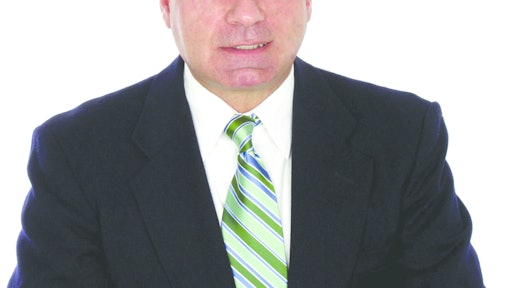
An efficient perishable supply chain and transportation network is a key component of good, fresh foods and will continue to be a key topic of concern. Long transit times and poor handling lead to spoilage and waste, not to mention potential foodborne illness. Out of the some 400 billion pounds of foods produced each year, 100 billion pounds are spoiled and wasted. Waste creates a new set of environmental issues as food waste converts into water waste and a host of GHG emissions.
With double digit increases in the consumption of perishable foods, it is crucial to reduce time-to-market. Reducing time-to-market means less cost, reduced energy and fresher products for sale. This calls for innovative logistics strategies, which will help improve quality by optimizing shelf life and increase revenue and profit.
Speed-to-market and reduced costs are not a given. There are several forces driving new thinking about faster, more efficient perishable transportation. The ever tightening refrigerated transport capacity, driver shortages, CSA 2010, stricter hours of service mandates for drivers, and equipment shortage are all contributing to a “reefer” transport segment that is in a state of tension. In addition, shippers are increasing pressures to reign in rates and are asking for tighter in-transit quality controls.
When we combine this with expensive oil, which is undoubtedly here to stay, speed-to-market at less cost seems to be conflicting objectives. After all, oil consumed in the U.S. is the source of more than 97 percent of transportation energy (70 percent of all consumption). The transportation sector contributes almost one-third of GHG emissions.
As an industry, we are becoming more creative in solving our own food logistics and product quality challenges while being more socially responsible. We are slowly seeing adoption of transportation policies with the expressed intent to improve transportation systems, energy efficiency and reduce GHG emissions. This leads us back to the strategic use of ports and rail in expediting perishables to market using less fuel. We know, for the most part, intermodal fleets can move a ton of freight nearly 500 miles on a single gallon of diesel fuel, which is about four-times more efficient than an over-the-road truck.
However, a downside of rail is one unit of NOx produces 310 times the global warming effect of one unit of CO2 (which is the GHG normally tracked in carbon comparisons). The EPA-mandated 2010 truck rules virtually eliminate NOx for newer truck engines. The pinch-point is the differences in the regulation of truck and rail diesel engines. Currently, rail locomotives emit an average of 4.5 times more NOx per horsepower-hour than a over-the-road truck engine. Locomotive emission improvements are on the way. For now, rail continues to eliminate thousands of horespower hours through express trains.
But, let’s neutralize the CO2 benefit of rail. We cannot ignore the use of express trains in reducing time-to-market, less energy requirements, and the reduction of food waste. With that noted, the use of customized express unit train solutions will become more common. Aside from reducing network miles, better time-to-market, less highway congestion and more responsible fuel consumption, further benefits are realized when ocean carriers, more efficient ports, and innovative rail solutions are orchestrated for an integrated food chain. In selected cases, transport costs have been reduced by as much as 50 percent with a faster speed-to-market (30 percent less time).
As a veteran of the food industry, 50 percent improvements reside in the world of fantasies where most managers would dismiss the possibility of such huge savings. But, fantasy has turned into reality. A newly started express train service is launching one of the most innovative uses of ocean vessel to port to express train to in-land hub to truck strategies designed to reduce sailing times of ocean vessels (reducing a day of ocean vessel sailing time converts to about $100,000 per day). As counter intuitive as ocean and rail sounds, the puzzle pieces are now ready to be put in place with new ways in viewing the use of ocean vessels, ports, express trains and well situated logistics parks. The logistics strategy also works in reverse. In other words, what works on the inbound side for one shipper works, in return, as an inbound for another shipper.
When all the components of the supply chain are considered, the combination of a well placed port, the more efficient use of ocean vessels, the use of an express train feeding inland logistics hubs and shorter truck routes to customers realize sizable cost savings and reductions in time-to-market. As with any strategy, it must start and end with the customer in mind. The proper use of supply chain components adds significant value to customers as it means fresher products in stores for longer times thus maximizing optimal quality sell time creating more revenue, increased profit, and less waste.