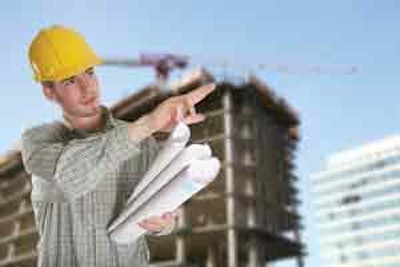
SECTION 1 / FACILITY DESIGN
Design A Blueprint For Sustainability
Start with an energy-efficient, environmentally-friendly facility.
By Carol Casper
Sustainability in commercial enterprise means economic development that is "ecologically viable now and in the long run," according to the Environmental Protection Agency.
The good news for the warehousing and logistics community is that business processes and investments which are ecologically viable also tend to be economically beneficial, often in the near-term and if not, then certainly in the long run.
Whether it's a matter of energy efficiency, building layout and design, or reuse of packaging wherever possible in manufacturing and distribution, approaches to operations which minimize an enterprise's ecological footprint also tend to provide significant returns on investment.
"Green leads to green," as the website of a leading reusable packaging supplier, ORBIS Corp., Oconomowoc, WI, proclaims. When it comes to environmental sustainability, you can do well by doing good.
The most effective way to build sustainability into an enterprise is to start at the beginning: with the design of energy-efficient, environment-friendly facilities and lean distribution networks.
But even existing buildings can be modified to reduce energy use and there are a host of operational decisions companies can make on a daily basis that will result in less use of resources and lighter demands on the environment, while at the same time improving not just a company's image, but also its bottom line.
"Anyone who's willing to make an investment in energy savings can find significant opportunities with very quick paybacks. It's economical to be green in both the long and short run," points out Mark Lowery, divisional vice president, refrigeration, for Stellar, Jacksonville, FL, an international, integrated firm focused on industrial design, engineering, construction and mechanical systems.
Many green buildings cost no more to build and may cost less than conventional alternatives, because resource-efficient strategies and integrated "green" design features often permit the downsizing of more costly mechanical, electrical, and structural systems, according to a report prepared for the U.S. Senate Committee on Environment and Public Works by the U.S. Green Building Council.
A nonprofit coalition of more than 3,000 companies and organizations from across the building industry, the USGBC promotes green construction practices and administers the LEED green building certification program, which stands for Leadership in Energy and Environmental Design.
In a pamphlet titled, "Making the Business Case for High-Performance Green Buildings," the USGBC enumerates 10 top reasons companies should "go green" in their facilities:
- In the event that upfront costs are higher, they can be recovered through lower operating costs;
- Integrating green design features lowers ongoing operating costs;
- Better buildings equate to better employee productivity;
- New technologies enhance health and well-being;
- Healthier buildings can reduce liability;
- Tenant costs can be reduced significantly;
- Property value will increase;
- Financial incentive programs are available for green buildings;
- Communities will notice your efforts.
In terms of trade-offs, Brian Hudock, partner with Tompkins Associates, points out that the only issue is the investment companies have to make upfront. They may pay an initial premium for energy efficient systems and materials, but in addition to showing they are good corporate citizens, companies will generally recoup their extra investment through lower energy and/or other operating costs within two to three years.
While cost-savings remains the most compelling argument for energy-efficient systems, people are growing more concerned about the environment and are increasingly motivated by an interest in environmental responsibility as well, adds Andy Saladin, a member of the senior engineering services team at ORBIS.
Key Opportunities
Planning for sustainable development starts with analyzing the requirements and realities of each business. For warehouses and distribution centers, the issues are less complex than with manufacturing operations, but that doesn't mean there aren't significant opportunities to conserve resources and become more efficient.
Hudock says that when addressing environmental concerns with warehouse clients, there are three primary areas Tompkins discusses:
- Facilities design;
- Equipment and equipment controls;
- Packaging, in terms of how product is handled and moved throughout facility.
"Among the first and easiest things to do is to address lighting in the building," he adds. "We try to use as much natural lighting as possible."
Increasingly, distribution centers are incorporating skylights to take advantage of sunlight. For companies that are concerned about roof penetration, sidelights—windows mounted high on the walls, just below the ceiling—offer most of the same benefit, Hudock notes.
Jud Walker, a LEED-certified engineer with Stellar, adds that companies are installing sensor controls to work in concert with skylights. The sensors detect the amount of ambient light coming through and automatically adjust the electric lights accordingly.
Companies can also install motion sensors to control lighting in different areas of the warehouse, so lights are only turned on when someone enters or accesses that area.
"These are especially effective for limiting unnecessary lighting in large storage areas deep in the warehouse," Hudock points out.
In terms of lighting technology, there has been a big push recently to develop fluorescent lights that are suitable for warehouse operations.
"With traditional, high-density warehouse lighting there's approximately a 10 percent energy loss. With fluorescent lighting, there's no energy loss," Walker notes.
The downsides of fluorescent fixtures are their lack of "quick-strike" capability, i.e. it takes time for them to turn on; as well as their inability to function in low-temperature environments.
Although temperature barriers remain, newer fluorescent technologies have recently been introduced that allow fast starts, making fluorescent lighting a good option for many dry warehouse facilities, even where motion sensors are used to turn lights on only as needed.
Walker says lighting manufacturers are also developing better ballasts for high-density lamps with less energy loss. However, presently these fixtures are still quite new and therefore expensive.
Another key consideration are the heating and cooling systems, especially for DCs operating any sort of cold storage, Hudock notes.
Of necessity, refrigeration systems are designed with sufficient capacity to operate effectively under the most demanding conditions, on the hottest day. The key to economizing lies in a system's ability to match output with load, or what is known as "part-load efficiency," Lowery explains. In other words, how efficient is the system during periods of lower demand; how much less energy does it consume when conditions do not require it to run full bore?
"To do that, you need systems that can be controlled in ways that closely match demand, so that whenever they're operating, they're operating at 100 percent efficiency," Lowery notes.
One way to save on energy with refrigeration systems, as well as with any other motor-driven systems, including other HVAC applications, conveyor systems, and automated doors, is by specifying premium efficient motors, Walker comments. They cost more upfront but typically pay back the extra investment through lower energy costs within 18 to 36 months.
Variable frequency drives on compressors and other motors—a relatively new technology, the use of lower horsepower evaporators combined with larger refrigeration coils and systems designed to operate with lower condenser pressure are other easy-to-justify investments in part-load efficiency that can pay off for themselves fairly quickly—generally within two to three years, Lowery adds.
"When we work on refrigeration projects we typically look at total economic value, which means finding the correct balance between initial cost and ongoing energy consumption and payback," he comments.
In some distribution center applications, but more often in manufacturing projects, Stellar also incorporates CO2-based refrigeration to boost system capabilities while lowering energy costs.
"We can turn an ammonia refrigeration system into a CO2-ammonia cascade system through certain modifications, boosting throughput by a spiral freezer, for example, allowing it to bring temperatures lower more quickly." In these situations, Lowery explains, CO2 functions more efficiently than ammonia for lowering temperatures quickly, but because it brings temperatures so low, it's not typically applicable to cold storage.
"However there are a number of third-party warehouses that do batch-freezing of product, for example, a cold storage facility that brings in product from a local fresh chicken supplier and needs to bring the temperature down within 20 hours. We can take an existing plant and apply this kind of technology to make it considerably more efficient," he says.
Automating Savings
Automated energy management systems are another technology that can help distribution centers substantially reduce energy use. While not new, they continue to grow more sophisticated and affordable.
"They're almost becoming standard, at least for anyone running any kind of refrigerated facility," Hudock observes.
These generally PC-based systems allow operators to set a variety of detailed, conditional parameters to control energy use and provide alerts or notifications when conditions fall outside certain parameters or otherwise require attention.
A lot of their application is in zone temperature sensing and some zone lighting control, Hudock notes.
"The systems allow any types of fans, such as refrigeration or exhaust fans, for example, to be turned on and off based on what's actually happening in the warehouse. In addition to temperature, the system might automatically trigger controls based on doors opening and closing."
Systems are also typically used to provide alerts, such as if a door is left open for a particularly long time, or if the load on the compressors is running higher than normal.
"Any time you can turn off equipment when it's not needed, by automating the controls, you're going to save resources and money. It's all about matching the load with the equipment," Lowery points out.
"As computers have gotten more sophisticated, with more memory, and bigger microprocessors and sensor technology has improved, these energy management systems can now trend components more quickly, and based on more accurate and precise data on conditions," he adds.
The general consensus is that a good energy management system will provide savings of anywhere from 10 or 15 percent to as much as 30 percent or more of a facility's total energy consumption, making some form of automated energy management virtually a no-brainer today.
Every Little Bit Helps
There are many other things companies can do when designing and constructing distribution centers to minimize energy use and other negative impacts on the environment.
"One of the things people are starting to do in new construction is to use more reflective roofing material that doesn't absorb as much heat, especially if they're operating freezer or cooler space. I've heard manufacturers claim such materials can yield a seven to 10 percent improvement in overall energy efficiency. Even if the reality is only two to three percent savings, that can be a pretty significant gain over a building's life," Hudock comments.
"Looking at air movement, even doing something as simple as putting in larger fans to keep air circulating through a facility can help with HVAC costs. And better systems are coming out today that use multiple blowers or fans instead of a single large one, an arrangement that is more efficient and can also be tied into the energy management system, letting you control with more specificity where you need more heating or cooling," he points out.
In an older facility, simple improvements such as making sure you have good dock seals and dock doors can boost efficiency. Likewise, paying a little more for better insulation can play a significant role in reducing a building's energy consumption.
Something as simple as painting the inside walls white can improve lighting effectiveness, reducing the amount of lighting that must be supplied. The way a building is laid out also contributes to its overall efficiency, including energy use.
"A lot of it ties into basic best practices for operations, for reducing labor in general and making efficient use of equipment," Hudock observes. "Simply having items slotted in the right locations to reduce travel time and provide a good, clear traffic flow helps a lot. If people can drive or objects need only move shorter distances in the warehouse you may save a person, a fork lift, a section of conveyor and all the energy each of these would consume."
Similarly, Lowery points out, good preventive maintenance procedures on the refrigeration and other electro-mechanical systems in the warehouse save energy as well as money for repairs and replacement, making the whole facility more "sustainable." Moreover, designing a building's systems to be more part-load efficient and thus more environmentally friendly and economical to run, means the equipment has smaller motors which are less costly to replace when failure does occur, so the approach is a real win-win.
High-Tech Enviro-Friendly
Among the best ways to create an energy-efficient distribution center, in many situations, is to build a high-rise facility equipped with an automated storage and retrieval system.
"We've been involved in projects with ceilings as high as 100 feet, with just eight to 10 aisles of racks. Because the footprint is so much smaller in these vertically-oriented operations, the energy costs related to conditioning the interior are lowered substantially," says Walker. "Moreover, since cranes don't require any lighting to operate, the lighting can be kept to a minimum, only putting in what is needed for maintenance issues, which is another big energy savings."
While the ASRS system consumes some energy, it is considerably less than is depleted by a conventional, horizontally-configured, human operated warehouse, Walker notes.
"The more people you have, the more you have to condition the space," he adds. "Plus you even have fewer people on the road commuting, consuming gasoline and contributing dangerous emissions."
ASRS systems also involve fewer door openings than a traditional warehouse with workers on fork trucks or pallet jacks zipping around, Lowery notes, which helps cut down on the HVAC load.
No matter what type of equipment a distribution center utilizes, there are options within that configuration that can help that operation reduce energy use and improve efficiency.
With conveyor systems, there's a push in newer designs to make greater use of sensor-driven motor technology, so that the belt only operates when product is in the area, rather than running continuously through the entire shift. While the capital investment required upfront for a conveyor system so equipped may run about 20 percent higher, they typically consume from 20 to 25 percent less energy than a system in which all belts are always on during operation, says Hudock.
There are two different approaches to synchronizing belt movement with product movement, he adds. One is through an energy management system, or the conveyor management system installed in conjunction with the conveyor equipment. Since the conveyor picking system operates off optical scan data anyway, it's easy to feed this data into the energy management system, so that product movement through a scan point activates the conveyor motors on the belts in the affected zone.
Another, more localized approach relies on motor-driven rollers. In this case small motors located in each roller typically operate anywhere from an 18- to a 36-inch section of conveyor belt, and simple motion sensors placed at intervals along the beltway detect product on one section and automatically turn on the rollers on the next section for a given period of time.
Which system works best depends on the characteristics of each operation. Those controlled remotely by the conveyor management system cannot be shut off very quickly, and tend to work better with longer run times, since the system is looking at activity in terms of sections, lanes or zones. The equipment-driven solution can turn sections on and off more frequently, an advantage in operations or sections of an operation where product movement is sporadic, rather than organized in large waves or batches.
For traditionalists in non-mechanized operations, who depend on human-operated forklifts and similar equipment, there is a move underway from older-style DC motors to AC-powered trucks.
The initial cost of units equipped with AC motors is a little higher, but operating at close to 10 percent improved efficiency, the upfront premium is recouped fairly quickly, says Hudock.
There are many other operational practices that not only reduce energy use and help make you "a wise and good corporate citizen of planet earth," but also simply make good business practice, Hudock adds.
"Good maintenance procedures, preventive maintenance and care in operating equipment also tie into good energy management and use of non-renewable resources," he points out.
SECTION 2 / PALLETS AND CONTAINERS
Three 'R's: Reduce, Reuse, Recycle
Pallet pooling, resuable containers help reign in waste.
By Carol Casper
One key attribute of sustainable business is reduced energy consumption. Another is solid waste reduction.
The latter, like education, rests on the "three Rs." In this case the Rs stand for: reduce, reuse, recycle.
Companies need to look for ways to reduce the amount of resources they use, particularly in the realm of disposable packaging. The rule is to use the least packaging necessary to accomplish the task.
Recycling wherever possible also helps to conserve non-renewable resources. Food distributors, particularly grocery wholesalers, have less latitude to affect the total amount of solid waste that is generated by the supply chain compared to manufacturers and retailers.
"They tend not to break cases, so they're not disposing of a lot of corrugated," Andy Saladin with ORBIS Senior Engineering Services points out. And most packaging activities are outside their sphere of operation. Stretch-wrapping of outgoing pallets is one area that is getting a second look, he notes.
"Some companies are trying to reduce the amount of stretch-wrap they use, trying different kinds of strapping methods instead, for example. And vendors of the material are also pitching in, trying to find the lowest mil rating available (plastic density) that is sufficient to do the job well, in order to cut down on waste and improve resource utilization."
Probably the biggest area where food distributors can have an impact is in reuse of certain materials, in particular, pallets. In many warehouses, discarded wooden pallets represent their single largest category of waste.
The Pallet Conundrum: Wood Or Plastic
There are basically two approaches to controlling pallet waste: switch to sturdier materials like plastic, or find ways to make wooden pallets last longer. The average pallet manages about seven to 10 trips before it can no longer be reused, according to Curt Most, national pallet sales manager with ORBIS. "Then it's ground into mulch or if it's good enough quality scrap it might go into paper, but there's not a whole lot of value in broken wooden pallets."
Plastic pallets, on the other hand, are engineered to sustain anywhere from 150 to 200 trips on average, Most says.
"That's a lot of wood that doesn't have to be harvested and made into pallets and a lot fewer pallets on a lot fewer trucks that have to be shipped to a DC," he points out.
The environmental argument in favor of a pallet pooling system like CHEP's is similar, even if the mechanics are different.
"One of the intrinsic environmental benefits with a pallet pooling concept is that you generate less solid waste because you can reuse the pallets a greater number of times. There are a lot of pallets that were put into service in the 1990s, when CHEP was first introduced to the U.S., that are still in service," points out Per Ohstrom, CHEP director of marketing, CHEP pallets last longer because they are built stronger from the start and because the company, which rents them, has a keen proprietary interest in their maintenance.
In 2006 CHEP USA issued approximately 220 million pallets, Ohstrom notes. According to a company report comparing their use and longevity to standard "white wood" pallets, the use of CHEP wood prevented the generation of some 1.2 billion pounds of solid waste and 596 million pounds of greenhouse gases.
Which is better, pallet pooling or plastic? It depends on whom you ask and also on the specific application.
"With our block design, if any component breaks, we can just replace the broken section. When a plastic pallet breaks, you have to discard the whole thing," Ohstrom says.
The most frequent objection to plastic pallets is cost.
Most says this issue disappears once you break down the numbers to look at cost per trip.
"With an average wooden pallet, if you can get seven to 10 trips you're doing well, so you're looking at a cost of about 80 cents per trip. Average cost for a plastic pallet is around $60, which sounds like a lot. But getting anywhere from 150 to 200 trips from the pallet, your cost per trip is only about 30 cents," he points out.
Moreover, this cost advantage for plastic doesn't yet take into account all the factors that enter into true cost.
"The plastic in our pallets is completely recyclable. When any of our pallets breaks or is no longer usable, we'll buy it back. The average price paid is about 20 cents per pound or $10 per pallet. So now, taking that into consideration, you're looking at a true cost of only about 25 cents per trip." That still doesn't factor in the extra labor typically involved in inspecting, repairing and eventually scrapping wood pallets.
"While companies are definitely becoming more interested in the sustainability benefit of reusable plastic pallets, our strongest argument in their favor still comes down to economics," Most notes.
The main limitation with plastic pallets is that they don't generally make sense in most wholesale operations."When you spend $60 or more on a plastic pallet, you have to know you will get them back," Most acknowledges. "If you don't have 100 percent control over your pallets, it's hard to justify the investment."
However, for internal operations—moving product within a facility, or between plants and distribution centers operated by a single corporate entity, for example, plastic reusable pallets are an elegantly economical and environmentally-friendly solution.
"In the grocery industry, they can work very well for self-distributing chains, where you have dedicated trucks traveling back and forth between the distribution center and the retail stores," Most observes.
"We've also seen some companies form partnerships to do pallet exchange with plastic."
Reusable Containers Meet A Variety Of Needs
In addition to pallets, there are other kinds of reusable containers and shipping packaging available to meet a wide variety of specific needs.
"Reusable containers are nothing new," Saladin notes. "But we are seeing more companies moving toward reusable packaging and shipping containers recently, due to growing concern over the future of the environment and a desire to reduce waste."
Many retailers including drugstores and supermarkets have been using flip-packs (totes with attached lids) to move product from the DC to store shelves for years, Saladin notes.
"Recently a large chicken processor has started using plastic containers to move its chilled product through the supply chain. Because of the harsh environment the product travels through, with high levels of humidity, they've found that corrugated doesn't withstand the rigors of handling nearly as well as plastic containers.
"We're also seeing growing use of reusable plastic shippers in the produce industry, where you have product moving all the way from the field to the store shelf in the same plastic shipper," says Saladin. "Many of these containers, some of them collapsible, are now shipped right out to the store floor and used for display."
There are hundreds of varieties of reusable container configurations, some tailored exactly to specific applications. Another advantage these offer over pallets, slip sheets, and other methods of packaging product for shipping, is that they can be designed specifically to protect the goods involved, resulting is less damage and waste.
In general, reusable shipping containers make not only good environmental policy, but also great economic sense, Saladin adds.
"We've had studies done that show a return on investment in anywhere from six to 18 months, depending on the supply chain. Those are real, immediate dollar savings. When you add the environmental and other benefits, there's a lot of interest."
SECTION 3 / LIFT TRUCKS
Workhorse Gets Green Makeover
By Brian Schiavo
Lift truck manufacturers have not been immune to the "green" trend. In fact, companies such as Raymond, Crown, Hyster and Yale are finding new ways to reduce the impact that their manufacturing processes and their equipment has on the environment.
"We have a long history of environmental efforts and sustainability," says Brian Duffy environmental and safety manager for Crown Equipment Corp., New Bremen, OH. Crown manufactures a large percentage of the components that go into its lift trucks. This gives the company a distinct advantage in what happens during the manufacturing process, allowing it to apply its own environmental principles, down to the component level.
"Each component has an environmental strategy associated with it," he says. "In our mast plant, for example, we do welding and plating. Our component level strategy for that was to put together a zero discharge plating operation." This means the process generates no hazardous waste sludge. Even the rinse waters used during plating are re-cycled, making it a completely environmentally sound operation.
Crown was recently awarded an Achievement Award from the National Partnership for Environmental Priorities for one of the changes it made in its production processes. This one entailed switching from a liquid coating painting process for its power units and most parts to a powder coating process. The process eliminates all VOC (volatile organic chemical) emissions. The switch eliminated more than 65 percent of the wastewater generated by the old process and saves more than 200,000 pounds of water and sludge.
On The Horizon: Hydrogen Fuel Cells
Another trend that has been gathering an incredible amount of steam in the past few years is the utilization of hydrogen fuel cells to power lift trucks. Many of the major manufacturers are testing the viability of this alternative power system.
Cellex Power Products Inc., Vancouver, BC, is a supplier of fuel cell power solutions for electric lift trucks. Last year, the company concluded a successful beta trial in conjunction with Crown, at a Wal-Mart food distribution center in Ohio. It is now moving, along with its parent company Power Plug of Latham, NY, into an early commercial phase of the plan.
"We will begin to ship these units starting in the fourth quarter of the year," says Tom Hoying, vice president of sales and marketing for Cellex. "We're in the final throes of preparing 100 Class Three units for customers right now. After the second quarter of next year we will start putting beta units out in Class One and Class Two stand up-units."
Reasons for switching from lead/acid batteries range from the environmental—old batteries leak acid and lead into landfills—to issues of productivity.
"There's no battery droop," says Hoying. "Any lead battery, once it reaches 60 percent of its available energy, starts to drop off faster, which means the truck tends to run slow. Fuel cells run longer."
In addition, the downtime for lead/acid batteries is incredibly long, necessitating removal of the battery from the truck, as well as a protracted recharge time and a cool-down period before they can be utilized. In contrast, fuel cells can be filled with compressed hydrogen from a filling station—a process that takes minutes.
Raymond Corp., Greene, NY, is on the forefront of the research. "We realized, as a truck manufacturer, that we needed to understand not only the environmental and productivity issues, but also the technological ones," says Steve Medwin, manager of advance research for Raymond. "In the fall of last year we were awarded a large contract from New York State that partially funded our internal program."
As part of the program, Raymond installed outdoor hydrogen storage and compression as well as an indoor refueling area in their production factory. Fuel cells have been installed in a Class Three pallet truck, a Class Two reach truck and will soon be installed in a Class One stand up truck as well as another reach truck. The company is using the trucks in its manufacturing process.
"All of these systems are hybrid," he explains. "They have a fuel cell and they also have another way to store electricity." Raymond uses super capacitors for this function. "Hybridization is really key to the performance of the truck," Medwin says.
"When you're lifting a load 40 feet in the air, you need a burst of energy." Supercapacitors provide this extra energy for them.
"Currently, we are evaluating the technology," he adds. "We're using our factory as a living lab." The duration of the experiment will be two years, after which Raymond will evaluate the evidence and determine what role they should play in the supply chain.
Anti-Corrosion Trucks For Tough Environments
A few lift truck companies have begun to offer anti-corrosion packages for their trucks, which makes for more environmentally friendly, cheaper to maintain trucks. Yale Materials Handling Corp., Greenville, NC, offers a galvanization process for its MPW-050-W walkie truck. This helps protect the vehicle's surface in harsh environments, thereby reducing the number of times the truck needs to be painted. It also reduces the overall maintenance costs during the life of the truck.
Hyster, Greenville, NC, provides an Extreme Corrosion/Wash Down Package on selected versions of its pallet trucks that provides extra protection for trucks working in applications that require they be washed-down frequently, or in situations where they are exposed to corrosive forces.
SECTION 4 / PACKAGING
Gaining A Competitive Advantage
Follow these nine steps to optimize the packaging supply chain.
By Patrick Smorch
The announcement of Wal-Mart's new sustainability scorecard has established sustainability as a source of differentiation and competitive advantage for Consumer Packaged Goods (CPG) companies. It turns out that what's good for the environment can also be good for business. As companies strive to meet their sustainability goals, they can also improve efficiency, cost-savings and profitability.
CPG companies can uncover sustainability and profitability benefits throughout the packaging supply chain by focusing on the following nine key areas:
- Package design Package design plays a critical role in helping CPG companies achieve sustainability and profitability goals.
More efficient packaging can reduce warehouse, distribution and transportation cost and consequently energy usage and greenhouse gas emissions (GHG). The amount of GHG and Carbon Dioxide (CO2) emissions per ton of production accounts for 15 percent of Wal-Mart's packaging scorecard. Efforts to reduce these emissions can also improve a CPG company's competitive position relative to other suppliers.
So while CPG companies need to look at the big picture—the entire packaging supply chain—to uncover new sources of efficiency, waste reduction and cost savings, they also need to think "inside the box" with package design.
- Material optimization Material value represents 15 percent of the total sustainability metrics that will be measured by Wal-Mart's packaging scorecard. One way CPG companies can improve sustainability is by reducing the total fiber content of their corrugated boxes.
Fiber reduction is achieved three ways: by using an innovative package design that utilizes less corrugated board; by using less fiber within the corrugated board; and by using lower basis weight material. Quite often the best fiber reduction solution is a combination of all three.
Using a low-fiber package is a great way to improve packaging sustainability. However, removing fiber from corrugated board without compromising the integrity of the package can be challenging. Microflute delivers the strength of corrugated board with the high graphics impact of traditional folding carton. The result is a low-fiber package with Point of Purchase (POP) appeal.
- Shelf impact In club stores, secondary packaging often plays a primary role. In this dual role, secondary packaging functions both as a shipping container and a display package. Therefore, an optimized package can enhance function, increase shelf appeal and velocity and in some cases, even reduce store waste.
Recently, we redesigned the packaging for Dixie's PerfecTouch Grab N Go insulated 12 oz. paper cups. Paper cups are traditionally packaged in large quantities in polyurethane bags. The new package design allows for better placement of the cups on store shelves. The carton itself acts as an excellent canvas for a variety of designs as well as communicating the product's benefits to the consumer. It also fits neatly in kitchen cabinets or pantry shelves, further enticing the consumer to buy.
- SKU consolidation CPG companies with 50 or 100 different SKUs pay more for packaging because suppliers are forced to perform shorter production runs of myriad package types. The number of SKUs can be dramatically reduced by developing package designs that meet universal needs.
- Alternative packaging Alternative packaging can provide significant sustainability benefits. A good example of that is Greenshield. The produce industry traditionally uses non-recyclable wax coatings to protect the integrity of packages containing delicate perishables. As an alternative to wax-coated boxes, Georgia-Pacific's Greenshield family of products delivers tested strength and an excellent moisture barrier and is recyclable. Reusable plastic containers (RPCs) may also be used as a more sustainable alternative to wax-coated boxes. Georgia-Pacific is the only packaging supplier to offer customers both a corrugated and a plastic packaging solution—both options have sustainability benefits as well.
- Productivity improvements There are many opportunities in the packaging supply chain to improve productivity by focusing on automating manual processes. For example, significant efficiency gains have been made by automating case-forming and stretchwrapping processes. These processes not only enable more effective use of labor, but they can also reduce material costs.
- Material handling Safe, effective material handling is central to streamlined packaging supply chain operations. Like each of the nine key areas of the packaging supply chain, material handling optimization depends on countless variables that are unique to each company and facility. For example, an innovative corrugated box design may give new strength to a package that was previously susceptible to damage by a clamp truck.
Other techniques to consider include the use of slip sheets in lieu of pallets or stretchwrapping instead of strapping. Pallets can be costly to manage and store, while stretchwrapping may avoid damage from strapping. Conversely, some companies may find stretchwrapping and slip sheets inappropriate and expensive and instead may look for new ways to optimize existing strapping and palletizing processes. Only by closely examining dozens of variables that effect material handling can the best solution be found.
- Warehousing Efforts to optimize the warehouse can include creating packages that can stand up to the demands of the warehouse environment and make efficient use of warehouse space.
High humidity, storage time and stacking height can all erode the integrity of a stored package over time. The degree to which these factors affect box performance depends on individual package characteristics. Whereas the solution to compression failure for one company may be to reduce stacking height, the answer for another may lie in the use of a Bliss box over a traditional RSC to provide added strength that allows packages to be stacked even higher.
- Transportation The road to improved sustainability, rather appropriately, is often connected to transportation itself. This is because many of the sustainability improvements made farther back in the supply chain are realized during transportation.
More efficient, lighter-weight packages help reduce the number of truckloads, which result in reduced fuel usage and greenhouse gas emissions.
Equally critical to reducing shipments is cube utilization. In some cases, mixed products on pallets can contribute to poor use of space, while in others unit load height is not as high as it could be. Placing pallets in a "pin wheeled" position can maximize cube utilization and prevent excessive load movement in the truck.
CPG companies can gain a significant sustainability advantage by optimizing their distribution operations. This is reinforced by the fact that cube utilization and general transportation factors together will account for 25 percent of a CPG company's total score using Wal-Mart's packaging scorecard.
Top Of The Scorecard
If CPG companies are to stay competitive in a world of shrinking margins, rising costs and pressure to outscore other suppliers on Wal-Mart's packaging scorecard, they will have to leverage sustainability efforts into a profitable advantage. Opportunities to improve efficiency exist across the packaging supply chain, CPG companies need only find them.
Georgia-Pacific offers a program called Packaging Systems Optimization (PSO) to help CPG companies optimize these nine areas of the packaging supply chain. By providing quantifiable cost savings and measurable sustainability impacts, the program enables CPG companies to simultaneously realize sustainability and profitability goals.
With more than 15 years experience in the consumer products and packaging industries, Smorch leads Georgia-Pacific's Packaging Systems Optimization (PSO) program. Based at the company's Innovation Institute in Norcross, GA, he is responsible for delivering supply chain savings and measuring sustainability through PSO for both national and local packaging customers located across the United States.
SECTION 5 / TECHNOLOGY
Technology Fuels Green Efforts
Environmental challenges, practices for food manufacturers and distributors.
Environmental issues are here to stay. Global warming and climate change are the newest hypes in a long string of movements toward preserving our environment. Other areas of the green movement include reduction of pollution and preservation of natural resources.
In coming years, green movements will flourish through international policy initiatives like The Kyoto Accord as well as increasing consumer pressure. Industries will be forced to modify their processes to become environmentally responsible. Truly green strategies begin with well thought-out supply chain design and are enabled by internal operations.
A recent study from the U.S. Environmental Protection Agency reported that the food processing industry is among the largest of manufacturing energy consumers in the United States. The same study also concluded that improvements in processes "including changes in operating techniques to implement best energy management practices, [and] optimizing energy consumption in scheduling processing" rank very high in opportunities for environmental improvements. .
There are a number of ways that food manufacturers and distributors can improve efficiencies while also moving towards green production strategies. Some very simple process changes can be enabled by today's software solutions. Mulvany Attard Associates, a Canadian food industry software solution provider, offers these suggestions:
- Convert to a paperless office space. Use already popular technologies like web order entry and wireless tablet PC's will make your office space almost entirely paper free. The need for your Sales Reps or Customer Service personnel to write orders on paper will no longer be required. This will not only reduce the amount of waste that is produced but it will also eliminate manual, time-consuming processes and lead to shorter fulfillment cycles. The ability to email files such as invoices, customer statements, and purchase orders directly from your software also reduces the paper that gets printed and helps increase efficiencies
- Truck loading and route planning. Load and Route planning is a very difficult and time-consuming manual process. It often results in sub-optimal use of transportation resources. Using software tools to help you plan truck loads, maximize truck capacity and map-out routes will result in reductions in terms of fuel consumption while improving customer service.
- Using lot control. Software designed for the food industry enables you to track and trace products through the entire supply chain. In the event of a product recall, food distributors and manufacturers tend to err on the side of caution. They often destroy large quantities of product because they lack accurate information to precisely identify the product that is bad. Being able to track and trace products through lot control measures means that only the lots affected by the recall need be destroyed and minimal amounts of product will be wasted.
- Manage inventory efficiently. Track product by expiry date to help to ensure that oldest products are used first which consequently results in less spoilage and reduced waste. Use Just-in-Time techniques to help to determine optimal inventory levels and minimize inventory holdings to save on space and energy requirements.
- Warehouse management. Manual warehouse management techniques do not allow the full capacity of a warehouse to be utilized. Current warehouse management software enables significant improvements in this area. The ability to manage and maintain a tight control of warehouse space so that minimum amounts of space are required reduces operational energy costs.
- Just-in-time production scheduling. Simple production planning techniques enabled by relevant data can improve production scheduling. The ability to generate well-maintained production schedules means that equipment can be turned on only when it is needed as dictated by demand. In addition only product that is required will be produced.
Many executives in the food industry today are still reluctant to adopt greener production strategies. In an industry where profit margins can be so low, any reduction in efficiency is a gamble. Selecting the wrong solution can mean longer lead times, lower fill rates, reductions in customer service and even smaller profit margins. However, some green solutions do not necessarily have to be more than just improving on your own internal efficiency.
Today's companies can adopt sustainable production strategies that enable in-house reductions while maximizing process efficiencies throughout the whole supply chain. By making the food supply chain more efficient, we reduce the negative impact on our environment. All of the green benefits can be achieved by better planning and management of our supply chain.
Environmental pressures for manufacturers are inevitable. "Green" production and consumption habits are slowly becoming integral components of industrial regulatory policies and procedures. Through all the various environmental hypes and trends, consumers are beginning to use "green" attributes as a product selection criteria. How your company responds to this challenge may affect its future success.