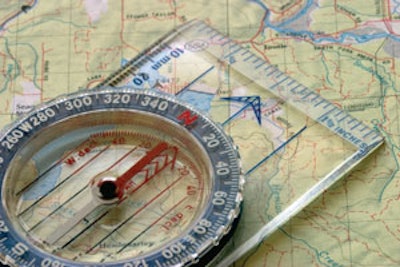
Choosing the right location to expand or consolidate food distribution operations is a challenge that many organizations are faced with. In these days of economic uncertainty, choosing the wrong location can be financial suicide.
Companies need to do their homework in the initial phase of the project to determine what their objectives are, not only for the actual site that they choose to locate at, but also in relation to their products, the location of their markets and the logistics models needed to get those products to the market in the fastest and most cost-efficient way possible.
The business of site selection should begin with companies identifying where their pain points are.
"It starts with primary issue identification," says Jeffrey Karrenbauer, president of Insight Inc., a Manassas, VA-based supply chain, software and consulting firm. "You need to think about what's bothering you."
Pinpointing concerns, he believes, can go a long way to actually determining what the objectives for a new site should be.
Matthew Schlosser, senior manager of supply chain strategy for Hershey, PA-based The Hershey Co., suggests limiting the site selection process to one or two exclusive goals. "You can't have a lot, because you're going to be dealing with numbers and then you set objectives from those figures. That's how you get cross-functional alignment."
Being able to name an initial goal naturally gives rise to factors such as these, as well as others such as inbound and outbound transportation costs, holding costs and inventory costs. These will all help suggest site locations and if a company is not using accurate data, or they're guessing at what the figures are, by the time all of the information forms a modeling perspective-which is what informs actual site selection-the location that is chosen will likely be off by quite a bit.
"Your data integrity is more than a little important because it helps you determine the direction you should go," says Hershey's Schlosser. "You know the size of the building you need, you know the service territories you want to be in, you've gone out and gotten real rates-the math will tell you where to go."
Otherwise, you could wind up in LA, when you really need to be in Vegas.
Land
Everyone wants to keep costs down these days. It's not so easy when you're looking to site a new facility and land costs are through the roof, especially if your company is looking to locate near an urban center such as New York, Atlanta or Los Angeles. This makes it prohibitive to build a warehouse in close proximity to such an area. However, companies should be wary of letting the quest for cheap land lead them to locating their DC somewhere in the hinterlands, where access to intermodal transport is limited.
"It doesn't matter how efficient your distribution center is in upstate Minnesota if you can't get your product rapidly to your customers," says Andrew Chesley, a consultant with Global Springs, a Concord, NC, firm that consults on site selection. "From a cost basis, everyone should be in upstate Minnesota, but in reality no one is."
Companies that need to be close to urban centers of population, yet still keep the cost of land down, might want to look at some of the smaller markets around those areas.
Leasing is another consideration.
"More and more, companies don't buy the land," says Paul Evanko, senior vice president, St. Onge, York, PA.. "They end up working out a leasing arrangement."
He says the reason for the popularity of leasing is that today's networks have to be fluid due to changes in the business environment. Generally, today's leases run for three to five years, with options.
The experts suggest that companies keep their future objectives in mind when selecting land.
"Whether they're building a half-million square foot facility or leasing an existing site, companies should determine whether there are expansion capabilities on the same parcel of land," notes John Hurst, vice president of warehouse management services at APL Logistics, Oakland, CA. "Can they get options on the land to build out if they need to? If it's an existing building, is it expandable?"
The Building
Building costs are another enormous expense that companies must consider when looking at new sites. This is where knowing your priorities and objectives can bring unexpected windfalls.
"The escalating costs in construction have made the existing facility approach a priority for the vast majority of companies out there," explains David Norrie, senior vice president and co-director of the Food Facilities Group at CB Richard Ellis, a company that represents the owners and users of food industry real estate. "Companies need to ask themselves ‘do we have a chance to find an existing facility that works for us or that we could modify to fit our needs?'"
According to industry experts like Global Springs' Chesley, the cost of a facility is one of the largest considerations a company has. It's also an area where you can find some fairly large differentials. However, it requires you to be careful about specifying your needs.
Chesley relates the story of Kal Kan, a former client. The company was looking to relocate to a new facility. Kal Kan maintains a high volume of product, on the order of 2,000 pallets of each SKU, with a relatively small number of SKUs, approximately three or so.
"They were getting a trailer out of their factory every 18 minutes and then another trailer would arrive. And this is 24 hours a day, seven days a week. Obviously if trailers arrive at that rate, they have to go out at that rate or you run out of room very fast."
Chesley says that the building that worked best for the company was an older one, not very tall by today's standards and, because of the lack of height, it was quite inexpensive relative to other buildings.
Market
Proximity to one's customers is an extremely important consideration when deciding upon a new site, whether it's for a stand-alone DC or one that will fit into a larger distribution network. A company needs to analyze what its objectives are in terms of how to best serve its particular market niche and factor that into the new location.
"If you are a large consumer products company, like Kraft, you're shipping to distribution centers and there is some leeway in terms of how close you are to your customers," explains St. Onge's Evanko. "If you're a supermarket company and just delivering to stores, you'll need very close proximity to them in order to provide the type of delivery service that a store typically expects."
Companies need to factor in customer service objectives as well. What kind of service do they want to provide to their customers? Is it short lead time and/or high availability? What if you have to be located next door to them? What level of confidence do you wish to instill in the people you are doing business for?
"Throughout history there are many examples of accounts that have been won by a sales organization with the promise of putting a warehouse right next door to the customer," says Terry Harris, managing partner of Chicago-based Chicago Consulting. "Understanding what customer service is and what they need is an important step. You need to create a clarification of what your customer service will provide."
Part of this is a clear understanding of the client-what its physical inventory requirements are and what they will be in the future, so that a company positions itself, in terms of warehouse space, to meet it. Companies should also be aware of what their own internal plans are for growing the markets that they're pursuing today and position themselves in the correct geographic position to enable those plans.
Supply chain optimization should be another objective in relation to serving a company's customer base. Companies need to take a "big picture" overview of where their other warehouses are located in relation to a new one they're looking to site.
Are all of the DCs mirroring each other? Will there be any substantial overlap in terms of areas served?
"Do they all perform the same type of execution and deliver the same type of product?" Asks APL's Hurst. "Do they really need six or seven identical warehouses or can they mesh the mix, in order to have two primary DCs and five feeder DCs that are closer to the customers. Perhaps the rationalization of their SKU's is that five feeder DCs can handle 80 percent of their faster moving items."
Also, is the demographic for the new DC substantially different? Will they serve a more specialized customer base in a particular area?
"Some warehouses specialize in one sort of thing or another, unless they're serving a similar customer base. However, if they're not serving the same type of customer, they should consider specializing them," explains Chicago Consulting's Harris.
Another factor to consider when examining a company's market objective and the number of warehouses required to meet that objective is inventory cost. The simple fact is that the greater the number of warehouses a company maintains, the higher the inventory costs associated with them.
"It requires more inventory if you divide the country up into smaller territories that are being served by more and more warehouses," says Harris. "In effect, it's taking you more inventory to provide the same level of service. Remember the old saying-if the inventory's in one place, it cannot be in the wrong place."
Some experts caution against adopting what they see as a "micro-view" when doing site selection.
"A lot of people use specialized tools that are myopic. They look at line balancing, capacity utilization, but they really ought to be doing that kind of macro production planning in the context of the entire supply chain, rather than just looking at a few manufacturing locations and trying to balance them," says Insight's Karrenbauer.
"People ask us how many warehouses they should have and where they should be located, but we encourage them to think in the much broader terms of designing the entire supply chain."
The typical supply chain encompasses procurement and raw material supplier locations, manufacturing locations, finished goods locations, cross-docks, ports, as well as intermediate nodes-not positioning the new site in conjunction with all of these can lead to dismal results.
Logistics
Perhaps the largest consideration involved in siting a new DC, in terms of dollars, is outbound transportation. It is estimated that this accounts for anywhere from 60 to 70 percent of total operating costs and if a company fails to write an accurate transportation analysis, chances are they will not be able to choose their site's location accurately.
A company needs to ascertain the logistical models required to bring goods into the facility, as well as transport them out. As the cost of fuel continues to rise unabated, this subject will only grow in importance.
"It's easy to rack up a million-plus differential in outbound transportation costs and when we do site studies over-and-over again, where we add up the dollars, it's not electrical costs, it's not taxes, it's not labor, what really makes the difference is outbound transportation dollars," notes Global Springs' Chesley. He adds that the type of facility a company is looking to site also comes into play. Regional DCs that are shipping to retails stores may use different transportation methods than national DCs, whereas manufacturers creating large quantities of goods may use rail to get their products to the next tier in the supply chain. It's not enough to say ‘a truckload from Point A to Point B costs "x" per mile and therefore we should cite our facility here.' Most people have a more complicated transportation structure than that and use a mix of modes-perhaps some rail, LTL carriers or truckload carriers. It depends on what sort of distribution they're doing. Food distribution takes in a whole lot of territory."
In addition to distance from markets, companies need to keep in mind the logistical situation revolving around where the actual site is located. Does it have easy access to major thruway systems? It is located near highway arterials and interstates? Do you need proximity to a port or the rails?
In addition, companies may want to consider locating in areas where there is a more competitive trucking market and they can negotiate with shippers for the best rates for over the road shipping, if they don't maintain their own fleet, that is.