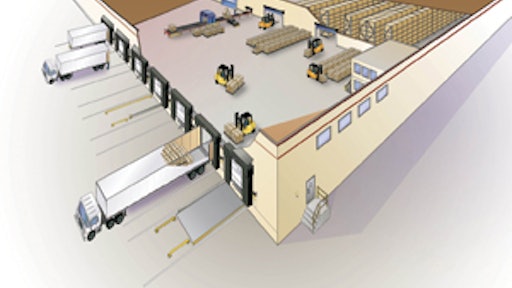
When is a loading dock not just a dock? The answer is now—because an efficient, productive loading dock provides a competitive advantage in supply chain logistics, which many agree is industry's new profit frontier. The fact is that businesses today can no longer think of the dock in isolation. Instead, companies will benefit by treating the dock as a part of a Material Transfer Zone (MTZ) that plays a critical role when working to improve speed-to-market.
The MTZ can be thought of as a valve that regulates the rate at which goods flow in and out of a facility. In this context, an efficient, productive loading dock becomes a competitive necessity. When everything flows smoothly, delays are avoided, accident potential is minimized, product damage is prevented, schedules are met and customers are satisfied.
The MTZ reaches from the drive approach well into the shipping/receiving/staging area. In the past, many simply thought of this area as the loading dock. However, the MTZ has evolved to become much more. As such, it presents facility managers with challenges and opportunities.
Complex Interactions Abound
In the world of supply chain logistics, profitability is largely achieved through efficiencies. The drive for supply chain efficiency increases the importance of the MTZ. Yet at the same time, the challenges associated with the MTZ have never been greater. In other words, the seemingly simple process of moving material between plant floor and inbound or outbound vehicles is not what it appears. Instead, it involves complex interplay concerning:
- Flow of trucks in and around the facility and loading dock approach;
- Material handling vehicles;
- Widely varied tractor/trailer types;
- Loads and load configurations;
- Loading dock door openings;
- Loading dock equipment selection; and
- Safety initiatives.
The number of factors that affect the MTZ continues to expand. These issues are further complicated by management schemes and various supply chain productivity trends.
Trucking is one area that is profoundly impacted by recent trends. Within the trucking industry, physical changes in trailers increasingly affect receiving and shipping efficiency. The overriding trend is toward larger trailer dimensions. To maximize interior space, trailer walls have also become thinner. Many dry trailers have as much as 101 inches of clear width inside.
Some trailer manufacturers have also introduced low-profile tires to squeeze out more cube space within the trailer. This allows the box to be six to eight inches higher while overall trailer height remains the same. Additionally, increasing numbers of trailers use air suspensions that are designed to minimize cargo damage and increase trailer life. This causes bed heights to fluctuate by several inches at the dock as loads are added or removed and as lift trucks move in and out.
Challenges Of Reconfigured Loads
As trailer dimensions have increased, shippers have reconfigured loads to take advantage of increased payload space.
In particular, 102-inch-wide trailers enable 48-inch-by-40-inch Grocery Manufacturer Association (GMA) pallets to be pinwheeled (turned 90 degrees) to increase the payload. If pallets are stacked two high and double pinwheeled (meaning two pinwheeled rows side by side) the total payload can increase by as many as 12 pallets.
Trailer widths aside, some shippers have opted for full-width loads to achieve fewer lift truck cycles and save time. Full-width loads may also travel on wood or plastic pallets, depending on the situation, or even specially designed racks.
Changes in trucks, trailers and loads can boost shipping efficiencies. Yet, they also create bottlenecks at the MTZ.
Mismatches Clog The Valve
Many existing loading docks are undersized or ill equipped to handle today's larger loads and wide range of trailer designs. Additionally, many new dock designs rely on outdated rules of thumb for dock height, dock leveler size and capacity, door opening size and dock-door sealing configurations. The result is a mismatch at the dock, which translates into a clogged valve in the supply chain.
Consider a 102-inch-wide trailer in position at a traditionally designed dock, filled to the rear sill with double-pinwheeled, 48-inch-wide pallets. Also factor in a foam dock seal with a 96-inch-wide overhead door, which is common at many loading docks. Pallet loads fill the width of the trailer, leaving virtually no maneuvering space.
A lift truck can remove the first loads (end loads) only by pulling them straight off. But this is difficult at best because the foam dock seal and door jam obstruct the load on each side.
Even with no dock seal, the building wall may interfere on one side or the other, unless the truck has backed in perfectly on center. If the forklifts can't remove the end loads, employees must unload those pallets by hand, wasting time and money.
More complications come into play when the same truck rides on low-profile tires because the trailer bed rests four to six inches below the typical 48- to 50-inch dock height. Lift trucks are now constrained by the walls of the six-foot-wide leveler pit, which doesn't allow for straight-in access to end pallets. As such, the lift truck must spend a great deal of time to carefully extract end loads.
The situation becomes even more difficult when double-pinwheeled and double-stacked pallets are involved. Now the upper loads cannot pass through the door opening and hand unloading is virtually unavoidable.
Other Pitfalls Lurk
Many additional pitfalls exist when servicing modern trailers with conventional dock designs. Drivers may violently strike the corner of the building wall when backing out of a trailer. Another example involves lift trucks servicing trailers with low beds (six to 12 inches below dock) by way of six- or eight-foot-long levelers. Drivers may face excessive platform slopes. As such, they must accelerate sharply when backing out with loads in order to make the incline, which causes load instability.
Other key concerns include dock shock and trailer drop, two safety issues that also slow productivity and create potential for product damage.
Dock shock describes jarring that occurs when a lift truck (stand-up walkie or forklift) crosses between the warehouse floor and the trailer bed due to the bumps and gaps that exist on traditional dock levelers. Trailer drop describes vertical trailer bed movement or "drop" that occurs with the weight of lift trucks traveling in and out of unstable trailers. The situation is compounded when trailers with air-ride suspension systems are involved.
Mismatched dock designs often present a number of significant problems. Unfor-tunately, these problems are magnified in a finely tuned supply chain that depends on the smooth flow of materials at all points.
Don't Abandon Safety
In any plant, safety must be a given and it's important not to put employees at risk for the sake of speed-to-market. It's also important to think ahead.
Safety and productivity are inexorably linked. If pallets are easily accessible with forklifts, manual work—as well as possible injuries— reduced. If forklifts can back out of a trailer without fear of crashing into a pit wall or running into trailer drop, driver confidence is gained.
If proper dock seals/shelters are in place, employees are protected from the elements and able to work efficiently. If dock levelers float to meet the bed of a trailer with air-ride suspension, product slippage and accidents related to steep grades are avoided. Additionally, the comfort level that a forklift driver has knowing a trailer is properly restrained cannot be overstated.
Facilities simply cannot afford to overlook the Material Transfer Zone when developing plans for an efficient and high-performance supply chain. The prudent strategy is to make wise choices in dock design and equipment today. Doing so provides relatively quick payback and a long-lasting solid return on investment.
Swietlik is customer relations manager with Rite-Hite Corp., Milwaukee. He has 25 years of experience in the material handling industry, with more than 20 years dedicated to the area of loading dock and door expertise.