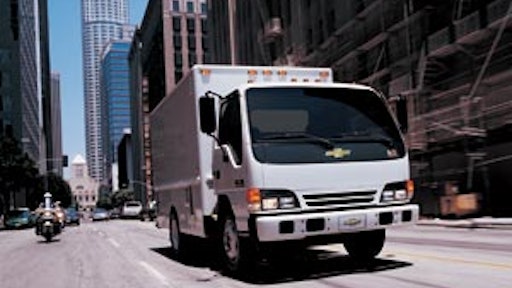
In food service, as product moves through the supply chain, it would be much more efficient for all parties to reference a product based on a single barcode given by the label's owner. That product could be ordered by distributors and their customers using that code, and be billed to all parties using that same code. There would be no need to put additional stickers on each product, or license plates on each pallet. Each member of the supply chain could use that one code to uniquely identify the product from the time it leaves the manufacturing facility until it reaches the restaurant kitchen.
Unfortunately, food service today does not always operate that way. Despite steady progress, the industry must make more aggressive strides in the use and quality of barcodes to achieve real supply chain efficiencies, according to sources all across the foodservice channel.
"A critical mass of companies using barcodes is needed to ensure better tracking of products from manufacturer to end user, reduce invoice discrepancies, enable more accurate communications and facilitate the electronic capture of company and product information," says Mark Allen, president of the International Foodservice Distributors Association, based in Falls Church, VA, and the former executive director of Efficient Foodservice Response (EFR), a broad-based foodservice industry initiative aimed at studying, piloting and recommending business processes to make the channel more efficient.
As early as the late 1990s, EFR advocated 100 percent case coding on at least two adjacent sides with a standard product identification barcode. But despite efforts, current research suggests that of the items that have barcodes, only 70 percent have barcodes on two sides. As for barcode quality, only 82 percent of cases and 74 percent of inner packages can be scanned accurately.
Worse than that, many say, is a lack of barcoding altogether that is still prevalent within the foodservice industry. Case coding among foodservice manufacturers currently stands at about 85 percent—up dramatically from 54 percent in 1999, but still quite a ways off from the goals originally laid out by EFR.
EFR's research has found that product-level coding varies among product categories, mainly because the industry is prone to a lot of disparate catch weights and variable weights. "You can get uniform case counts in dry and canned groceries, but you just don't get that with fruits, vegetables and meats," Allen says.
Coding also varies among supplier types. The larger companies typically do barcoding well, while smaller local or regional companies do not, reports Phil Graff, director of operations at Yancey's Foodservice, Loveland, CO, which ships to 1,500 foodservice customers in Colorado, Nebraska and Wyoming from a 100,000-square-foot warehouse. Companies like Tyson Foods, Springvale, AR, and Rich Products, Buffalo, NY, have been fairly consistent with barcoding.
Officials at Tyson claim that all products leaving its facilities have either Interleaved 2 of 5 (ITF) barcodes, chosen as the standard for outer cartons, or EAN-128 barcodes for variable weight products. ITF barcodes, also known as Global Trade Identification Number (GTIN) codes, include 14 digits that represent country code, manufacturer number, product number and check digits, while the EAN-128 code offers a higher density with the entire 128-character set to also include things like dates, batch numbers, weights, quantities and product dimensions.
"We have adopted the standard barcode technology and are using that on all shippable products going to our customers," says Lela Tripp, director of customer service and business development at Tyson.
Rich Products makes the same claim. Since adopting the barcoding standards, it has reported an inventory accuracy rate of better than 99 percent, lower labor costs, inventory reductions and better recall management.
It should come as no surprise that both companies were early pioneers in EFR barcoding tests and pilots, but those companies aside, many distributors report that at least 15 percent to 20 percent of all products coming into their warehouses do not have barcodes of any kind.
"We get products all the time that don't have any barcodes," says John Brusie, systems administrator at Cash-Wa Distributing, Kearny, NE, which supplies more than 3,500 accounts in the Midwest. "Then we get some vendors that send some items with barcodes and some without."
Still other products come in with multiple barcodes. "Between pallet, case and individual item, we can have three different barcodes for the same product," Brusie also notes.
Barcoding is also inconsistent from one supplier to the next. "It has been painfully clear that members of the foodservice industry have different ways of identifying product," says Allen. "Some suppliers use the GTIN, some use their own internal number, some use the distributor's number and still others use the operator's number, all to identify the same product."
The industry has pretty much settled on the GTIN as the standard, but adoption has been another thing. According to Jim Lavender, executive vice president of purchasing and marketing at Ben E. Keith Foods, Fort Worth, TX, some companies at one time "were talking about 30- or 40-digit codes to contain all kinds of information that they may or may not need."
Adds Susan Boyme, a product marketing specialist at Retalix, "The standard is out there in the GTIN. ERP and WMS systems are ready, it's just a matter of getting all the parties together to use it.
Retalix, which offers WMS and ERP solutions, is GTIN-compliant and trying to promote its use among its customers, says Boyme. "If you're still waiting, you're missing out on a lot of the efficiencies that you can achieve."
Prone To Errors
This lack of barcoding—and inconsistency in barcoding—is being seen by distributors as a main reason for a high level of errors on inbound freight. Current estimates place accuracy levels at just 89 percent on inbound freight received from suppliers.Today's processes also contribute to an increase in database errors, incorrect orders, shipments and invoices and an increase in invoice deductions.
"As members of the supply chain communicate with each other, each must cross-reference its product number with the other party's product number. As each function within a company uses this process, the chances for errors increase," Allen explains. "As your communications about that product increase with additional members of the supply chain, the chances for error further increase."
Those errors typically result in a back order being issued, but at least 60 percent of those back orders are later cancelled as distributors and operators look elsewhere for the products that could not be delivered on the first pass.
EFR analysis, however, shows that 63 percent of manufacturer errors and 21 percent of distributor errors could be eliminated with item, price and promotion data synchronized across a common barcoding format. The same data places the potential for savings in food service at between $847 million and $1.1 billion a year through streamlined transportation and handling, reduced invoice discrepancies and deductions, accurate contract pricing, improved trading relationships and more productive use of employees' time.
This last point—worker productivity—is perhaps the single greatest benefit to be gained, say experts and industry insiders alike. For one thing, the lack of a single standard has forced manufacturers, distributors and end users to create databases of all the different product identification numbers, or to pay a third party to create and maintain those databases. That is extra work that could be avoided.
"When we have no barcode, we have to cross-reference it through our system with a product description, and we try to give it an item number based on that description," says Cash-Wa's Brusie. "It's often difficult for us to cross-reference products across all manufacturers."
Then, distributors have to assign all products that arrive at their receiving docks unique pallet-level, barcoded license plates. Those codes, usually generated by their WMS solutions, contain unique product IDs, date stamps, storage locations within the warehouse, expiration dates and more.
"When we bring a pallet in, our WMS attaches a license plate to it. The WMS then directs put-away and knows what's on the pallet, where it is and its shelf life and can tell us when it's best to pull it and ship it," says Ben E. Keith's Lavender. "Then when we pick a case, we put our own special barcode on that case."
These steps are being repeated at distributorships all across the country. "Our WMS tracks pallets by the license plates we create. We have to track everything by pallet, not barcode, because about 15 percent to 20 percent [of all products in Yancey's inventory of about 4,000 SKUs] comes in without a barcode," says Graff. "We do it for everything that comes in because it's a lot easier than trying to do it for some products and not for others. The labels are just for our use, and products probably get another set of labels at the restaurant. There's an obvious cost involved with it."
It's not incredibly expensive to do. "After all, it's just a sticker," says Lavender. "The real problem is the labor issue. All that scanning and placing labels on pallets and cases are still a lot of manual steps."
A universal barcode would eliminate the need to manually read and key information into systems, and cut the amount of time spent on correcting errors. It would also eliminate a lot of the duplication that exists now.
"There are other methods that some people are employing with their trading partners, but they're very isolated between the two companies, and then you have to go back and do it individually with all of the other companies you do business with," says Jeff Smith, vice president of marketing at Instill Corp., Redwood City, CA. "There's also some drift in the way those codes are used, so you have to go back into the system and update them every few weeks."
Mergers and acquisitions in the industry have also created havoc on those fronts. "The 50 largest foodservice distributors account for 50 percent of all foodservice sales. They continue to grow through acquisitions, and will continue to do so," says Paul Pretko, industry principal for wholesale distribution at software firm SAP. "With each acquisition, you have different software and applications that those companies could have. At the end of the day, you could have eight or 10 different software packages in one company."
Different Than Retail
Just about everyone in the foodservice industry would agree that the retail grocery industry is far more advanced in its use of barcoding, mainly because barcodes are a much more critical component of the overall sales equation. In retail, barcoding travels with the product all the way to the point of sale, providing retailers with the basis for dozens of decisions related to pricing, ordering, forecasting, demand planning, category management, shelf placement, packaging, marketing, promotions and more. That's not something that foodservice operators face to the same degree, Allen says.
"Also, in retail, with data synch and a standard barcode, there's been a tremendous benefit in cost efficiencies needed to compete against Wal-Mart," says Boyme. Most foodservice outlets do not have that kind of competition.
"There are great similarities between food service and retail, but the business processes are much more complex in food service and that can lead to much more complicated data flows," adds Smith. "There are 30 different types of trade funds programs—spending by manufacturers to boost sales—and there are all kinds of deviations to that. A deviated price is something you almost never see in retail.
"The obvious answer to overcoming that is to reduce the complexity of the way companies interact, but changing the way people do business is not something they do easily," he says.
Delays in full-out barcode implementation in food service are also being fostered by uncertainty among smaller firms about the value of investing in barcoding equipment. "Companies like ours would love to see it in food service, but the compelling value proposition is just not there," says SAP's Pretko.
"Food service has very much taken a wait-and-see approach. The solutions are ready to adopt it, but there needs to be a proven ability to capture ROI before the industry goes forward," Retalix's Boyme adds. "I think it will really help promote standards if companies can prove that they can effectively track products through the supply chain while removing costs and increasing accuracy beyond just scanning."
In some cases, manufacturers do not want to invest in printers and labeling programs until they know their distributors are equipped to read the labels properly, and distributors do not want to invest in scanners and other technology until they are sure that their suppliers can properly apply labels with the correct information.
Even among those that did make the investment, the decision has been made with some trepidation. "By the time we get everyone on one standard, the technology and platform will be outdated," Brusie fears. "Everyone will move away from that standard and something else will come along to replace it."
Radio frequency identification (RFID) tagging is one such technology that has fueled those fears. There's no reason to fear, says IFDA's Allen. "The recommendation was for barcoding, and that has not changed," he says. "The carrier can change, but the data structure will remain the same."
And, rather than replacing barcoding, RFID will simplify processes. "If we have scannable barcodes on all cases, with RFID we will not have to manually scan anything," says Ben E. Keith's Lavender. "With RFID, our computers would immediately know all there is to know about a pallet. It's the next step for sure."
"If every case on a pallet had an RFID tag on it, we would be able to break it down to a manufacturer and lot code automatically and pull information for it without having to manually scan it with a reader. It would make our life much easier," adds Graff of Yancey's.
"Distributors have realized that our systems will be much more efficient and accurate if we have 100 percent implementation of standard product IDs and barcodes," says Pam Tann, director of the Standards and Coding Group at Sysco Corp., Houston, the nation's largest foodservice distributor. "Sysco is committed to using codes to achieve supply chain excellence and we, likewise, need all of our trading partners to embrace these fundamental building blocks as well."