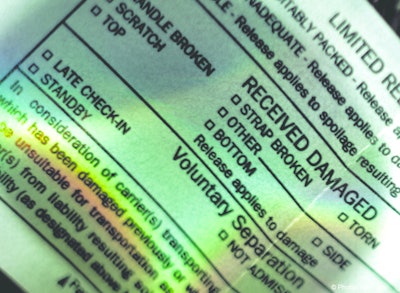
When recalls occur, the best response is a prepared one. But recognizing risk in your business and preparing contingencies is powerful and bears a direct impact on how well you respond and recover, according to Steve Dollase, president at Inmar Supply Chain Network, writing in the January/February Food Logistics.
Every consumer-goods company should plan for these contingencies, particularly in the food industry, where the potential impact to consumer safety and brand equity has far-reaching implications, Dollase writes.
Many companies do take some measures to reduce recall risk, implementing strong quality controls and even positioning quality as a brand differentiator. But, more is required. Think about these external factors that led to high-profile recalls:
- A plant in China that turns out to use paint with cadmium content on a product used by children to consume liquids.
- Dog treats produced overseas that turn out to have ingredients toxic to dogs.
Striving for best-practice quality, with safety baked in, isn’t the whole picture. There is more complexity to contend with, not the least of which are global manufacturing and supplier bases providing raw materials and ingredients for your products. You can impose and monitor quality standards with vendors and suppliers, but measures must be taken to plan for the defects that are outside of your direct control…those low-probability, high-impact events like product recalls.