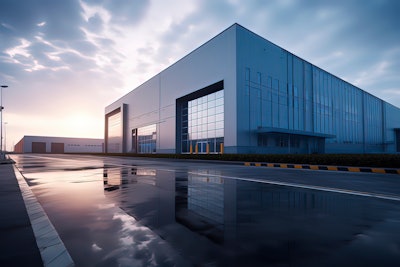
“Hey, it fell off the back of a truck…”
While this statement has been uttered sarcastically by everyone from movie mobsters to Homer Simpson, it is no laughing matter to manufacturers, shippers and logistics executives.
According to CargoNet, “supply chain risk events” (aka, cargo theft) increased more than 15% last year, with an estimated $223 million stolen across the U.S. and Canada in 2022. As in previous years, warehouses and distribution centers were the most targeted locations and large trucks the most targeted vehicle type. CargoNet's 2022 data shows that theft events involving a heavy commercial vehicle such as a semi-truck or semi-trailer increased by 17% from 2021 to 2022, with the average value of cargo stolen $214,104.
Much of this increase is due to fictitious pickups in which a shipment is subcontracted to a legitimate carrier and then misdirected to another address. However, an increasing number of thefts are also happening in warehouse yards and around loading docks. One common practice that puts companies at risk is when the security seal on a trailer is broken—or put in place by non-company personnel—on the drive approach. Since security or surveillance may not be as present there as it is inside, goods can more easily be stolen.
In some cases, even trailers that have backed into the loading dock may be at risk, particularly if they are not fully secured—which is a common problem with liftgate trailers, trailers with obstructed rear-impact guards (RIGs) and intermodal containers. In such cases, thieves may be able to tamper with the restraint, gain access to the trailer, and make off with valuable cargo.
This article will examine ways that warehouses and distribution centers can more effectively secure their loading dock areas to prevent cargo theft, while also improving employee safety and energy efficiency.
Automatic Vehicle Restraints: The First Step in Cargo Security
The first step in improving cargo security at the loading dock is to install vehicle restraints that automatically secure a trailer or vehicle when it backs up to the dock. While automated vehicle restraints are often viewed as a safety measure to thwart trailer separation accidents, they are an often-overlooked component of cargo theft and contamination prevention. Automatic vehicle restraints not only present a visual and physical barrier to thieves, they can also be integrated into building management or security systems, providing another level of security. Leading automatic vehicle restraints will also re-fire into a locking position if the trailer begins pulling away from the building or the locking mechanism is tampered with.
Rotating hook-style restraints, which secure a trailer by wrapping around its RIG, are the most common type of automated restraint. They work well with traditional OTR trailers, but don’t always work with other vehicle types. However, a new type of RIG-based restraint has been recently developed that provides a wider range of vertical engagement (8½ inches to 30 inches) and can handle a broader variety of trailers. These vehicle restraints feature a double jointed “shadow hook” design, which rotates to connect in a secondary location and lock in the event of early departure. This secondary point of entrapment makes them able to help secure nearly any type of trailer to the loading dock wall, including intermodal cargo trailers, trailers with obstructed RIGs, as well as new, reinforced pentagonal RIG trailers.
Vertical Levelers and “Drive-Thru” Dock Design
Vertical storing levelers are another important upgrade that facilities can make to enhance cargo safety and security. Unlike pit-style levelers, vertical levelers (when in the stored position) allow the loading dock door to close directly on the pit floor, rather than the leveler itself, minimizing points of entry at the loading dock. This helps maintain security and improve environmental control. The vertical design makes it easy to clean or wash down the pit floor when the leveler is in the upright and stored position, as well.
Vertical levelers are the key component in a “drive-thru” style loading dock. Once a rarity, drive-thru docks are becoming increasingly common, and for good reason—they are considered the gold standard for cargo safety and security. They differ from traditional loading docks as they allow for trailer doors to be opened into the facility, rather than on the drive approach. This ensures that the trailer’s security seal is inspected and cut inside the dock, minimizing the opportunity for cargo theft or tampering, as well as outside air intrusion. A drive-thru design effectively makes the semi-trailer an extension of the facility. In addition to enhancing cargo security, this design minimizes energy loss and reduces moisture intrusion (and thus slip hazards). Perhaps most importantly, it keeps workers inside the dock and “boots off the ground” on the dangerous drive approach outside.
Drive-thru loading docks typically have a continuous recessed pit. Their defining feature, however, is a vertical leveler interlocked via a control system into a system of dock equipment including the dock door and automatic vehicle restraint. Sensors in the pit, as well as a push-button control mast help ensure the pit area remains safe for workers when the leveler is stored in a vertical position. Drive-thru docks also need a dock shelter or seal compatible with the vertical leveler.
Loading Dock Control Systems
State-of-the-art dock control systems can interlock these pieces of equipment and program them to function only in a safe sequence of operations. This capability is an important leap forward in both safety and security, especially for facilities with inexperienced employees. For example, when interlocked properly, the hydraulic leveler and overhead door are disabled until the vehicle restraint is safely engaged. Once the vehicle is secured, the overhead door can be opened, the dock barrier released, the trailer seal cut, the trailer doors opened and the leveler extended into the trailer bed. After loading/unloading, the restraint is not allowed to disengage the trailer until the leveler is taken out of the trailer and stored safely. This “safe sequence of control” programming helps to eliminate the potential for human errors in operating equipment throughout a dock station.
The leading dock control systems now come with a real-time trailer presence monitor, which provides a camera view of the exterior vehicle restraint. In addition to letting workers inside see when engagement takes place between the vehicle restraint and the trailer, the live camera view will also show if anyone outside is trying to tamper with the locking mechanism–taking security and safety to another level. A secondary camera can be added to show a live view of trailer nose stands on dropped trailers. These control systems and cameras can also be used with leading wheel lock restraints, to alert employees inside if anyone is tampering with the vehicle restraint or it has become disengaged.
While these types of loading dock control systems are often associated with a drive-thru dock set-up, they can work with multiple types of dock designs, including traditional pit leveler docks or wheel restraint docks as described above. The key is to have a “new generation” vehicle restraint that is smart connected, can be interlocked into a control box, and is compatible with building management and security systems.
Properly Sealing the Dock Perimeter
The connection of a dock seal or shelter between the back of a semi-trailer and the inside of a dock provides a barrier to keep wind, rain, dust and other contaminants outside the building. Besides environmental and energy saving benefits, this also contributes to theft deterrence by sealing gaps that could otherwise be passageways for thieves to move product.
Foam compression dock seals or full-access dock shelters that seal trailer door hinge gaps, along with a full-coverage, under-leveler sealing system are recommended in most applications. Some of the newest dock shelters have been specifically designed for drive-thru applications. They allow the trailer doors to be opened inside the building, while still maintaining a tight, consistent seal on all four sides of the trailer.
Protect the Supply Chain at the Loading Dock
In almost every instance, the best way to secure a loading dock is through a systematic approach that incorporates automatic vehicle restraints, vertical dock levelers, appropriate seals/shelters and the proper sequence of operation. By integrating these pieces of equipment and making sure they work together as a system, facilities can greatly enhance cargo security, protect employees, reduce contamination and improve energy efficiency within the building and throughout their supply chain.