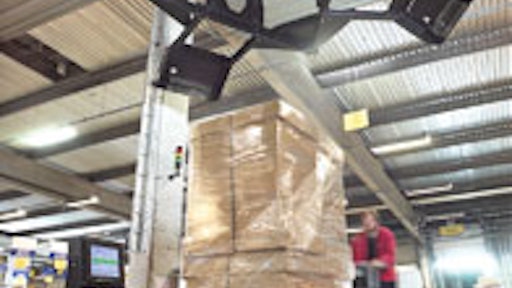
Transportation costs are skyrocketing. A tank of gas is edging up to $4 a gallon. With this trend going on, food and beverage companies are now looking for new ways to max out the cube in their delivery trucks.
Cubing system can enable workers to get the maximum number of items onto a pallet and the maximum number of pallets into a vehicle. It's all about helping today's fleet managers make the space they have available in their trucks do more.
First off, distributors need to know that there are several different methodologies out there to achieve the best cube. It depends upon how their workflow is set up and what type of software they've incorporated into their warehouse management system-and to use any of these solutions a WMS is required.
Dimensioning Devices
"With regard to a food distribution application, they'll often take a cubing device and put it in the receiving area," says Randy Neilson, director of sales and marketing for Quantronix, a Farmington, UT, company that builds dimensional scanning equipment. "That way they're able to cube and weigh all the new items that are coming into the facility."
Quantronix builds a variety of scanning equipment, such as the Cubiscan 100, which uses ultrasonic sensing technology to gather dimensions and weights on products as small as 0.5 inches and as large as 24 by 24 inches in length and width and 36 inches in height. This solution can be deployed on a mobile cart with a battery system. It also builds larger dimensioning devices such as the Cubiscan 150 and the Cubiscan 200-TL (a conveyorized model).
The goal is to keep the most accurate cube and weight information on all the SKUs a warehouse has in the master file of its warehouse management system.
Systems like Quantronix's work well for measuring the individual boxes that will eventually be going into cartons. With the proper cube information, a warehouse's WMS will be able to select the correct-sized carton that will allow workers to package orders most efficiently and get the best use out of cartons.
"You don't fill a box only half full," says Neilson. "Or fill one box and have three items left over, so that you have to utilize another box and put a bunch of packaging material in there to fill up the excess space. You end-up sending out boxes with a lot of dead space in them."
When workers put half-empty boxes in a trailer, the trailer itself, in effect, is only half-full. This results in companies sending out more trailers than is necessary.
Express Cube, based in Toronto Canada, offers a countertop dimensioning and weighing system that uses a passive, infrared sensor array. The choice of sensor units depends upon the preference of the user. In addition to ultras-sonic and infrared, many dimensioning units use laser sensors.
Express Cube also captures the dimensions and weights of items and brings them into a WMS, after which the information can be used to obtain the optimum use of space in a vehicle or container.
"From the standpoint of a person optimizing the trailer space, Express Cube gives the consistent data to be able to do that, as opposed to a person taking a tape measure and measuring a box or just eyeballing it, which is cost prohibitive," says Gordon Cooper, director of marketing for Express Cube.
Less expensive systems such as these make it possible for small- to mid-sized operations to get into the cubing and weighing game, as they typically cost in the $7,000 range. Larger systems, designed for higher throughput, can range from $30,000 to $50,000.
Measuring Pallets
Companies that aren't measuring the packages before they're putting them on the pallet will most likely need to measure the entire pallet after they've built it. Mettler-Toledo Inc., a Columbus, OH-based provider of precision instruments and services to the food and beverage industry, offers a device for just such an application-the CSN840 Pallet Solution. The CSN840 can capture the dimension, weight and identification code of almost all pallet shapes and sizes in less than three seconds. The ceiling-mounted design allows operators to place pallets directly under the measuring system.
"If you're worried about palletizing a truck to cube it out, the CSN840 is able to perform a very large scan and it will give you all the attributes of a full pallet," says Jerry Stoll, marketing manager, strategic accounts, for Mettler-Toledo. "Every pallet is slightly different, so it's an on-going process. A system such as this can capture the dimensions of a pallet before you load it and if you have load planning software like Maxload or Q by Q, you can interface our system right into their software and plug these dimensions in it and be able to cube out the truck more effectively."
A system like the CSN840 is also advantageous for companies that do a lot of less-than truckload shipping. If a distributor is only shipping a few pallets at a time and is relying on an LTL carrier, that carrier is requiring the customer to give them the actual physical dimensions of the pallet in order to know how much space to set aside on its truck-space the customer pays for whether he uses it all or not.
"If you're out there with the tape measure, it becomes kind of cumbersome and inaccurate," says Stoll. "If they have the correct imaging system, like a pallet dimensioner, they can be sure the dimensions they're giving to the shipper are correct."
Quantronix's Neilson cautions that cube information is only as valuable as the computer system that is using that data. If a company has a good computerized warehouse system that can utilize the cube information, then they can take advantage and realize the savings.
Load Planning Software
For a dimensioning system to truly be of value, a warehouse has to be able to send the dimensional data to some type of software system that can use that data, such as load planning software. Basically this software takes all the dimensions of the items going onto a pallet-and is also aware of what the height, length and the width of that pallet should be-and it builds the pallet, helps workers stack pallets and also enables them to load their trailers most efficiently.
Advanced Logistics Systems Inc. is a logistics consulting and custom software development company that creates solutions designed to meet and manage the packaging, palletizing and loading needs for the food and beverage industry. Their Advanced Loading System software is a 3-D palletization and load diagrammer for optimum placement of floor-loaded products and pallets into trucks and railcars.
"SAP systems feed their orders into our software and it then calculates the orders," says Robert Ahbel, senior partner at Advanced Logistics, which is based in Friday Harbor, WA. "How robust your load planning software is becomes really critical at this stage in the process, because if you can't build stable, stackable pallets, typically you're going to end-up running out of pallet spots on the floor of the truck."
Ahbel notes that companies that utilize advanced loading systems can take their fleet of, say, 50 38,000 pound trucks and up the cube and weight utilization of each truck so that they're only shipping 45 trucks a day. "If those are $1,000-a-day trucks, it's very easy for even companies of moderate size to be able to pay for the automated load planning solution."
The use of such a planning solution has added-value beyond just maximizing the space in company trucks.
One other thing to take into consideration is the quality of the pallets that workers are building. If left to their own devices, workers may not optimize the weight distribution of the material they're placing on pallets. They're simply drawing from a pick list and placing the items on a pallet as they pick them. Typically, they'll place as much on it as they can until they can't reach the top of it. Or they build an overweight pallet.
"You can't build a seven-foot-tall bleach pallet and shrink wrap it," says Ahbel. "The first time they hit the brakes, the bleach is all over the place. Worse yet, if you have a new worker and they put the bleach on top of the soap powder, the soap powder gets saturated with the bleach and you have a big green cloud of chlorine gas!"
Many types of load planning software allow for the inclusion of a company's business rules in the process, thereby eliminating any potential QA, enforcement and training issues.
Another benefit involves the Electronic Data Interchange (EDI) process. More and more, venders are pushing receiving costs associated with EDI back to the suppliers by demanding EDI. This issue is eliminated with the usage of advanced loading software. Because pallets are planned in advance of their creation, companies don't need to capture what the worker managed to load on the pallet-they already know. They directed that worker to create the pallet with a list printed out via the software.
"To do a QA on the pallet, all you have to do is a simple weight check," says Ahbel. "If the weight comes out correct, it's very likely that the correct material in the correct quantity is on the pallet and then you can send the EDI transaction to your business partner."