced technologies. It’s an approach that workers can get behind, too.
A workplace safety trio: Culture, processes and technologies
Business leaders can overcome these challenges by fostering a culture of workplace safety, establishing policies and processes that drive compliance and safer outcomes, and investing in advanced technology. This holistic approach to EHS will save lives.
Step 1: A culture of workplace safety
The focal point of an EHS program ought to be the people it’s intended to protect. Thus, every stakeholder in the food supply chain, from farm to fork, should be and feel heard. To secure buy-in on EHS policies and processes, start by soliciting feedback and listening to ground-level perspectives. Ask employees:
● What safety protocols and business applications are effective, or ineffective?
● What’s hindering workers’ ability to complete their jobs – processes or technologies?
● What do workers need to be safer and more efficient in carrying out their work?
Leaders should also make their workforce feel they are part of the solution – not a part of the problem. A workforce excited to improve workplace safety and empowered to positively influence working conditions will be more effective than one that feels they are merely checking a box to comply with OSHA/EHS policies and regulations.
Step 2: EHS processes
The next step for business leaders across the food supply chain is to develop EHS processes that exceed OSHA standards without making workers’ jobs much harder – or hard at all. Finding that balance can be tricky.
An engaged and personally invested workforce that partners with leadership can develop or refine best practices and policies that not only comply with OSHA standards, but also reduce incidents, accidents, and fatalities significantly. Consider the following:
● What EHS policies and processes do industry leaders implement? What’s worked?
● Where have other companies struggled or failed? What can you learn from them?
● How can you scale EHS across the supply chain to protect more stakeholders?
Step 3: Advanced technologies
The final step to enhance workplace safety features next-generation technologies, such as AI-enabled mobile applications and unified EHS platforms, that help stakeholders across the food supply chain to manage safety and reduce incidents. After all, fostering a culture of workplace safety and establishing and enforcing EHS policies and procedures across large, dispersed workforces is impossible without the right technology in place.
AI-enabled video analytics autonomously detect and report workplace accidents (or near-accidents) and facilitate further analysis and record-keeping. Advanced analytics enabled with machine learning algorithms sift through extensive datasets, identify potential safety concerns, and deliver actionable insights to business leaders. Predictive analytics also leverage machine learning algorithms to uncover safety trends, surface insights, and help teams prevent accidents.
Front-line workers can use mobile applications enabled with natural language processing to immediately report unsafe or unsanitary working conditions, accidents, and near misses. The conversational interface streamlines safety-incident reporting. Workers can also use AI-enabled applications to directly share feedback with leadership on the effectiveness of EHS policies and practices and the vision they may have for a safer work environment.
Unified EHS platforms bring all the pieces together via a common user interface that facilitates seamless data and process management across diverse business units. They empower teams to efficiently collect, store, reference, and share safety data and insights – internally and with regulatory bodies – to drive comprehensive safety and compliance efforts. EHS platforms are a must-have solution for businesses with an EHS program.
A safer food supply chain benefits everyone
Business leaders across the food supply chain – including restaurateurs, wholesalers, shippers, plant managers, and farmers – have a responsibility to their diverse worker base to create the safest working environment possible. Business leaders can meaningfully reduce workplace injuries and fatalities by engaging stakeholders to shape a workforce safety culture and giving them agency and technology to develop and refine processes.
By taking a tech-powered approach to improving worker safety, business leaders can create a safer experience for all stakeholders in the food supply chain.